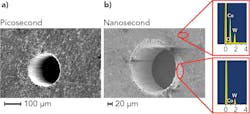
XINCAI WANG, YIN CHI WAN, and HONGYU ZHENG
Tungsten carbide (WC) is well known as a difficult-to-machine material, but is a widely used tool material in industry due to its unique properties such as high hardness, excellent wear resistance, chemical inertness, and dimensional stability. Due to the material’s toughness and hardness, conventional mechanical machining methods such as electrical discharge machining (EDM) and grinding may encounter problems such as tool wear, easy breakage of the tool, and time-consuming repairs. When EDM is used to machine WC, there are several machining issues, including a heat-affected layer produced on machined surfaces and a discharge-induced rough surface. As a result, a post-polishing process is required, which makes the whole fabrication process very slow and increases the production cost. Also, for the EDM process, a shaped electrode needs to be fabricated, which usually wears and has to be remade or replaced to ensure required part accuracy.
An alternative cost-effective and high-efficiency machining method is needed. Laser micromachining is one promising candidate due to its unique properties such as noncontact processing, no mechanical cutting forces, and no process tool wear. However, use of conventional lasers, such as the nanosecond pulsed laser, to machine tungsten carbide has been found to cause thermal effects and residual material redeposition issues.
Recently, researchers at the Singapore Institute of Manufacturing Technology (SIMTech), which is part of A*STAR, developed an efficient picosecond pulsed-laser WC micromachining process that is able to drill high-quality microholes, engrave various features, and produce micro/nanosurface structures on a WC surface.1 Compared with conventional EDM techniques, the picosecond laser WC micromachining process is quite efficient in terms of machining time and flexibility.
High-quality picosecond laser micromachining
With its unique properties such as ultrashort pulse duration and high peak-power intensity, the picosecond pulsed laser produces results much different from those of conventional lasers, creating new opportunities for processing of hard-to-machine materials such as WC. The major advantage of ultrashort laser pulses is their ability to generate high peak power and deliver energy into a material rapidly, before thermal diffusion occurs. During ultrashort pulsed laser processing, material is removed mainly by vaporization. In addition, the laser-irradiation-induced heat-affected zone (HAZ) and molten material are significantly reduced due to the ultrashort pulse duration.
Cemented WC, a composite material system, consists of two main compositions: WC grains and cobalt (Co) binder. As shown in TABLE 1, WC and Co have quite different thermal properties, especially in terms of their melting and boiling temperatures. As a result, some issues will occur during laser machining of cemented WC, such as increased HAZ, rough surface finish, and debris redeposition.These issues can be minimized by using an ultrashort picosecond laser with optimum laser processing parameters. FIGURE 1 compares holes drilled via trepanning with a picosecond laser and a nanosecond laser. The WC substrate is 0.2 mm thick. It is obvious that the picosecond laser-drilled hole has a higher quality than the nanosecond laser-drilled hole. The hole edge is very clean, with almost no HAZ and no debris redeposition, whereas for the hole drilled with the nanosecond laser, a HAZ of about 20 µm is the result. From energy-dispersive x-ray (EDX) analysis, as shown in FIGURE 1b, it can be seen that the Co binder in the HAZ has been evaporated in comparison with the original surface.
The effect of pulse duration on the drilling quality can be explained in terms of the thermal diffusion length, which is a very important parameter in describing laser-induced thermal phenomena and depends on laser pulse duration, the material thermal conductivity, the mass density of the investigated material, and the heat capacity, as described in Equation 1:
where τp is pulse duration, k is thermal conductivity, ρ is mass density, and c is heat capacity.
TABLE 2 shows the calculated thermal diffusion length in WC and Co for different nanosecond and picosecond pulse durations. It can be seen that for ultrashort pulses such as a 10 ps pulse (which is comparable to the thermalization time of about 1 ps), the energy transfer occurs only in a superficial layer of tens of nanometers in scale under nonequilibrium conditions—a much thinner layer than for the nanosecond pulses. During the laser-material interaction, hot electrons are generated, whereas lattice atoms still have undisturbed energies (cold lattice). Material removal occurs through nonthermal mechanisms such as Coulomb explosion. So, as shown in FIGURE 1, the HAZ is much less for the picosecond pulsed laser than for the nanosecond pulsed laser.The effects of various laser parameters such as focus position, repetition rate, hatching pattern, and scanning speed on machining quality in terms of HAZ, debris redeposition, hole circularity, hole taper, surface finish, and cleanness were investigated. The optimum focus position surface, in terms of hole taper, edge, and surface cleanness, was found to be at 0.1 mm below the sample. It was also found that a lower repetition rate helped to reduce the HAZ and debris and produce a circular hole exit. In addition, a multiple circular hatching pattern was needed to drill through thick substrates with hole diameter below 100 µm.
Microdrilling and engraving
It was demonstrated that a picosecond laser is able to drill through WC substrates with different thicknesses up to 0.5 mm thick and a hole size range of 50 to 250 µm. It was noticed that there was a certain amount of taper of less than 6° for the drilled holes. The drilled hole aspect ratio can reach up to 10 and the drilling speed is 2 to 5 s per hole, depending on the sample thickness and hole size. FIGURE 2 shows a picosecond laser-drilled hole array under identified optimum laser conditions with hole diameter of 100 µm. The WC substrates are 0.2 mm thick. It can be seen that the hole edge is very clean with no debris redeposition. The HAZ is minimized.Surface texturing and patterning
As shown in FIGURE 4, a consistent two-dimensional dimple array was produced on a WC-based drill bit with a dimple diameter of 50 µm and depth of 25 µm. The produced dimple array serves as a lubricant reservoir and a trap for wear particles, and is able to reduce the friction coefficient as well as decrease the cutting temperature and the cutting force so as to improve the performance and lifetime of the cutting and drilling tools. In addition, a riblet-array grooving surface structure can be fabricated on WC substrates with a period of 30 µm, a groove width of 25 µm, a depth of 30 µm, and an aspect ratio of 1.2.REFERENCES
1. X. C. Wang and H. Y. Zheng, “Picosecond Laser Microdrilling, Engraving, and Surface Texturing of Tungsten Carbide,” Proc. ICALEO, M804 (2017).
2. P. Crook, Metals Handbook, 2, 1404 (1990).
XINCAI WANG ([email protected]), YIN CHI WAN, and HONGYU ZHENG are all with the Singapore Institute of Manufacturing Technology (SIMTech), A*STAR, Singapore; www.a-star.edu.sg/simtech.