This issue of ILS includes two features on the subject of additive manufacturing (AM) and, specifically, laser additive manufacturing (LAM). One feature, by Elizabeth Kautzmann, is a philosophical view of what may hinder the acceptance of AM/LAM by manufacturers, while the other feature is Ken Vartanian's in-depth description of 3D printing, the latest "hot" application in desktop manufacturing. ILS has not made a habit of publishing speculative musings by authors, but we challenged industrial laser champion, "Laser Liz," to put her thoughts on paper, which she did in an interesting free flow of thoughts that should produce some interesting reactions. Ken's article is a well-written primer on 3D printing and AM, a subject that seems to be slightly confusing to many in laser materials processing technology.
Here's the problem, however: what's the correct nomenclature? Should the subject be called AM, LAM, SLS, FDM, or SLM? A few years ago, an ASTM committee settled on AM as an umbrella term under which LAM was placed; see ASTM F2792. Overnight, those of us familiar with rapid prototyping and rapid manufacturing were advised that they were now called AM or, in our case, LAM. We asked what happened to laser cladding and precision laser manufacturing and learned that these terms still existed for specific forms of LAM. Satisfied, we accepted the change and heartily endorsed the Laser Institute of America's LAM Workshop, the latest of which was held February in Houston.
For a while, I thought of myself a little like a manufacturer of buggy whips at the advent of cars in that technology had passed me by overnight. And as the editor of an international technology publication, that's a deadly sin. Then, it occurred to me that we had been talking about LAM earlier in our publication's existence, but had called it something else. As a multi-decade promoter since the 1980s of laser cladding and alloying, Industrial Laser Review (the precursor of ILS) published in 1998 an article by Paul Denney and Ray Duhamel, then with UTRC, on producing high-quality shapes without tools by using laser forming (even then we did not know what to call this technology). And a year later, when ILR became ILS, we ran a news item in the April issue about Lockheed Martin using LENS technology (see Vartanian's article 15 years later) for direct manufacturing of complex metal parts. The following year, the January cover feature (by Dwight Morgan of POM) discussed fabricating metal parts from powder. So maybe I was out ahead of the curve on AM, as it was the technology that only now is beginning to get the recognition that Kautzmann says it deserves.
What's caused the rather belated widespread interest in LAM? A plentitude of reasons, some of which Laser Liz explains, but mainly its popularity is due to lean manufacturing and the need to be able to make production quantities of one, quickly and economically. Related to this, many years ago, I consulted on a DOD-sponsored effort that had, as one of its goals, a means to meet the future needs for spare parts when the manufacturers of same had gone out of business. Answer: LAM. The part we studied was a large, worn cast-iron wheel used on rail-mounted ship-side overhead cranes. It seems a rather mundane project, but to us in the laser processing business, it would have been like manna from heaven to get laser cladding up and running. Editor's note: it didn't happen then, but today it likely would.
AM/LAM has been an elusive market for laser processing. Successes have been limited and not glamorous enough to get the attention of manufacturing engineers (see Liz's article). That is changing. Since 2008, ILS has logged in more than 150 editorial pieces on the technology, possibly more than we published in the previous 20 years altogether. Paraphrasing an old TV commercial for wine: No widely used laser application before its time. For LAM, the time is now.
About the Author
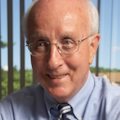
David Belforte
Contributing Editor
David Belforte (1932-2023) was an internationally recognized authority on industrial laser materials processing and had been actively involved in this technology for more than 50 years. His consulting business, Belforte Associates, served clients interested in advanced manufacturing applications. David held degrees in Chemistry and Production Technology from Northeastern University (Boston, MA). As a researcher, he conducted basic studies in material synthesis for high-temperature applications and held increasingly important positions with companies involved with high-technology materials processing. He co-founded a company that introduced several firsts in advanced welding technology and equipment. David's career in lasers started with the commercialization of the first industrial solid-state laser and a compact CO2 laser for sheet-metal cutting. For several years, he led the development of very high power CO2 lasers for welding and surface treating applications. In addition to consulting, David was the Founder and Editor-in-Chief of Industrial Laser Solutions magazine (1986-2022) and contributed to other laser publications, including Laser Focus World. He retired from Laser Focus World in late June 2022.