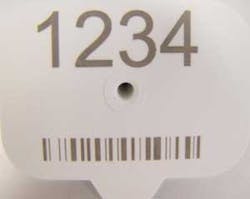
High-contrast and decorative effects can be achieved in color on plastics and metals using Nd:YAG or Nd:YVO4 laser
Riccardo Rusconi and Joshua Gold
C orrect manipulation of the output of certain diode-pumped solid-state (DPSS) Nd:YAG and Nd:YVO4 marking lasers, along with, in certain cases, the engineering of base materials, enables today’s laser user to obtain clear, high-contrast marks, both in black and white and in color on a wide variety of plastics and metals.
Plastics marking
Use of these lasers for plastics marking applications has become widely accepted in all sectors of manufacturing industry. In recent years laser sales, competing mainly against inkjet technology, have gained considerable ground in terms of total system sales, and indications are that market share will continue to expand. The reasons for this success are multiple, including decreased cost of ownership due to elimination of costs associated with ink acquisition, storage, and disposal as well as improved mark permanence and consistency.
Unlike ink deposition techniques and techniques involving the application of colored powders or films, the typical physical effect of a Nd:YAG or Nd:YVO4 laser on plastics manifests itself in a color change linked to thermal degradation (pyrolysis) of the polymer in the presence of oxygen.
The techniques employed, depending on the makeup of the substrate and on the result to be obtained, may vary from the direct application of high average power via high-frequency settings in “charring” applications (thermal degradation of polymer creating a dark mark) to the use of high-peak-power pulses via short-frequency settings to obtain a visible and raised re-solidification of molten polymer in so-called “foaming” applications, to the photo-reduction of titanium oxides in layers immediately underlying the surface in so-called smooth “cold marking” applications (see Figure 1).
Polymers said to be “laserable” (with contrast) are those that absorb the laser wavelength and convert that light into thermal energy. Unfortunately, most “virgin” polymers are more or less transparent to light emitted by common commercial lasers-meaning the laser light passes through without being absorbed. However, because laser marking of plastics has become such a desirable application, plastics formulators and master batch suppliers today offer many chemical formulations that allow the effective reaction between the polymer and laser radiation, without drastic changes in the physical characteristics of the material to be processed. Figure 2 shows how the deposition of pigments and oxides into the polymer increases laser radiation absorption at the different available wavelengths, from infrared to ultraviolet, giving rise to highly “laserable” plastics.
FIGURE 2. Absorption rates with pigment.
In most situations, the result is a mark with good contrast and sharpness. This being said, there is no single additive that can solve all marking needs, be they dark on a light support or vice versa. Also noteworthy is the fact that it is not possible (as of this writing) to create different colors on a single polymer even with pigment additives, and so the resulting marking always remains monochrome, with only shade variations possible.
Notwithstanding this limitation, an interesting application based on obtaining different gray tones between white and black, is used for marking ID cards made primarily of polycarbonate. In this case, the different levels of gray can be obtained by accurately adjusting laser parameters such as pulse energy and duration on a pixel-by-pixel basis. This is a rapidly evolving sector because of the high degree of security and resistance to forgery offered by laser marking.
Color marking on metals
With metals, unlike plastics, a truly decorative effect can be obtained by altering the superficial color of the material subjected to laser radiation (see Figure 3). This effect can be obtained both on anodized surfaces and on untreated surfaces. In the first case, coloring is obtained by thin film interference generated in the oxide layer deposited on the surface laid bare by the removal of the anodization. Controlling laser pulse parameters enables variation in the thicknesses of the new oxide layer and, with these, different colors (see Figure 4). In this way, no more than two or three sharply different colors can be obtained.
null
By contrast, on raw metal surfaces, a broad range of chromatic colors can be obtained, enabling use of Nd:YAG and Nd:YVO4 lasers as a true decorative tool (see Figure 5). In this case, the generation of different colors is linked to the surface diffraction grid obtained by means of several laser passages performed on the same area but with different laser parameters. A laser to be used for this type of work must be able to be tuned to operate at a broad range of frequencies, speeds, power levels, fill spacing settings, focal distances, and so on.
FIGURE 5. Some colors obtainable on raw stainless steel with Nd:YVO4
This new marking technique has elicited interest in decorative applications in jewelry and emblem manufacturing (see Figure 6), where laser color marking, unlike other techniques, is indelible and biocompatible, and can be used to reach recessed spaces and to work three-dimensional surfaces.
null
Conclusion
Contrast and color laser marking with DPSS Nd:YAG and Nd:YVO4 lasers is a viable option in all sectors of industry where a flexible, environmentally clean tool is required to produce clear, readable, and indelible marks, even in areas that otherwise might not be accessible with traditional techniques, while assuring repeatability and reducing the running costs of consumables.
Riccardo Rusconi is at Laservall in Italy, and Joshua Gold ([email protected]) is CO-CEO of Laservall North America, LLC (Pawtucket, RI; www.laservall-usa.com).