Advances in manufacturing technology and the trends for faster and more accurate procedures opened the door for new metal welding and cutting applications based on high power lasers. Laser welding and cutting technologies are now being used to replace old processes, often with increased productivity and lower overall cost.
Moreover, the demand for greater precision in high-performance applications, especially in the automotive industries, has increased the use of these lasers as a higher quality, more effective technology. Also, since laser welding and cutting are noncontact processes, metal deformation of the component parts is practically eliminated.
Beam spatial propagation
The beam profile of an intensity distribution is an important parameter that indicates how a laser beam will behave in an application and will dictate the overall system performance in a specific setup. A laser propagating through space has a different width and spatial intensity distribution along its propagation path. This is continuously changing as a function of its laser cavity, divergence, interaction with optical elements, and electronics driver characteristics. Although existing theory accurately predicts laser propagation in a real world involving engineering specification, it is crucial for researchers, system designers, and laser manufacturers to be able to accurately measure laser beam spatial propagation.
Of special interest are the fiber lasers where the good beam quality coupled with high CW power offers deep penetration welding as well as superior metal cutting capabilities. Modulating these CW lasers offers pulsed lasers with high peak and low average power for low heat input applications. The fiber delivery offers flexibility to integrate into conventional weld heads, galvo heads, and robotic and remote welding systems. Whatever beam delivery method is employed, fiber lasers offer unparalleled performance and real-time measurement of beam profile at its focal point, a challenging task.
Laser material processing is especially sensitive to beam characteristics, and end results are strongly dependent on laser beam quality. Laser cutting and ablation characteristics such as depth and edge quality are determined by beam diameter and its surrounding diffraction rings or pedestal. In laser welding, the weld characteristics are dictated by material type, the beam's power density and stability, depth of focus, and so on. Moreover, effects such as thermal lensing will directly influence beam quality and stability.
For further understanding the complexity of high power beam profiling, we will describe the characteristics of two main applications: welding and cutting.
Laser welding
There are many welding methods, but we will concentrate on deposition welding where a filler material is applied to fill the gap between two parts. Deposition welding is also a useful process for surface finishing as well as repairing or modifying existing components. In automated deposition welding, the machine guides the filler material to the area to be welded. After cooling, a metal layer will solidify, and it can be mechanically machined.
FIGURE 1 shows a typical deposition welding head. Measuring the laser beam directly in its mechanical enclosure could be very difficult due to the limited working distance between protective glass and spot location. Moreover, the filler wire guide will protrude into the free space between laser head and workpiece to limit the working distance even further.
Principle of laser welding. The focused laser beam strikes the filling wire, heats the material to the melting point, and fuses it to the surfaces to be welded or filled. Once it has completely welded or filled the workpiece, the process is sustained by moving the laser head along the intended welding contour. The laser beam moves along the part contour, melting the filler material and welding as it goes.
Laser cutting
Cutting is one of the largest applications of lasers in materials processing. Wavelength, power, beam quality, and spot size are some of the parameters that determine the cutting dynamics. As for applications, pulsed lasers are used for fine cutting of thin metals and nonferrous materials, and CW lasers are used for cutting a wide range of thick materials. Ytterbium fiber lasers operating at the 1070 nm wavelength are perfect for laser cutting.
Principle of laser cutting. FIGURE 2 shows the cutting procedure where the focused laser beam incidents the workpiece, heating the material to its melting or even vaporization point. Once penetrating the workpiece, the cutting process is sustained by moving the laser beam across the part contour. Usually, a pressurized gas blows the melted material downward, out of the cut.
Some of the features offered by fiber lasers for most applications are: IR operating wavelength of 950 to 1070 nm, kilowatts of power, good beam quality, wide operating power range, power stability, and small spot size.
To summarize, the laser can handle a variety of material processing tasks. These range from micrometer-precise cutting joints in paper-thin semiconductor chips to quality cuts in 30-mm-thick steel.
Preliminary conclusions
The performance of a high power CW or pulsed fiber-delivered laser systems has to be assessed. At powers of 4000 W and up, measuring the laser parameters is a daunting mission. For best results, measurements should be performed periodically under different working environments, preferably on a manufacturing line.
The main parameters to be measured are total output power and its stability, beam size and its distribution, beam pointing stability, and overall position accuracy. To make things even more difficult, measurements should be performed fast with fast data transfer to the laser controlling computer for on-line corrections.
Measurement procedure
In today's manufacturing procedures, it is not standard to measure any of the above-mentioned parameters. Most of the measuring devices are not constructed for use in an industrial environment, especially when on-line measurement is required. Even for the most basic laser beam parameter--the optical power--measuring devices are on an acceptable standard, but their response time and mounting are inadequate for fast or on-line measurements.
Most of the available measuring devices are also not made for use with high-power lasers in an industrial environment. Those devices do not allow measurements at full power, especially not at the focal point: they are too fragile; the handling is too complicated; and the results are not reproducible. Recent development of a sophisticated nonpolarizing beam sampling device solves most of those obstacles, allowing real-time measurements of beam parameters. In FIGURE 3, a practical measurement using a device to characterize high power beam propagation is presented.
Measurement principle
The focused laser beam incidents the beam sampler's input aperture where, by reflection, the beam is sampled, and its power is greatly reduced. A second reflection further reduces beam power and restores the original beam polarization. Furthermore, the doubled sampled beam reaches the detector, usually a laser beam profiler; in this application, a Knife edge beam profiler made by Duma Optronics is used. For CW high power measurements, this will be the preferred measuring device due to its accuracy in power and multiple profile measurements. Whenever additional power attenuation is required, it can be performed without distortion due to a special attenuation system. Usually, most of the beam passes through the sampling device and strikes a beam dump. The sampling ratio is about 0.1% of the main beam power.
Results
Typical results for 4000 W measurements are presented in FIGURE 4, where a typical measurement of 3921 W, two typical beam profiles in perpendicular directions of 559 and 579 µm, can be seen. The laser power and profile were measured from about 400 W to about 4000 W. There are several noticeable interesting things as a direct result of measurement:
- Real-time profile and power measurements at a rate of 5× per second.
- Profiles and position were very stable during the power-up procedure
- There is a significant pedestal around the main lobe with about 50% percent of total power
Conclusion
A practical real-time method of high power laser measurement is demonstrated. Measurements were performed at the laser's focal point where it matters the most. Further development of innovative beam sampling can lead to real-time accurate measurements of 50 or even 100 kW of laser power. Various measuring beam profilers can be adapted to measurements needs such as power, CW or pulsed lasers, and wavelength.
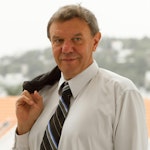
Oren Aharon
Oren Aharon is the CTO of Duma Optronics. He has several decades of experience in the electro-optical field, including start-up initiations based on his patents. He founded Duma Optronics 25 years ago to offer advanced enabling technologies to industry. He owns 30 patents and graduated from Technion with a BSc in nuclear engineering and an MSc in industrial engineering. He has written numerous articles and served as a technical assistant to the Israeli Minister of Energy.