Laser erosion cutting is a term that isn’t widely used today. I thought only old graybeards like me running high-peak-power, pulsed solid-state lasers used it. Andrew May of ES Precision (Abingdon, Oxford, UK) says the process itself isn’t all that commonly used, either. When I Googled the term, user gKteso GmbH (Bobingen Germany), turned up with a neat definition - laser erosion. A new application for lasers in manufacturing, the correct choice of laser and material is essential for the process. Laser erosion is the removal of thin layers from a workpiece.
May agrees, telling me “It neatly describes the process and distinguishing it from ‘normal’ laser cutting. It’s more accessible than terms involving words like vaporization or sublimation.” Personally, he said, he had never heard of ‘vaporization mode cutting’ until I mentioned I used it in courses I taught in the 1990s.
ES Precision may be the only company offering such a service in the UK, so it’s fairly innovative in that sense. May says affordable higher power/high beam quality fiber lasers now make the process a bit more attractive than when Q-switched yttrium aluminum garnet (YAG) lasers were really the only way to access it for metal cutting (thus yours truly). ES Precision has both technologies, but does find that the pulse duration of fiber lasers is more efficient per watt than vanadate or YAG sources, which tend to have very high sublimative peak powers but very short pulses and lower volumetric removal rates. ES Precision’s latest investments in technology to provide laser processing to UK manufacturing companies uses erosion cutting to fabricate precision components from sheet metal on a scale that traditional laser cutting cannot efficiently achieve.
The laser erosion cutting workstation and a computer microscope measuring system at ES Precision were partly funded by a ‘bounce back’ grant from the Getting Building Fund in recognition of the important innovation that this technique brings to precision manufacturing companies. The laser is a Coherent-Rofin PowerLine F100—a galvo-delivered 100 W fiber laser and the microscope is a turnkey digital system from Keyence.
All metals can be processed with the equipment and other laser technologies at ES’s Abingdon site can process organics such as paper/card, wood, leather, and some plastics. The same laser technology can also produce detailed functional or decorative markings on the cut components.
Erosion cutting uses a deflection head to direct the focused laser beam across the working area. Each pass removes several microns of material and even thousands of passes can be completed in minutes until the pattern is cut cleanly (see Fig. 1). Intricate CAD cog patterns from a customer were simply uploaded to the laser and cut from 0.35 mm brass (see Fig. 2).These prototype designs were produced economically at a batch volume of only five, but volumes of thousands could be also be economic before other mass-production techniques need to be considered. After cutting on the laser, the parts were subjected to a semi-automatic quality assurance (QA) process using the measuring system: first-off units had key dimensions extracted.
Subsequent parts were 100% QA-tested against a pre-set tolerance window of critical dimensions on a simple, one-click inspection that provides a simple pass/fail response.
ES Precision has been receiving enquiries for laser micromachining from companies operating in a diverse range of industries such as medical devices, fuel cell and battery, lab-on-a-chip, and motorsport. Suitable applications are trialed without charge; erosion cutting is particularly well matched to intricate metal cutting of components from a few millimeters to about 20 cm from metal sheets of up to 2 mm thickness.
ES has so far processed many thin metals, including precious (gold, silver, and platinum), specialist (molybdenum, tungsten, tantalum, vanadium, and titanium), and more commonplace engineering materials (stainless and carbon steels, brass, copper, and aluminum).
May summed up, “I chose laser erosion cutting because it neatly describes the process, and of course it is very important that I distinguish it from ‘normal’ laser cutting, so that potential users and readers can be clear about its advantages and drawbacks.”
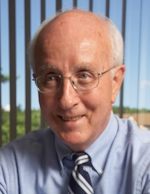
David Belforte | Contributing Editor
David Belforte (1932-2023) was an internationally recognized authority on industrial laser materials processing and had been actively involved in this technology for more than 50 years. His consulting business, Belforte Associates, served clients interested in advanced manufacturing applications. David held degrees in Chemistry and Production Technology from Northeastern University (Boston, MA). As a researcher, he conducted basic studies in material synthesis for high-temperature applications and held increasingly important positions with companies involved with high-technology materials processing. He co-founded a company that introduced several firsts in advanced welding technology and equipment. David's career in lasers started with the commercialization of the first industrial solid-state laser and a compact CO2 laser for sheet-metal cutting. For several years, he led the development of very high power CO2 lasers for welding and surface treating applications. In addition to consulting, David was the Founder and Editor-in-Chief of Industrial Laser Solutions magazine (1986-2022) and contributed to other laser publications, including Laser Focus World. He retired from Laser Focus World in late June 2022.