Joining Technologies offering internal diameter laser cladding
East Granby, CT - Joining Technologies has expanded its laser additive manufacturing capabilities to include internal diameter (ID) cladding, with the addition of a specialized ID cladding station through partnership with Fraunhofer ILT, Pallas Oberflaechentechnik, and Laserline.
The laser cladding technique can be used with a wide range of materials, including nickel-, cobalt- or iron-based alloys, and carbide-matrix compounds. The new cladding head, mounted to a CNC handling system, can process internal diameters as small as 2.75 in. with a maximum insertion depth of 500 mm. Double-sided access enables ID cladding for parts as long as 1000 mm. The company can perform robotic and Cartesian laser additive processes for components ranging up to 72 in. diameter, 40 ft in length, and 6 tons in weight.
Laser cladding has gained wide acceptance as a cost-effective way to add wear or corrosion-resistant coatings, or to repair worn-out or mis-machined parts. Laser cladding typically has been limited to easy-to-reach external part features.
"The technique is ideal for adding service life to oil and gas equipment, pumps, sleeves and extruder components," stated Tim Biermann, director of the Joining Technologies Research Center (JTRC). "We expect other industries will come to us seeking the ID cladding process for their applications."
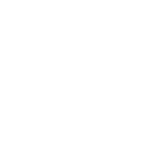
James Montgomery | Associate Editor
James manages editorial production for news (online and print) and newsletters, as well as the magazines' new product sections. Jim has 13 years’ experience in producing Web sites and e-mail newsletters in various technology markets for CNet, ZDNet, Digital City Boston/AOL, and KM World.