Laser coating process improves protection for brake discs
Brake discs, more than other auto parts, are subject to repeated mechanical loads. As a result of this continual abrasion, they produce fine particulate matter, which pose a substantial environmental burden. Now, a new coating process developed by the Fraunhofer Institute for Laser Technology (Fraunhofer ILT) and RWTH Aachen University (both in Aachen, Germany) can significantly reduce this impact. By using extreme high-speed laser material deposition (EHLA), it has proved possible effectively protect the discs against wear and corrosion in a procedure that is both fast and economical.
Traditional brake discs are made of gray cast iron containing lamellar graphite phases, a material with good thermal conductivity and high thermal capacity, at a relatively low price. The downside is a strong propensity to corrode coupled with high material wear during service, which generates substantial emissions of fine particulate matter. To date, it has proved difficult to provide adequate protection for brake discs by means of conventional coating processes such as electroplating or thermal spraying. Their problem is that they do not produce a metallurgical bond between the cast iron and the protective coating; further they are expensive and use a lot of materials. The EHLA process, however, avoids these drawbacks.
"The EHLA process is ideal for coating brake discs," explains Thomas Schopphoven, research fellow and team leader of Productivity and System Technology within the Laser Material Deposition group at Fraunhofer ILT. "Conventionally, it’s difficult to coat brake discs, because they have to withstand high loads, and there are also economic and environmental considerations. But with EHLA, it's now possible to apply coatings that form a metallurgical bond with the base material of the disc and therefore adhere very strongly. Unlike conventional coatings, these do not flake and chip."
As opposed to conventional coatings that can show pores and cracks, the EHLA process coating remains intact, providing longer and more effective protection for the component. This increases service life and prevents early failure as a result of damage to the surface of the brake disc. Moreover, the process is suitable for a wide range of materials. Therefore, it is possible to select an environmentally friendly coating for each specific application.
EHLA does have a number of decisive advantages, for example with EHLA the powder particles of the coating material are melted directly in the laser beam with the melt pool fed by liquid drops of material such that the coating process is faster, rising to as much as 500 meters per minute.
This also substantially reduces the heat affected zone from the millimeter to micrometer range, enabling the use of new material combinations such as coatings for aluminum or—as with the brake discs—cast-iron alloys. So, it is now possible to provide brake discs made of gray cast iron with an effective coating that is firmly bonded with the base material.Compared to laser metal deposition the EHLA process produces very thin layers of between 25 and 250 µm, resulting in a coating both purer and smoother, with roughness reduced to around one-tenth of its previous value.
Moreover, the EHLA process is extremely resource-efficient and more economic, using as much as 90% of the fed powder material. Initial investigations have demonstrated that the EHLA process is capable of reliably producing coatings—with different material combinations—for conventional brake discs made of gray cast iron. A system that is ready for use in mass production, including a modified grinding process for finishing the components, is currently under construction at the Aachen-based company HPL Technologies.
Juries have awarded three prizes for the method: the Joseph von Fraunhofer Prize in 2017, the Berthold Leibinger Innovationspreis in 2018, and, in the same year, second place in the Stahl-Innovationspreis in the Steel in Research and Development category as an environmentally friendly laser-based alternative to chrome (VI) coatings.
For more information, please visit ilt.fraunhofer.de.
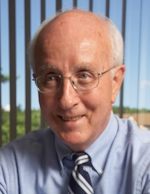
David Belforte | Contributing Editor
David Belforte (1932-2023) was an internationally recognized authority on industrial laser materials processing and had been actively involved in this technology for more than 50 years. His consulting business, Belforte Associates, served clients interested in advanced manufacturing applications. David held degrees in Chemistry and Production Technology from Northeastern University (Boston, MA). As a researcher, he conducted basic studies in material synthesis for high-temperature applications and held increasingly important positions with companies involved with high-technology materials processing. He co-founded a company that introduced several firsts in advanced welding technology and equipment. David's career in lasers started with the commercialization of the first industrial solid-state laser and a compact CO2 laser for sheet-metal cutting. For several years, he led the development of very high power CO2 lasers for welding and surface treating applications. In addition to consulting, David was the Founder and Editor-in-Chief of Industrial Laser Solutions magazine (1986-2022) and contributed to other laser publications, including Laser Focus World. He retired from Laser Focus World in late June 2022.