So who knew, 12 months after the year started, that 2011 was going to end up a record-breaking year for industrial laser revenues. I for one didn’t, even after the 2010 sales were adjusted upward by 10% in February of 2011. And the same held true for laser systems sales after a 4% adjustment.
What had us, and a broad cross-section of economic analysts, spooked was the specter of a double-dip recession. We were being bombarded by the media’s obsession with it, based on continuing high unemployment in the US, economic woes among the Euro block nations, and a government check on inflation in China. And if that wasn’t enough, our friends and colleagues in Japan were pounded by an earthquake and tsunami that wiped out a significant portion of the country’s energy resources, forcing several months of power restrictions.
Now that’s a plateful of woes that should cause any self-respecting analyst to run for cover under the mantle of a double-dip recession. Well, guess what folks, it didn’t happen. It came close occasionally, causing emptied aspirin bottles, but we struggled through, although our friends on Wall Street developed ulcers over the every-other-day pattern of threatened economic disaster in the Euro Zone later in the year.
Through all of this, the quarterly news from the industrial laser community was continuously good. As the year progressed, it got better, and then by the end of the third quarter, it convinced ILS and others that 2011 was going to be a winner. A winner by a long shot as prime market sectors defied the analysts and turned in company after company success stories.
Even so, we were continually questioned as to how this phenomenon, a strong and growing manufacturing sector in an overall mixed economy, could be happening. Then it occurred to us, and a few economists, that the consumers who usually drove the economy by spending on food and household needs, had shifted their buying pattern to non-essentials. It seemed as if the buying public was sick of the tight restrictions of the previous two years and was saying, “recession threat be damned, let’s buy a new car.” And they did; 2012 was a record year, similar to pre-recession years for new car sales in North America, and the main reason was the return of small SUV and light truck sales.
We analyzed the laser markets that were having an excellent business year and found that several, semiconductor and medical devices for example, had weathered the recession and come out of it stronger and more profitable and were poised for further growth. Also other sectors, such as energy (conventional and alternative), were expanding and investing in capital equipment. Transportation, on the ground and in the air, was booming as airlines couldn’t order planes and engines fast enough, and the auto industry had bet on the right downsized vehicles and sales were booming. And market stalwarts such as fabricated metal products, aerospace, and microelectronics, comprised of a multitude of small and medium companies, found financing to commit to capital equipment.
Overview
So the table was set for a banner year in industrial laser revenues and we didn’t experience the disaster of the 12th month of 2008 when the phones stopped ringing in sales departments. As shown in TABLE 1, the industrial laser community experienced two strong double digit growth years in a row, and 2011 saw the laser system industry shatter the $7 billion ceiling to set a new high of almost $7.1 billon. Laser sales also zoomed by the old 2008 record by 12% to a record high of almost $2 billon.
The financial reports of the three dozen leading industry companies were all positive in 2011, and many of them set records for sales and profits. At every industry trade show, optimism reigned supreme as record numbers of visitors, many in a buying mood, buoyed the confidence of company salesmen. As the last month of the year approached, order books at leading suppliers were full and bookings for the first quarter of 2012 were rapidly filling the production floors.
TABLE 1, a four year summary and projection of laser and systems sales, shows the turning point as the industry began its recovery from the recession (2009) and the rapid growth to new highs in 2011, with a modest expansion forecast for 2012. The infamous “fishhook” curve, FIGURE 1, took on a more typical look as the CAGR for the past 25 years of industrial lasers, including the disastrous recession, was a more typical 12.52%.
What is significant is that in 2010 laser system revenues surpassed the previous high in 2008 and that laser revenues almost matched the 2008 record, passing this by 12% in 2011. So the pain of the recession felt in 2009 disappeared.
A look at the details of global laser revenues, TABLE 2, shows that CO2, fiber and “other” (diode/excimer) lasers experienced solid double digit growth in 2011, with fiber lasers enjoying a strong 48% growth led by sales of high-power units for sheet metal cutting, a relatively new market for these lasers. Solid-state laser sales continued the pre-recession low growth pattern as fiber lasers cut into sales of lamp-pumped and diode-pumped solid-state units used in marking and microprocessing applications. It appears that as the market for fiber laser marking systems is now essentially a consumer one with sales being price driven, then the suppliers are turning their attention to the microprocessing market that has long been a prime market for solid-state laser suppliers. Since TRUMPF (SPI), Rofin (Nufern/Lasag), Coherent, and Newport/Spectra Physics (High Q) are major suppliers to this market, only the latter two may experience a revenue change as they do not offer a fiber laser as of this writing.
Low-power CO2 laser sales, centered on Asia (China), continue to grow, but the pricing pressures from competition and end-users has made profitable sales a function of sales volumes. Margins are slim even when shipping thousands of units. High-power CO2 laser sales posted a surprising 14% gain as buyers of sheet metal cutting systems, still primarily job shops, managed to find financing in an otherwise tight credit environment. Even with sheet metal market erosion brought on by surging high-power fiber laser sales, the long-entrenched CO2 systems sector showed a 13% gain.
The question of the hour at the annual Fabtech show was how much market share will fiber lasers capture moving forward. Because only one of a dozen CO2 systems suppliers at this show did not also offer fiber laser units, it was difficult to get a straightforward answer to the market share question. Current penetration of about 15-17% is expected to grow to 25% in the coming year or so, and the bulk of the increase will be with traditional buyers. Thus, the total market growth will not be greatly affected as it will when fiber laser systems find a new untapped market, such as a replacement in the high-density plasma market.
Fiber laser revenues and the performance of industry leader IPG Photonics have the interest of the investment world, rightly so, as shown in TABLE 2, where global fiber laser revenues grew 48% in 2011. At industry trade shows and numerous conferences, such as the Laser Institute of America’s ICALEO, the hot topic was fiber laser processing, specifically applications for high-power fiber lasers. At the last two big international fabricating shows in Europe and North America, all eyes were on the fiber laser cutter exhibits, as crowds of enthusiastic potential buyers kept exhibitor personnel hopping.
Not to take anything away from fiber laser successes in the metal cutting market, but an interested observer hanging back in the crowds at several product demonstrations was surprised to hear from potential buyers that “I don’t know what a fiber does that CO2 can’t, but we better look at this.” And standing in lines for refreshments, it was common to hear fiber lasers being the topic of conversation. So the buzz is there, and suppliers are riding the wave of industry interest to draw potential buyers to their products.
Meanwhile, sales of low-power fiber lasers for marking and microprocessing applications continue to take market share from solid-state and low-power CO2 lasers. Combining annual sales of both technologies resulted in market growth in line with past years. One conclusion is that fiber lasers have yet to find a new application of size that will move the market at a higher pace. Development work by the suppliers and leading research laboratories shows promise to open those new markets the industry desires.
Significant growth in the acceptance of high-power direct diode lasers for industrial use has resulted from the successful transfer of application technology from the laboratory into industry, Showpiece applications in laser brazing for automotive applications has finally lifted diode sales to a visible number. Credit goes to system integrators such as Laserline Inc., which has made some key installations that show the operational benefits of this underused laser technology. Coupled with progressive work to improve beam quality for possible focused beam applications, diode laser suppliers promise strong growth potential for this laser, which has been dubbed, “the perfect laser” for inline manufacturing operations.
System revenues, TABLE 3, paralleled laser growth numbers in 2011, again led by the growth of high-power fiber laser cutter sales (38%). However, it was the almost ½ billion dollar increase in CO2 lasers, primarily high power that trumped the fiber lasers almost $400 million increase. Together this almost $1 billion revenue increase was the major factor in the 16% growth of the system business.
The question that plagued analysts through 2011 was how the industrial laser market was experiencing such outstanding performance in an international manufacturing market that spawned more bad news than good news? ILS identified six sizeable market sectors that were defying the economic malaise taking place in three continents: aerospace, energy (conventional and alternatative), electronics, fabricated metal products, and transportation. Companies in these industry sectors were experiencing demand for their products that exceeded the rather poor market prospects for other products such as appliances that were feeling the fallout from the housing industries woes. Prompt action by the banks in China reversed that country’s efforts to control inflation that had caused a steep drop in capital equipment investments, thereby saving jobs in companies in Europe that have China as a major customer for their products.
ILS easily identified more than two dozen laser applications that showed market strength in an otherwise dull manufacturing year. These range from turbine component drilling to battery welding to solar cell processing to smart phone glass cutting to automobile roof brazing. Finally, the often derogatory terms of “niche” or “diverse” to describe the industrial laser markets became words of praise for the industry’s ability to survive what had threatened to be a double-dip global economy.
Overall, the industrial laser market gained almost $300 million dollars of revenue in 2011 and ended the year with many leading companies showing full order books, leading to solid first quarter 2012 shipments.
Lasers for metal processing
FIGURE 2 illustrates the dominant role that high-power lasers for metal processing play in laser sales, with more than double the revenues of all the other applications. One half of total laser revenues are for CO2 lasers, which also represent 42% of the units shipped, thanks to the more than 20,000 low power units sold. The average unit list price for sheet metal cutters has increased due to the higher power lasers, CO2, or fiber, used to power the process. ILS does not account for any systems automation associated with these units, which are normally sold with material handling accessories. It is estimated that about 25% of all systems sold have these accessories, raising the selling price on average by at least $155,000, bringing the total metal cutting revenues to well over $3.2 billion.
TABLE 4 and FIGURE 3 detail the metal processing market by industrial laser type. Not surprisingly, CO2 lasers dominate sales in this application, but notice the almost 70% growth for high-power fiber lasers. Estimates for 2011 sales of kilowatt level fiber lasers range to 700 units, most used in metal cutting systems. CO2 laser sales showed strong growth in 2011 as the markets served by OEM suppliers integrating these lasers were among those mentioned earlier as “recession-proof”. Suppliers in the US faced difficult times with customer’s system financing. Many cited this as a roadblock to additional sales in a vibrant market.
Lasers for microprocessing
TABLE 5 and FIGURE 4 show the market breakdown for lasers used in semiconductor and microprocessing applications. This market grew 23% in 2011, led by sales into the microprocessing sector for applications such as: printed circuit board drilling, solar cell ablation, smart phone display processing, and telecom component welding. This is a diverse market sector with a heavy concentration of installations in Asia, for example, the hyperactive market in Taiwan for PCB drilling.
At the start of the year 2000, ILS identified microprocessing as one sector that offered good prospects for growth. Just as the forecast looked to become reality, the industry was hit badly by the recession. On the other hand, the semiconductor industry, mainly in Southeast Asia, managed to survive the recession in good shape, generating sales that enabled some equipment suppliers to ride out the recession in good shape. It is expected that ultra-fast pulse (UFP) laser sales — now doubling each year — will act to drive market growth for the next few years. In our market survey, UFP lasers are included in solid-state sales numbers.
Lasers for marking/engraving
Marking and engraving has been, and continues to be, a strong market for industrial lasers, as seen in TABLE 6 and FIGURE 5. These markets are controlled to a degree by government and industry regulations geared to security, warranty and traceability requirements, and these are proliferating. Since most call for permanent, legible marks on a wide variety of materials, including ID cards, aircraft components, and automobile VIN tags, lasers are the choice today, and are used in increasing numbers. These uses will only grow as the years pass.
In 2011, more than 22,000 solid-state and fiber lasers and 11,000 CO2 lasers were installed for marking and engraving applications, with a major market for these products in Asia. Fiber lasers continue to take market share from the diode-pumped solid-state lasers. As shown in TABLE 6, fiber laser suppliers enjoyed a 34% increase in 2011 sales, while solid-state sales only grew 4%.
The ubiquitous “Other” market is becoming more defined as the sales of direct diode lasers have risen to the level where they may be entitled to their own category in the next few years. Sources place diode unit sales at about 1300 units, with most of these in the microprocessing and marking sectors.
Other applications
TABLE 7 and FIGURE 6 detail the lasers used in a variety of applications not covered by the previous comments. Grouped in here are lasers used in additive manufacturing, surface treatment, heat treating and rapid manufacturing. This is not a large market at $127 million in 2011, and it is dominated (43%) by solid-state lasers, which are expected to be replaced by fiber lasers in the coming years.
In this “other” category” may be the seeds of new applications that may be industry growth drivers in the coming year. For example, laser additive manufacturing (LAM) is a term that encompasses laser cladding as its key process. LAM has its roots in the early days of high-power CO2 application development in laser cladding and glazing. Over the years, these applications have had a small number of successes, but it wasn’t until advanced process development work in Eastern Europe and China, where high-power lasers were being used to repair and refurbish worn metal components, began to be presented at international conferences. As companies in the more developed countries began to limit some manufacturing operations to accommodate low quantity demand for certain products, they noted the ability of lasers to manufacture quantities of one through laser assisted manufacturing. Now the process is under widespread evaluation in a number of key industry sectors and prospects for rapidly growing markets are begin identified.
Installations
Tracking the installations of lasers in the global marketplace has always been a process made difficult by the limited availability of official surveys and reports. An example of this is the laser market in China, which is not officially presented to the public until some years after the fact. Therefore, analysts depend on reports from publically traded companies such as Han’s Laser, the leading Chinese manufacturer of industrial lasers, and the information gleaned from contacts in the industry. As shown in FIGURE 7, the East Asian market now surpasses the former leader Europe (32%) as the location of 33% of all lasers systems installed. China is the major user of industrial laser systems in the region, probably placing as much as 85% of all East Asian installations.
Taken together with the now-stagnant market in Japan, Asia represents the location of 48% of all system sold. It is likely that China’s recent move to expand exporting products to the rest of the Asian market to compensate for slowing market growth in the US and Europe will force industry in other domestic markets to gear up to stay competitive, and this can become a fertile market for industrial laser products. As a result, Asia will remain the major market for several years to come, especially as manufacturing in India gets its act together and exercises its goal to be the dominant exporter of goods to the rest of the region.
The market in European countries in 2011 was flat, reflecting the roller coaster like ride that their financial reporting took as the Euro was under attack with one country after another going to the verge of bankruptcy — threatening the entire Euro Zone. As this was being written, the Euro remaining as the common currency was questionable, and the fallout from this was likely to negatively upset the economies of all the partners.
North America (essentially the US) held its 16% share of installations thanks to a vigorous export market led by the international demand for US manufactured products, such as in the agricultural, heavy equipment and aircraft industries. The ubiquitous green hats of John Deere equipment users show up on Web reports from all over the globe, more so today in Africa and South America, two markets for lasers that are counted in the ROW category of FIGURE 7. The former is years away from being a factor but the latter is now a target for many of the industrial laser systems suppliers, and ILS is considering how to identify this growing market (now mainly in Brazil) in future reports.
Forecast
For all the reasons cited earlier as growth drivers, changes in them will lead to a softer market for industrial lasers in 2012. A selection of headlines late in 2011 is illustrative:
- “European Machine Tool Builders Warn of Slowdown” (http://www.americanmachinist.com/Classes/Article/ArticleDraw.aspx?CID=88238),
- “Chinese Manufacturing Output Contracts for the First Time in 33 Months” (http://www.industryweek.com/PrintArticle.aspx?ArticleID=26100&cid=NLIWD),
- “India’s Growth Skids to 6.9 percent” (http://www.canadianmanufacturing.com/general/india%E2%80%99s-growth-skids-to-6-9-per-cent-48887)
- “America Must Learn From Germany — Before it’s Too Late” (http://globalpublicsquare.blogs.cnn.com/2011/10/24/america-must-learn-from-germany-before-it’s-too-late) and
- a thought provoking “10 Threats to China’s Economy” (http://citywire.co.uk/money/10-threats-to-china-s-economy/a534419).
Then there were the magazine headlines: “The (High) Cost of Manufacturing in America” (Industry Week, November 2011); “China’s Bind: How to Avoid a Crash Landing” and “Manufacturing Slows Outside US” (both in the Wall Street Journal, December 2, 2011); and “Battery Companies in Need of a Boost” (Wall Street Journal, December 5, 2011). However, there was some good news in the November Industry Week magazine (www.industryweek.com) – “Brazil is Booming”. The daily Steel Guru (www.steelguru.com) turned negative on the markets for steel early in October, where news items listed gained in negativity as this is being written.
We have labored over this forecast because on the one hand we have a fragile manufacturing economy held in place primarily by Asia (China) and on the other hand some key industries that are strategically strong that are major industrial laser users. In this latter category is the market for fabricated metal products, a basic industry that is key to developed countries — manufacturing economies. If, for example, sales of laser metal cutters were to decline due to slow markets in these countries the sales of high-power lasers would immediately be affected, see December 2008 as an example. A slippage of only 10% in laser cutter sales means a drop of $300 million in total system revenues, wiping out 30% of the 2011 revenue growth. So you can see our concern for the fragility of the international markets.
As this forecast was being prepared, the general prognosis, from a multitude of sources, was that 2012 would be a flat to a low growth year, depending on the sectors being reviewed. Even TRUMPF, the largest laser and systems supplier, cautioned that it, in all likelihood, could not match the 51% growth of its 2010/2011 year, but that the company expected to at least show double digit growth. Since the company’s fiscal year will include six months of the industry record calendar year 2011, this forecast seems doable even if the 2012 market is softer.
After much contemplation of the known facts and assessments of the forecasts of basic industry suppliers, i.e. the steel industry, we have settled on a 5% growth in laser revenues and a 4% growth in laser system revenues for 2012. We think these numbers are achievable given the current status-quo of the industrial markets. We see a strong first quarter followed by a slowing in the second half of 2012 with the year ending on a modest growth. We keep trying this forecast on everyone we interact with and have yet to find any violent disagreement. A low double digit growth year on top of a record year is not all that bad.
One last statement in the form of a qualification: I did not predict the record year of 2011 when I made the forecast in last year’s review issue of this publication. I had laser revenues for 2011 at a 16% increase and systems by 14%. Close but no cigar, as they say, and the CAGR for the past four years is 10.83%, not far off the 25 year number.
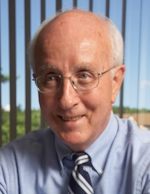
David Belforte | Contributing Editor
David Belforte (1932-2023) was an internationally recognized authority on industrial laser materials processing and had been actively involved in this technology for more than 50 years. His consulting business, Belforte Associates, served clients interested in advanced manufacturing applications. David held degrees in Chemistry and Production Technology from Northeastern University (Boston, MA). As a researcher, he conducted basic studies in material synthesis for high-temperature applications and held increasingly important positions with companies involved with high-technology materials processing. He co-founded a company that introduced several firsts in advanced welding technology and equipment. David's career in lasers started with the commercialization of the first industrial solid-state laser and a compact CO2 laser for sheet-metal cutting. For several years, he led the development of very high power CO2 lasers for welding and surface treating applications. In addition to consulting, David was the Founder and Editor-in-Chief of Industrial Laser Solutions magazine (1986-2022) and contributed to other laser publications, including Laser Focus World. He retired from Laser Focus World in late June 2022.