Building a business based on customer satisfaction
Bill Fredrick—the president of Laser Mechanisms Inc.—tends to be a rather unassuming person who fits the description of a nice guy, an attribute increasingly hard to find today. From those who know him, this characteristic is typically the first response you get when asking about him.
I’ve known Bill since the mid-1970s, mostly as a technologist, occasionally in a social setting. So when I sat down to interview him in regard to the 25th anniversary of his company—in, of all places, a hotel in Beijing where we both happened to be attending the China International Machine Tool show—he suggested that a brief review of his background might give me a clue as to what makes Laser Mech the success that it is.
To say that he is a pioneer in the industrial laser sector is an understatement. At the University of Michigan, where he studied under Peter Franken, he worked on frequency doubling of light, did some laser spectrum analyzing and laser range-finding, and was among the first to use a helical flashlamp-pumped ruby rod to drill holes in razor blades. We are talking the early 1960s here. Among his fellow associates at the time were other future laser pioneers including Jim Hobart one of the co-founders of Coherent Inc.
On graduating he worked at Trion Instruments, which became Lear Siegler Laser Systems Center, helping that company develop the world’s first ruby, neodymium, and CO2 laser products.
In 1967 he co-founded Photon Sources Inc. in Livonia, Michigan, which after much iteration is now part of GSI Lumonics. At the time he built and commercialized the famed Super Pulse and CW CO2 lasers that were used to drill holes in and scribe the edges of ceramic substrates. Super Pulse was a new way of extracting energy from the CO2 gas, which resulted in long-sustained pulses of more than 100 kilowatts average power, containing the large amounts of energy needed to drill the ceramic with almost no heat effected zone. Photon Sources made thousands of these holed substrates for a number of telecom companies, in the process becoming one of the first CO2 laser job shops.
Eventually Photon Sources, under Bill, developed more powerful, fully industrialized, CW CO2 lasers that were used in various metal and non-metal cutting systems. In conjunction with the growing need for more laser power, he worked with II-VI Corporation as they developed new CO2 materials and coatings. It was during this period that he became an expert on CO2 material processing and that he began to realize that too much emphasis was being put on laser power and not enough on reliable, efficient, easily maintained beam delivery devices.
In 1978, in a move that I learned is typical, Bill chose to direct his energies toward technology and he gave up his president’s position. Much of this decision related to the hard times that the infant industrial lasers industry was experiencing as the United States went through one of its worst inflationary economic situations. Another factor, which he reflects on today, is that he realized his technical education had not really prepared him to be the president of a public company. While he had learned what was needed by trial and error, he felt that there were others who could better run that part of the business, but there were few skilled laser engineers so he took back that job.
Two years later he concluded that what the laser industry needed was a source of quality beam delivery devices, so he left Photon Sources and set up Laser Mechanisms in the basement of a Southfield, Michigan, house. The first products were a spatial filter and circular polarizer module, components for optimizing the CO2 laser’s material working capability, which could be easily added to any manufacturer’s laser. This got the business off to a profitable start as every major laser company purchased these to add to their own product line. These were closely followed by the AccuCutter cutting head, which was designed for stability and ease of cleaning without the need for realignment. It contained the first slot-mounted optics, which allowed the focal point to remain fixed to a machine reference while lens focal lengths and gas jet tips were exchanged as the process might require. Many other radical features for the time such as laminar flow gas jet manifolds, dual gas flow tips for anti-air entrainment, and capacitive auto height sense were available. This device became the bread winner for Laser Mech and remains so today.
Bill’s approach to building Laser Mech as a business was novel in 1980. He did no in-house machining or electrical circuitry, only engineering design and final assembly. In a process he calls virtual manufacturing he outsourced all his machining to a myriad of subcontractors located in the greater Detroit area. These companies, who had invested in the latest machine tool technology, turned out the quality parts that Bill later assembled into beam delivery devices that he supplied to companies like Cincinnati Inc., Raytheon, Coherent, and eventually most of the CO2 system suppliers. To keep employees to a minimum Laser Mech always employed the latest technologies such as computers, fax machines, and cell phones as soon as they became commercially available. This produced a very efficient organization requiring few employees to do a large volume of business.
As customers requested new optical devices for specific application niches, Laser Mech responded. Eventually more engineering talent was added to develop products for paper perforating, heat-treating, and a wide range of other applications.
Under urging from a leading medical device supplier, Laser Mech developed an articulated arm that could ensure the delivery of a quality focused laser beam for surgical applications. These articulated arms became the largest single product in Laser Mech’s catalog, at one time reaching sales of hundreds of units per year. Sold under the OXID brand name, the arm has become the standard of the world in medical circles. The company has expanded the arm technology into industrial applications and today the company is the preeminent global supplier of articulated arms for laser processing. One of the arm designs is now used to retrofit old style flat sheet cutters to improve metal cutting speeds. Sales of all the arm products represent about 25 percent of Laser Mech’s output.
The company has expanded to more than three dozen employees, chosen by Bill to meet one overriding criterion; he hires people who he hopes will be with him for their entire career. This is another attribute Bill has installed in the company’s culture stemming from his formative years at Photon Sources; build a reliable team that shares your passion for customer satisfaction. Laser Mech still does not do any in-house machining of product components, instead relying on that network of valued suppliers who produce the quality parts that Laser Mech designs, assembles, and takes to market.
As the company celebrates its 25th anniversary this month it can reflect on years of profitable operation, a stable workforce, and an ability to respond to industry needs for quality beam delivery products, sold at a fair price and backed by the warranty of a company with an impeccable reputation, built in the image of its founder.
Attaining 25 years in the industrial laser business is a true accomplishment. Companies just don’t do this because they are survivors; they do it because their customers recognize the value that their products and services offer. In all fairness I should mention that Laser Mech has been an ILS advertiser since the October 1986 issue of this magazine, then known as Industrial Laser Review. However, this review is based not on this relationship but on the high regard the company is held in by its customers.
About the Author
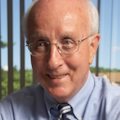
David Belforte
Contributing Editor
David Belforte (1932-2023) was an internationally recognized authority on industrial laser materials processing and had been actively involved in this technology for more than 50 years. His consulting business, Belforte Associates, served clients interested in advanced manufacturing applications. David held degrees in Chemistry and Production Technology from Northeastern University (Boston, MA). As a researcher, he conducted basic studies in material synthesis for high-temperature applications and held increasingly important positions with companies involved with high-technology materials processing. He co-founded a company that introduced several firsts in advanced welding technology and equipment. David's career in lasers started with the commercialization of the first industrial solid-state laser and a compact CO2 laser for sheet-metal cutting. For several years, he led the development of very high power CO2 lasers for welding and surface treating applications. In addition to consulting, David was the Founder and Editor-in-Chief of Industrial Laser Solutions magazine (1986-2022) and contributed to other laser publications, including Laser Focus World. He retired from Laser Focus World in late June 2022.