3D micro assembly with precision laser welding
Welding engineers know that automated joining processes are only as good as the fixturing used to hold and position the part. Recognizing this, Nanosystec (Groß-Umstadt, Germany) designs and builds high-precision assembly and test stations. The company’s VersaWeld system uses accurate motion control and joining techniques for precision laser welding and soldering, with up to six degrees of freedom and long-travel linear motor axes with encoders for position readout. This precision laser welding station complies with complex welding geometries. As an additional option, the laser beam is deviated to any position in a field of 100 × 100 mm by a XY scanner within milliseconds.
Modern fiber laser sources offer up to 500 W continuous-wave power and create a weld seam down to 20 µm wide. In pulsed mode, such lasers provide high peak powers and allow for keyhole welding. Alternatively, lamp-pumped Nd:YAG lasers with pulses in the millisecond regime allow for high flexibility—as low as 100 µm spot diameter can be achieved.
Automated machine vision utilizes the images from the weld optics and external cameras for motion control purposes, such as seam tracking. Device-specific machine vision algorithms reduce the processing time to a minimum.
VersaWeld works as a single station or can be integrated into production lines. Trays for single or multiple devices sets, belts, and feeders present the parts for processing and allow for the exchange with other work stations in the line. In addition, VersaWeld controls robots for device loading.
Quick-release toolings serve for maximum flexibility in order to process different workpieces and reduce setup time when changing from one process to the next.
Nanosystec systems ([email protected]) are used worldwide in optoelectronics, medical applications, the automotive industry, and aerospace.
About the Author
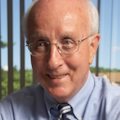
David Belforte
Contributing Editor
David Belforte (1932-2023) was an internationally recognized authority on industrial laser materials processing and had been actively involved in this technology for more than 50 years. His consulting business, Belforte Associates, served clients interested in advanced manufacturing applications. David held degrees in Chemistry and Production Technology from Northeastern University (Boston, MA). As a researcher, he conducted basic studies in material synthesis for high-temperature applications and held increasingly important positions with companies involved with high-technology materials processing. He co-founded a company that introduced several firsts in advanced welding technology and equipment. David's career in lasers started with the commercialization of the first industrial solid-state laser and a compact CO2 laser for sheet-metal cutting. For several years, he led the development of very high power CO2 lasers for welding and surface treating applications. In addition to consulting, David was the Founder and Editor-in-Chief of Industrial Laser Solutions magazine (1986-2022) and contributed to other laser publications, including Laser Focus World. He retired from Laser Focus World in late June 2022.