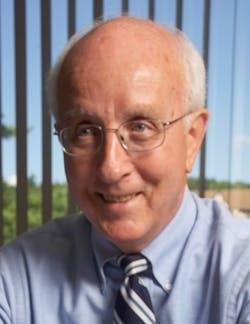
I've been thinking about the time I introduced CO2 laser cutting of sheet metal to US readers of the Journal of the Fabricator in two 1974 issues (May/June and July/August), followed immediately by a talk at an FMA-sponsored conference in Milwaukee (September 1974). In each, I started off by saying that "metal fabricators are usually surprised when lasers are suggested as an alternate method of laser cutting." As a closing, I boldly stated, "lasers after all these years (circa 1974) have become an acceptable metal working tool." My claim was based on early sales made in Europe, where the first 450W CO2-powered, stand-alone units sold by Messer were installed in Germany and in the UK by Plascut (Rotherham, South Yorkshire, England).
Ah, the arrogance—or should I say naiveté—of youth, as it would be four more years before the first combination laser/turret punch from Strippit (now LVD Strippit) was introduced at the 1978 IMTS event in Chicago, and several years more before quantities were sold worldwide. In 1980, the number was less than 100 units per year—by 2015, over 102,000 units had been installed.
As I grew more market-savvy, I realized that even great ideas like non-contact, exothermic cutting with light energy (a technical and economic achievement), which I had been touting, would only become accepted worldwide when the market itself was ready—that is, when a combination of buying influences coalesce to present irrefutable evidence for capital investment. And, I might add, with a little help from some 'champions' among users.
The above reminiscences were triggered by Jason Hillenbrand's retrospective on high-power lasers for metal cutting (see page 13), in which he states that high-power fiber lasers have found their place in the fabricating industry because they are as easy to operate as lower-power units and any additional capital investment can be offset by significantly higher production and lower operating costs than CO2 machines in that power range—the irrefutable evidence I mentioned.
Jay Finn (LaserCoil Technologies) shows new solutions for laser blanking from coil stock, offering ways that laser cutting can become a cost-effective solution for a company's blanking needs (see page 16). Some job shops, looking to add services offered, are moving into sheet metal welding using their laser cutters as welders, which Philipp Rettenmeier (TRUMPF) says is cost-effective (see page 8).
This issue could easily have been dubbed "the marking special" since we present three perspectives on laser marking difficult materials by a variety of processing options. Tony Hoult at IPG Photonics has developed techniques for marking copper, uncoated glass, and other surface structures (see page 19). David Stadler and Joerg Wertli (Optotune) describe a variable z-axis device that is a first step towards a full 3D marking solution that does not require an f-theta lens (see page 22). And Geoff Shannon (Amada Miyachi America) and Gary Firment (Laser-Micro LLC) make the point that a universal marking solution for every part and mark does not exist (see page 24). For example, fiber laser markers can be used on 300 series stainless steel, but as the surface finish increases in difficulty and cycle times, ultrafast lasers in the UV may be the solution.
And finally, Justin Conroy and Rajiv Pandey (Synrad) provide an update on an early CO2 laser application—label cutting (see page 28). They demonstrate its capability in selective converting applications, where the flexibility to cut multiple easily changeable shapes on the fly is needed.
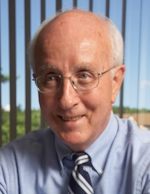
David Belforte | Contributing Editor
David Belforte (1932-2023) was an internationally recognized authority on industrial laser materials processing and had been actively involved in this technology for more than 50 years. His consulting business, Belforte Associates, served clients interested in advanced manufacturing applications. David held degrees in Chemistry and Production Technology from Northeastern University (Boston, MA). As a researcher, he conducted basic studies in material synthesis for high-temperature applications and held increasingly important positions with companies involved with high-technology materials processing. He co-founded a company that introduced several firsts in advanced welding technology and equipment. David's career in lasers started with the commercialization of the first industrial solid-state laser and a compact CO2 laser for sheet-metal cutting. For several years, he led the development of very high power CO2 lasers for welding and surface treating applications. In addition to consulting, David was the Founder and Editor-in-Chief of Industrial Laser Solutions magazine (1986-2022) and contributed to other laser publications, including Laser Focus World. He retired from Laser Focus World in late June 2022.