EOS, IMDS to make medical devices with laser sintering
Novi, MI -EOS Electro Optical Systems (EOS) and medical device maker Innovative Medical Device Solutions (IMDS) are partnering to make new products using laser additive manufacturing technology. IMDS recently installed an EOSINT M 280 direct metal laser-sintering system, and the two companies say they are investigating other partnerships together in response to major medical product developers.
“Until now, using AM for medical devices was considered a high-technology novelty done on a few implants, but mainly used to make quick metal prototypes,” stated Dan Justin, chief technology officer for IMDS. "However, recent advances -- such as increased materials choices, enhanced manufacturing precision, and faster build speeds -- have made medical product developers worldwide more willing to co-invest in developing implants made by laser-sintering systems."
"Instead of being constrained by traditional technology, engineers and medical professionals are now free to explore a world of new designs—perhaps with varied porosity built in, or features nested inside," added Andrew Snow, regional sales director for EOS of North America.
As an example, titanium implants are traditionally manufactured by subtractive machining (material is removed to create shapes and features), and a porous coating is added. Using laser sintering, implants in development are being created in 20 μm layers at a time, resulting in functionally gradient single pieces that transition from a precisely shaped porous structure to a less porous, more solid load-bearing structure -- a design that offers significant performance benefits, and is not capable of being manufactured with traditional processes. Other devices in development include patient-specific surgical guides for placement of pins, saws, and drills.
"This partnership marks the most comprehensive resource alignment between contract medical device development and metal additive manufacturing expertise available to our industry," Justin noted. Longer-term the two firms plan to offer design-to-manufacture services for customized orthopedic implants, e.g. ultrathin bone-conserving joint-bearing implants (hip, knee, shoulder) digitally designed from patient CT scans, built from regulatory-approved implant materials such as stainless steel, cobalt-chrome, and titanium alloys.
EOS claims 1100 systems are installed globally -- about a third of which are its direct metal laser sintering (DMLS) technology -- being used in applications including patient-specific plastic drill guides for surgery, metal tooling inserts, and dental copings.
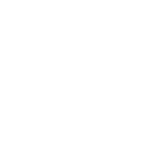
James Montgomery | Associate Editor
James manages editorial production for news (online and print) and newsletters, as well as the magazines' new product sections. Jim has 13 years’ experience in producing Web sites and e-mail newsletters in various technology markets for CNet, ZDNet, Digital City Boston/AOL, and KM World.