The next level of additive manufacturing
Making a standard machine part from metal powder using a laser system still looks a bit futuristic. Materials, processing time, and costs look a bit futuristic, too, and prohibit a broader introduction of additive manufacturing to regular job shops—but this may change soon.
A collaboration of six Fraunhofer institutes is developing a set of solutions to lift additive manufacturing to the next level. Within their Fraunhofer lighthouse project “futureAM – Next Generation Additive Manufacturing,” they plan to accelerate additive manufacturing with metal powder by at least a factor of 10. They created a concept to overcome build volume limitations towards a freely scalable concept. They have new materials in mind and they want to trace the whole process in a virtual lab with digital shadows. In summer 2020, the project will conclude and it looks as if all targets have been met or even exceeded.
Developing new materials using AI
There are at least two basic principles that the consortium follows to reach such ambitious goals. First, they have an eye on the whole process chain. From design over manufacturing and postprocessing, everything is related and has to be seen in a holistic way. This becomes particularly clear when developing a digital model, as will be discussed later.
The other principle is to develop new ideas for each step of the process chain. One point to begin with is the material for additive manufacturing or metal-based 3D printing. Qualifying such a material for production is expensive; the costs of tests and measurements add up to high six-digit numbers if a new material is introduced into a serial manufacturing process. Furthermore, current applications such as turbine blade repair1 often have extreme requirements for thermal and mechanical properties of the materials, which make the selection process even more challenging.
Scientists at the Fraunhofer Institute for Material and Beam Technology (Fraunhofer IWS; Dresden, Germany) are responsible for the materials part in the project. They have collected decades of experience and, for instance, developed new nickel alloys for additive manufacturing. Such materials are difficult to weld and to process with conventional methods. Finding the right parameters for additive manufacturing processes requires complex tests of various parameters such as temperature, powders, or feed rate.
Such tests are tedious and deliver a lot of data from various sensors. The experts from Fraunhofer IWS introduced a system with artificial intelligence (AI) to exploit the big data effectively. Special analysis algorithms link the sensor data with the institute’s powder database and evaluate further process parameters. Gradually, the machines learn to make their own decisions. For example, they can determine whether a slight rise in temperature in the welding process can be tolerated or whether they have to take immediate countermeasures before the entire component ends up as waste.
In addition to using AI for faster process development, the experts at Fraunhofer IWS have taken on further challenges such as multimaterial constructions. For example, different areas of a turbine part are exposed to different temperatures. Thus, expensive, highly resistive materials can be used where needed, but the rest of the part can be made from other powders. Using laser material deposition, different powders can be fed into the process zone simultaneously or successively with precisely adjustable feed rates. Such transitions have been tested for several different materials such as Inconel 718 to Merl 72 (FIGURE 1). Current research focuses on transitions from Titanium to Aluminum. The experts also investigate how the procedure works for three or four components.
Making additive manufacturing 10X faster
Another core problem for the application of additive manufacturing in industrial manufacturing is productivity. So, how can additive manufacturing become faster? Parallel production of several parts in one machine is a common answer, but there are other and more sophisticated ideas.
A team from the Fraunhofer Institute for Laser Technology (Fraunhofer ILT) and RWTH Aachen University (both in Aachen, Germany) has developed a method in which the metal powder for additive manufacturing is used in the form of a powder jet.2 The trick in this patented process is to melt the powder particles within the jet before they reach the surface of the workpiece. As the melt pool on the workpiece is fed by liquid drops of material rather than solid particles of powder, the coating process can be much faster, rising from the 0.5 to 2 m per minute with conventional laser material deposition to as much as 500 m per minute.
This extreme high-speed laser material deposition process known as EHLA (in German, this means “Extremes Hochgeschwindigkeits –Laserauftragschweißen”) won several high-ranking industry awards in 2017 and 2018. In 2019, the method was used in serial production of hydraulic cylinders of up to 10 m length and up to 500 mm diameter already. The costs were comparable to those of thermal spraying, as confirmed by users.
The original EHLA process was designed for rapid coating of rotational parts. At Fraunhofer ILT, the idea has been transferred to a new machine where the workpiece is moved by a tripod while the laser and the powder nozzle remain at fixed positions. This way, the workpiece can be moved with accelerations up to 200 m/min with up to 5g while the powder jet remains undisturbed. The adapted process allows to build 3D structures on almost every surface. Single layers can be built as thin as 30 µm and lateral features with a resolution of 100 µm.
The material deposition rate has been tested up to 3 kg/min (50 g/sec). With higher laser power, even higher rates might be possible. Compared to laser metal deposition, this new procedure is more precise, depositing less heat in the material and allowing the use of hard-to-weld materials.
Overcoming spatial limitations
The new 3D procedure stands between two established methods: laser metal deposition (LMD) and laser powder-bed fusion (LPBF). LMD is the method of choice to build a metal coating onto existing surfaces.3 For this purpose, a laser beam melts the surface, a metal powder is fed into the mold, and a new material layer develops. This is well known for the repair of hard metal tools or turbine blades. LPBF (also known as laser sintering, laser metal fusion, or simply 3D metal printing) is used to build entirely new workpieces according to CAD data by melting a metal powder with a laser beam. This is repeated layer by layer until the job is completed.During LPBF, a laser beam follows a defined trace to create a metal contour in the powder bed (FIGURE 2). Obviously, this process can be accelerated by using several laser beams and building up several parts in one powder bed. The typical limitation is the build volume, which is restricted by the stability of the shielding gas flow. The shielding gas is applied to remove process by-products such as spatter or metal condensate.
The experts at Fraunhofer ILT have built a new laser processing head to overcome this limitation. This system uses multibeam optics with five laser beams and five x-y scanners, allowing processing with five laser spots at once. Furthermore, the compact head uses two nozzles for inert gas. Usually, such nozzles limit the workspace to less than 600 or 700 mm. In larger areas, turbulences can occur. The new processing head is used in a prototype machine with a build volume of 1000 × 800 × 500 mm (FIGURE 3). Therein, the head controls a space of 200 mm width and can be applied in working chambers of any size. The build volume is only limited by the length of the linear axes. Already in the prototype, productivity can be increased by a factor of 10 compared to conventional LPBF machines.In addition to new hardware, a new software module was developed. It allows control of the energy input into the powder: the process parameters can be set individually for each individual melting track in order to increase both component quality and build speed. This targeted parameter selection can, for example, prevent overheating in the component. This way, the number of required support structures in overhangs can be significantly reduced or even eliminated completely. It allows speeding up the process in massive areas of the component.
Listen to the process
In a machine shop, it is easy to tell from the sound of a lathe whether it is running smoothly. Surprisingly, a similar effect occurs in 3D printing as well. For example, the vibration pattern of the workpiece changes when support structures tear off. The researchers at Fraunhofer ILT have installed ultrasonic sensors within the working chamber to investigate the sound of such events.
The actual research into ultrasound measurement will go a step further in the future: a pulsed laser will induce structure-borne noise in the component, which in turn will be detected by a laser vibrometer. This could help in finding tiny pores on the workpiece while they are evolving, allowing an immediate intervention. The in situ measurement process should, for example, make it possible to rework problem areas with another exposure sequence.
Automated postprocessing
One of the major limitations for industrial additive manufacturing processes is the amount of manual postprocessing required, accounting for up to 70% of the total process costs. So, changing the postprocessing from manual to fully automated procedures was a major task in the project. Scientists at the Fraunhofer Institute for Machine Tools and Forming Technology (Fraunhofer IWU; Chemnitz, Germany) led this part.
For all postprocessing steps, they developed various autonomous technology modules and individual processes. For example, an identification module identifies the component and additional sensors help with orientation. The module retrieves the digital information about the component from the CAD file and then starts the cutting process with the help of a robot on the basis of the specified support structures. Finally, two laser line scanners measure each machining process so that the robot can rework the component if necessary.
The future is digital
While every step in the process chain deserves attention, it is the software that links them all together. This includes data acquisition and processing for every part and every step in the process chain. Furthermore, it should allow for distributed manufacturing on different places in one country or around the world.For this purpose, the partners within the FutureAM project have developed a virtual lab (FIGURE 4) that digitally links all areas and all involved partners via a network and a database. It will be made to control the processes and to track distributed manufacturing.
This virtual lab includes digital mapping of the real world for simulation and tracking: Digital shadows enable project participants to model and simulate processes in order to optimize real systems in all steps of manufacturing. According to the ideas of Industry 4.0, this software should allow for substantial progress in manufacturing efficiency of 3D metal printing.
REFERENCES
1. A. Thoss and S. Piegert, “Laser-based methods generate massive lead time reductions,” Industrial Laser Solutions, 34, 3, 28–30 (2019).
2. T. Schopphoven, A. Gasser, and G. Backes, “Extreme high-speed laser material deposition conquers industry,” Industrial Laser Solutions, 34, 1, 27–29 (2019).
3. D. Locke, “Laser metal deposition defined,” Industrial Laser Solutions, 25, 6, 6–9 (2010).
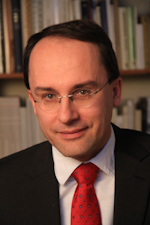
Andreas Thoss | Contributing Editor, Germany
Andreas Thoss is the Managing Director of THOSS Media (Berlin) and has many years of experience in photonics-related research, publishing, marketing, and public relations. He worked with John Wiley & Sons until 2010, when he founded THOSS Media. In 2012, he founded the scientific journal Advanced Optical Technologies. His university research focused on ultrashort and ultra-intense laser pulses, and he holds several patents.
Christian Tenbrock | Group Manager for Laser Powder Bed Fusion, Fraunhofer Institute for Laser Technology
Christian Tenbrock is Group Manager for Laser Powder Bed Fusion at the Fraunhofer Institute for Laser Technology (Fraunhofer ILT; Aachen, Germany).