Corrosion-resistant black marking of medical devices
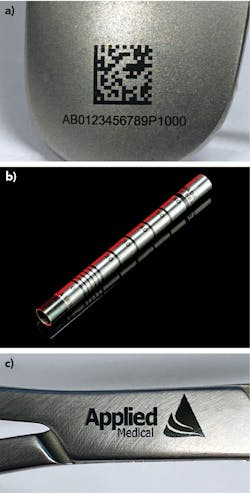
Medical device manufacturers have been marking their parts for branding, serialization, and traceability for decades. In 2015, however, the U.S. FDA mandated that implantable devices bear a specific, permanent mark called Unique Device Identification (UDI) on the device itself. In 2018, UDI was extended to include reusable surgical tools and instruments, like depth scales, that undergo autoclaving and reuse.
Typical customer key criteria state that UDI marks must be:
- High-contrast and dark black in color
- Permanent, corrosion-resistant, and non-fading
- Machine-readable
- Shallow, with minimal surface relief to prevent bacteria accumulation
Ideally, no additional passivation step would be required after the mark is made.
The three most common marks made on these kinds of parts are 2D code for UDI; banding to mark depth scales on cannulas, catheters, and other tubes; and logos or company branding added to some parts for identification purposes and to distinguish between other similar parts (FIGURE 1).
The challenge in marking these parts is that the mark must be high-contrast, corrosion-resistant, free of inclusions or engraving, and able to survive further passivation steps or cleaning processes (e.g., autoclave). Laser marking is the only viable way to achieve marks that meet these requirements. However, not all lasers are equally effective.
Traditional laser black marking
Traditionally, nanosecond infrared (IR) fiber or UV diode-pumped solid-state (DPSS) lasers have been used to create dark, contrasting marks on parts. While these lasers are able to achieve successful marks, the processing window is small, which can lead to concerns over process reliability and consistency.
Because these lasers make marks via a thermal process, resultant mark quality depends on the geometry of the part and the alloy used. This means that a new laser marking recipe must be developed not only for each and every part individually, but also for every mark location on every part. In addition, the heat generated in this thermal process results in the formation of an oxide layer on the surface of the part, which can lead to cracks (FIGURE 2). These cracks can cause the marks to fade or, in the worst case, disappear completely during the next step—the passivation process. Passivation is typically the last manufacturing step after laser marking, as it is used to rebuild the chromium oxide layer that degrades or is removed in previous steps.Furthermore, the fragility of the oxide layers also poses an issue when disinfecting and sterilizing multiple-use parts. A common cleaning technique is autoclaving, which submits the parts to high temperature and pressure.
IR picosecond laser black marking
IR picosecond laser pulse durations are generally 3–4 orders of magnitude shorter than the pulse durations of typical nanosecond marking lasers and have significantly higher peak powers. As such, they interact with the material differently. The marks may look similar to the naked eye, but the method by which the black mark is created is different. The ultrashort pulse durations of the picosecond laser allow energy to be imparted to the material surface with minimal thermal effects. This creates features known as “light traps,” which have antireflective properties, making marks that appear dark black against their surroundings (FIGURE 3). In other words, the picosecond marks do not form a brittle oxide layer and therefore remain corrosion-resistant, even after passivation and repeated cycles of autoclaving and sterilization procedures.The process window for this type of structured mark has also been found to be significantly larger and is not dependent on part shape or alloy. Since it is an athermal process, it better accommodates part tolerances and inconsistencies, which is beneficial in production.
More and more medical device manufacturers are turning to picosecond marking technology to ensure the marking success of their parts. Recent advances in this technology have resulted in improved industrial robustness of the laser engines, increased average power (lowering process time), and lower prices. The slight price advantage afforded to nanosecond fiber or UV DPSS lasers is steadily decreasing, and the technical benefits of picosecond IR lasers are quickly outweighing this particular factor.
Summary
Picosecond IR lasers have entered the market of black marking of stainless-steel medical devices and are the best choice for medical device manufacturers today to comply with rigorous unique device identification regulation. Picosecond IR lasers ensure a reliable mark that is high-contrast, permanent, and corrosion-resistant. The broad process window improves the production reliability over traditional laser options.
About the Author
Mark Boyle, Ph.D.
Product Manager, Amada Weld Tech Inc.
Mark Boyle is Product Manager at Amada Weld Tech Inc. Mark is responsible for technical product management of the company’s product lines, including laser, micro TIG, resistance welding, seam sealing, hot bar, and systems.
Brennan DeCesar
Manager, Advanced Technology at Amada Miyachi America
Brennan DeCesar is Manager, Advanced Technology at Amada Miyachi America (Monrovia, CA).
Dan Sickafoose
Director of Business Development, Amada Weld Tech
Dan Sickafoose is Director of Business Development at Amada Weld Tech (Monrovia, CA).