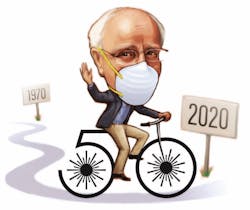
Editor's Note: I am indebted to Derek Kern, president and CEO of Kern Laser Systems (Wadena, MN). In response to my call for examples of how industrial lasers suppliers and users were reacting in the COVID-19 crisis he sent this to Industrial Laser Solutions along with this note: “I noticed your recent articles on COVID-19 have been driving quite a bit of traffic for your audience. I wanted to provide the following, which features 7 small/mid-size companies that have completely shifted their business models and are using their lasers to create PPE masks for hospitals.” I am so impressed with the response to the crisis by these companies. We all owe you a heartfelt thank you. Wear your masks, everyone.—David Belforte, Editor-in-Chief, Industrial Laser Solutions
7 companies using laser technology to combat COVID-19
DEREK KERN
The COVID-19 crisis has placed intense pressure on companies as we strive to maintain (and potentially future-proof) bottom-line revenue amidst possible shutdowns, corporate mandates, and operational changes. As the pandemic is teaching us, unique challenges require unique solutions as well as pivoting where required. At Kern Lasers, we’re always impressed with the work our customers do and appreciate where our efforts help them achieve theirs. Now, more than ever, we’re in awe and proud of the work our customers are conducting to combat the effects of COVID-19 and its far-reaching implications within industries and the economy alike.
Here are some of those stories of impact and versatility.
1. Woodchuck USA
Ben VandenWymelenberg is the founder and CEO of Woodchuck USA, a Minneapolis, MN-based custom wood production company specializing in truly unique gifts. As Minnesota entered the shelter-in-place mandate from Governor Walz’s Stay Home order, Ben entered his company into a new production territory.
Originally, his company shifted half of its production to face shields for medical staff members and personnel, developing a prototype within 24 hours of the decision. As word spread and obvious need grew, Ben and team shifted 100% of its production to that of face shields, cranking out 45,000 a day at first, and ramping up to 105,000 units per day now. Woodchuck is using all eight of their Kern HSE 52 × 100 in. CO2 150 W lasers to cut face shields.
Ben said their team recognized the “extra, extra high demand” for PPE across the U.S. and made the unanimous choice to support the cause. He explained that the face shields are compliant with N95 masks and are produced to John Hopkins’ standards. The face shields essentially elongate the lifespan of N95 masks worn by medical professionals on the frontlines of this crisis.
On the company website, Ben writes, “As an entrepreneur, you get used to the daily intensity of ever-changing situations and opportunities to grow. The opportunity to go against the beaten path, venture out, experience something new, and forge a new road. Over the past few weeks, we have all experienced an exponential amount of change. A change in the global markets, a change in our national procedure and benefits, a change in our state policy, likely a change in our employment, and a change in our homes and family life. Myself and my entire team here at WOODCHUCK USA are standing by and ready to help in whatever way possible.”
Order Face Shields from Woodchuck USA and watch Ben’s Video via LinkedIn
2. Laser Cutting, Inc.
Laser Cutting, Inc. (LCI), based in Milwaukee, WI, is a full-service sign and point-of-purchase display house. For nearly 30 years, LCI has served the industry to design and manufacture signs and displays, while also offering laser cutting and laser engraving services with secondary operations. Now, for perhaps the first time ever, the company has turned its capabilities to that of the growing PPE shortage in a time of global pandemic.
“We are laser cutting fabric masks, polycarbonate face covers, and clear acrylic barriers for retail applications,” said John McMillan, the sales manager at LCI. “We have 10 lasers for short lead times and make protective barriers, face masks, and other custom parts. Our lasers can cut most nonmetal substrates, and we are making essential parts for fighting the Coronavirus.” LCI is using their large-format 4 × 8 Kern Laser tables equipped with CO2 lasers from 100 to 400 W to produce the products.
Inquire About LCI for PPE Needs and connect with John on LinkedIn
3. Faulkner Plastics
Faulkner Plastics, a family-owned and operated plastic distribution and fabrication company in Hialeah, FL, is celebrating its 50th year in business. The company is a source for all types of plastic custom fabrications for retail, wholesale, and export. Though Faulkner has decades of experience, the company hadn’t produced any medical equipment, but the Coronavirus changed all that.
Responding to local fire and rescue first responders in Hialeah facing a shortage of PPE and safety equipment, Faulkner Plastics quickly flipped production to plastic face masks. Joseph McCabe, VP of Faulkner said, “We’re operating 24 hours a day now to make these face masks.”
Mask orders came in rapidly and the initial batches were in the hands of first responders and emergency personnel by March 26th. In addition to the City of Hialeah, Faulkner also collaborated with Lawrence Franchetti, CEO of One Beat Medical in Miramar, FL, a business that distributes medical supplies. After learning about the new equipment Faulkner Plastics is creating, he reached out to the company to help get the equipment in the right hands. He told 7 News Miami, “We are able to work with them to protect our first responders out there.”
Because Faulkner Plastics has been successful using its Kern Lasers in making these face masks during the upheaval of normal business, they’re currently looking at different organizations across South Florida to determine who they can help during this pandemic.
Order Face Masks from Faulkner Plastics and watch News Story via 7 News Miami
4. Versacarry
Versacarry (Bryan, TX) is primarily known for producing premium leather holsters, but is joining the fight to help stop the novel Coronavirus. The plant has switched part of its manufacturing capacity from making firearm accessories to widely needed medical items, such as face shields and masks. Versacarry uses their three 52 × 100 in. 400 W lasers to cut the PPE products.
With weekly output expected at 20,000+ of each product, these will be sent to the front line of this pandemic war and into the hands of hospital personnel, EMT, police officers, firefighters, and others facing the virus on a day to day basis.
Order Face Shields from Versacarry and read this local news article.
5. Mirart
Founded in 1976, Mirart (Pompano Beach, FL) began manufacturing a variety of acrylic mirrored products. Today, the Florida-based team is using their Kern Lasers to create intubation boxes, partitions and sneeze guards, and face shields to help create safer environments for essential workers during COVID-19.
The Intubation Box, ideally used in hospitals, works by sitting over the head and shoulders of a patient as they are intubated by a provider. The box acts as a protective shield between the patient and medical staff, thereby hopefully minimizing the medical staff’s exposure to Coronavirus (COVID-19). Although this is a NON-FDA approved device, it was created by Dr. Hsien Yung Lai with best practices in mind and is currently being used by medical professionals.
Order an Intubation Box from Mirart and view protective barriers.
6. Laser Etch
Tim Pawelk’s laser engraving company, Laser Etch, uses advanced laser technology to engrave on metal, plastic, wood, glass, stone, and more. The technology allows them to custom-etch, 3D-engrave, cut, sandblast, and more on a variety of items, surfaces, and materials, including curved or irregular surfaces such as pens, baseball bats, and rocks.
When the Coronavirus hit, Pawelk got a request to create PPE face shields to help prevent the spread. They have five different Kern Lasers ranging from 48 × 24 in. to 60 × 120 in. and from 50 to 400 W and was easily able to reconfigure the laser settings to create the shields.
“I saw a picture of a design in the news and created my own version,” explained Pawelk. “This version does not contain open cell foam and should be cleanable and not a single use item.”
He’s using 1/8 in. PETG for the frame and .030 in. for the face shield. He says that the laser allows for fast modifications as the design changes. Cost of cutting face shields is close to the die cutting price of the thinner (.015) PETG when production is under 2000 pieces, meaning there are minimal costs to his company, and they are making a great impact to help slow the spread of COVID-19.
Order Face Shields from Laser Etch
7. Shields Windshields
Shields Windshields is a family-run polycarbonate and acrylic manufacturer creating windscreens, windows, shields, and canopies for heavy equipment, racing cars, vintage and classic cars, specialty vehicles, marine, military, and OEMs.
Due to the current health crisis, the company was approached with a design to make intubation boxes. That day, the company president created a prototype and began reaching out to hospitals inquiring about their needs.
The company announced in a statement, “This crisis is affecting and challenging everyone. We want to help our local healthcare providers stay safe and we hope these boxes aid in that. We have begun production on these boxes and will increase production as needed by demand and have shipping worldwide. We plan to continue supporting our community through maintaining employment, hiring during this time, and providing these boxes or other PPE supplies that are needed.”
They use Kern Lasers along with CNC to make and identify blanks. Then, they form the acrylic box and fit the pieces together.
They are encouraging any hospitals or clinics in need of these boxes to please call 1-800-554-7527 for more information or share their information with those in need. They are ready to produce and can ship anywhere.
Order boxes from Shields and read this Local News article here.