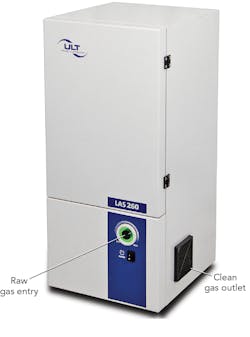
STEFAN JAKSCHIK and STEFFEN BLEI
Advanced laser processes find increased utilization in production processes. This fosters an in-depth understanding of laser fumes, which are a major factor in product quality, machine life, and environmental/safety and health considerations. Ultrashort-pulse (USP) laser processes are focused on non-melting preparations from which exciting new applications arise. Starting from hard-glass manufacturing, to thin-film photovoltaic patterning to lithium ion battery electrode structuring, virtually every advanced technology relies on USP laser processes.1-6
Experiment
This study was performed on a femtosecond laser with a wavelength of 1064 nm.3 Correlations between type of ablated material, particle size distribution, and particle concentration were investigated—specifically, the difference in particle size between steel and plastic was evaluated.
The aerosol resulting from laser material processing was captured close to the source and suctioned towards a filter system. Particle size distribution was determined continuously using an Engine Exhaust Particle Size (EEPS) spectrometer, which measures particle sizes in the 5.6–560 nm range. For this purpose, a sample was analyzed by the instrument. Particles within the sample are positively charged and move within an electric field towards electrometers, where their charge is transferred—the charge is a measure of particle-surface-area. According to their electrical mobility, particles reach different electrometers. Based on current flow, particle size distributions are calculated. In addition, samples were taken from the filter and investigated by secondary electron microscopy (SEM) for analyzing particle shape.
The raw gas was filtered using the LAS 260 filtration system (FIGURE 1), a storage filter with F9 pleat pre-filtration. This pre-filter consists of high surface area with a well-defined cross flow to ensure long filter life. A secondary particle filter with the HEPA-class H14 ensured cleaning capability to 0.005% of total particle count. Further down the gas stream, activated carbon was located to remove eventual reminders of hazardous gases from the laser process.
The performance of the LAS 260 filter system was also determined. For this, the laser was kept in stationary conditions and the particle concentrations in raw gas and purified gas were measured using the EEPS method.
Results and discussion
FIGURE 2 illustrates the particle shapes, as seen in SEM investigations. As expected, the majority of these particles are not melted, though a small amount of the metal debris proved to be hemispherical, which is a sign of sufficient thermal energy to melt this material. In any case, the size of these particles is very small, in the range of d = 100–200 nm.In contrast to the metal process, the plastic debris seemed to be initially smaller, though it formed small agglomerated plates on the filter. The particle shape is mostly cubic. Forming plates can be caused by thermal energy during the agglomeration phase on the filter.
Based on these findings, filter technology should be revised—starting from extraction, the high kinetic energy of these particles has to be taken into account. Small particles are faster due to kinetic impact. The basic rule of extracting the fumes close to the source needs to be extended to another extraction point further up for capturing the small particles in the nanometer range as well.As the size of these particles is mainly in the nanometer range, they can enter the lung-blood barrier, causing high risks on health. Therefore, a standard filter technique is in many cases not suitable for air cleaning. FIGURE 3 depicts the basic principle of particle filtration as used in the LAS 260 extraction system. As demonstrated, most the particles are kept in the F9 filter, ensuring low maintenance cost for the operator.
FIGURE 4 depicts the measurement results of EEPS during the plastic process. The statistic maximum of plastic particles was at d=90 nm with a concentration of 3.4 105 particles per cubic centimeter. This value is well above acceptable concentrations for high product quality and operator health. By employing the filter sandwich of the LAS 260 system, the clean gas was on the same level as the background signal of the lab with dN <<102 #/cm3. Therefore, a high-quality operation in terms of laser fumes is possible.Summary
USP laser processes, especially in the femtosecond range, have been investigated in terms of particle distribution during the operation. Particle size is found to be in the range of d = 50 nm -200 nm in significantly high concentrations of up to 106/cm3. By using the LAS 260 with pleat filtration and HEPA post-filtration, a fractional deposition in the filter of >>99% was demonstrated. For non-cancerous and mutagenic materials, the filtered air can be recirculated in the working environment for saving energy cost.
ACKNOWLEDGEMENT
The authors like to thank the Fraunhofer Institute for Material and Beam Technology (Fraunhofer IWS; Dresden, Germany) for supplying the laser time and the German Ministry of Education and Science for founding part of this work in the MWT+- project.
REFERENCES
1. K. H. Leitz, B. Redlingshöfer, Y. Reg, A. Otto, and M. Schmidt, Phys. Procedia, 12, 230–238 (2011).
2. J. Hänel et al., “Ultrakurzpuls-Laserbearbeitung von Silizium-Mikrosystemen,” MikroSystemTechnik (2011).
3. J. Kaspar, A. Luft, S. Nolte, M. Will, and E. Beyer, J. Laser Appl., 18, 85 (2006); http://dx.doi.org/10.2351/1.2164480.
4. P. Engelhart et al., Prog. Photovoltaics Res. Appl., 15, 6, 521–527 (2007).
5. S. Weiler, D. Sutter, and C. Koerber, Laser Tech. J., 5, 5, 43–46 (2008).
6. “Holtkamp: Mikrostrukturieren mit Zukunft,” Laser Tech. J., 2, 37–40 (2011).
Dr. STEFAN JAKSCHIK ([email protected]) is with ULT AG, Löbau, Germany, and STEFFEN BLEI is with ILK Dresden, Dresden, Germany.