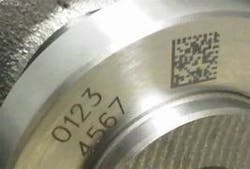
Aluminum is used in a very large sectors of activity, including aeronautics, shipbuilding, electrical/electronics, rail transport, and particularly the automotive industry. In the automotive industry, car manufacturers and equipment suppliers opt for aluminum for manufacturing car chassis, steering columns, power steering components, turbo bodies, engine crankcases, cooler or automatic air conditioning elements, and now in the fast-developing field of new energy vehicles (NEVs), particularly in manufacturing electric battery casings and other electronic components.
Because the use of aluminum is so varied, so are the traceability requirements, as the marking requirements are of a very different nature and require barcode, Data Matrix, alphanumeric, or logo marking. In addition, there are several constraints linked to the nature of the aluminum (anodized, alloy, etc.), but also to the customer’s requirements, particularly in terms of marking contrast or depth. It is not uncommon to be asked for a marking capable of being visible after the application of any coating or of resisting various surface treatments such as shot-peening for example.
Recognizing this, industrial traceability specialist SIC Marking (Pommiers, France) has been committed to providing appropriate marking solutions to meet the challenges associated with the identification of aluminum components. The company’s experience has enabled it to offer a technically superior range of scribing, dot peen, and laser marking machines, as well as a large number of automatic reading solutions for Data Matrix codes. Its laser product range is particularly suitable for marking aluminum components both in series and individually; it consists of lasers that can be integrated with various options:
- A 3D function for marking on complex-shaped parts
- A vision function for fast and reliable barcodes and Data Matrix reading
- A rotary axis for cylindrical parts marking.
SIC Marking’s product range also includes L-BOX, XL-BOX, and XXL-BOX laser stations, which can be integrated into a production line or used as a standalone marking station.
SIC Marking has had the opportunity to take on challenges offered by major automotive equipment manufacturers, including a particularly complex request from a major Japanese player in the automotive sector that wanted a station dedicated to marking Data Matrix codes on power steering components. The solution had to withstand a constraining environment (humidity, dust), fit into a small space, and adapt to different part numbers. Based on many years of experience, SIC Marking was able to offer a compact customized station equipped with a HD laser automatically controlled on 2 axes for fast and high-contrast marking. It is protected by a dust and moisture protection system, making it easy to integrate into a difficult industrial environment.
SIC Marking recently provided a major German equipment manufacturer with the most suitable solution for its requirement to mark a 7 × 7 mm Data Matrix code on air conditioning compressor pistons to facilitate their internal traceability. These codes needed to be marked deep enough to allow proofreading, even after shot peening and tinning and in reduced cycle times. After various marking tests, the chosen solution was a 50 W fiber laser to carry out deep marking in record time.
SIC Marking also offers markings on NEV battery components, turbo bodies, and identification plates for electric motors and engine cylinders.