Ultrahigh-power laser cutting continues growth path
Two methods are currently used to cut sheet metal: plasma cutting and laser cutting. Plasma cutting dates back to the 1950s when it was developed as an alternative to flame cutting. It works by firing a superheated, electrically ionized gas (i.e., plasma) out of a nozzle at high speed toward the workpiece. An electrical arc is then formed within the gas. This electrical arc ionizes some of the gas, creating an electrically conductive channel of plasma in the process. As electricity from the cutter torch travels down this plasma, sufficient heat is generated to melt through the workpiece. The plasma and compressed gas blow the hot molten metal away, resulting in separation of the workpiece.
Laser cutting was first developed in the 1960s as a way to cut holes in diamond dies. This thermal cutting process uses a computer-directed, high-power laser along with oxygen, nitrogen, and compressed air to burn, melt, vaporize, or blow away the material being cut. The laser beam is emitted from the laser source and then transported through a suitable beamline (made by several mirrors or an optical fiber cable) into the laser head containing the lenses that focus the beam onto the surface of the material for cutting and piercing.
There are two types of lasers used in these applications: CO2, which works at a wavelength of 10.6 μm, and solid-state lasers, which operate at around 1 μm (thin-disk and fiber lasers). CO2 lasers are cheaper, but they cannot cut through copper, brass, and aluminum because they do not work on reflective surfaces. In contrast, solid-state lasers (besides a higher energy/wall-plug efficiency and wider variety of materials) have the major benefit of a much higher processing speed/feed rates, due to the higher absorption rate of ~1 µm vs. ~10 µm wavelength in ferrous materials.
Each method offers certain capabilities and benefits that make one more suitable for an application than the other. In general, the main benefit of laser cutting is its noncontact process, using heat to cut through the material, and it’s far more precise; the main benefit of plasma cutting is that it offers versatility across different types of metal. Several key differences exist between laser and plasma cutting:
Cutting technology: Plasma cutters use a mixture of gases with an electrical arc, while laser cutters use a focused beam of light.
Precision: In plasma cutting, there are some cutting jobs that high-definition plasma cutters can’t handle; e.g., cutting a finely detailed saw blade. By comparison, laser cutters offer a much higher level of precision and tolerance.
Capital investment required: Plasma cutting is relatively low, while laser cutting is considerably higher.
Cutting speed: Plasma cutters are relatively slow, while laser cutters can generally cut metal quicker than plasma cutters and use less energy, making them an eco-friendlier metal cutting option.
Cutting thickness: Plasma cutters can generally cut through any type of metal up to 80 mm thick. In contrast, laser cutters generally cannot cut materials as thick as plasma cutters can, and usually can only efficiently cut materials that are up to 25 mm thick.
Versatility: Plasma cutters are limited to cutting; however, they can cut all types of metal. Laser cutters can cut, engrave, and weld and can be used to cut through nonmetals, ceramics, and glass.
As shown above, laser cutting has several advantages over plasma cutting. First is the material range—laser cutting can be used in all materials common in industrial processing, from steel to aluminum, stainless steel, and non-ferrous metal sheets, to non-metal materials such as plastics, glass, wood, or ceramics. Second, there is contour freedom, in that the bundled laser beam only heats up the material locally and the rest of the workpiece is subjected to little-to-no thermal stresses. This means the kerf is barely wider than the beam and complex, which enables the smooth cutting of intricate contours free of burrs. Laser cutting can also produce high-quality cutting edges with ultrashort pulses that vaporize virtually every material so quickly that heat influence cannot be detected, thereby creating high-quality cutting edges without ejection of melted material. This makes the lasers ideal for the manufacture of the most intricate metal products, such as stents for medical technology and cutting chemically hardened glass for the display industry.
Fiber lasers
The first commercial laser devices, which appeared on the market in the late 1980s, used single-mode diode pumping, emitting only a few tens of milliwatts. For many laser applications, however, watts of optical power rather than milliwatts were required and the jump to watt-level fiber-laser output was made with the introduction of a 4 W erbium-doped fiber laser. This development laid the groundwork for the golden age of laser cutting development in the 1990s, when 10 W and higher single-mode fiber lasers suitable for micromachining and other applications—the first true high-power fiber lasers—were developed.
Soon, more high-powered lasers came onto the market with the ability to cut in large volumes. In the early 2000s, fiber laser cutting was introduced to the commercial market. The first fiber lasers for cutting reflective metals were introduced in 2008 and different laser beam conveying methods allowed cutting metals such as aluminum, brass, copper, and galvanized steel.
Current state of the market
In 2020, the global market for laser cutting machines was estimated at US$4.3 billion and was projected to reach US$7.3 billion by 2027, growing at a CAGR of 8%.1 The main market drivers identified were the growing demand for highly efficient and precise technology capable of producing smooth finishing, together with the demand for high processing speeds and easy programming technology from various manufacturing sectors such as defense, consumer electronics, and automotive.
According to Martino Burlamacchi, president of the Italian group Cutlite Penta, a developer and manufacturer of both fiber and CO2 laser systems, the availability of super high-power fiber laser sources has greatly improved laser cutting technology and the competitive positioning of lasers vs. mechanical cutting and plasma. Since 2021, Cutlite Penta has installed more than 250 laser cutting machines of over 20 kW. As a result, laser cutting speeds on 20- to 50-mm-thick materials are now up to 3X faster than plasma, making the laser faster, cheaper, more precise, more efficient, and more sustainable than competitive technologies (see Fig. 1).
New markets have opened for high-power laser cutting, including steel structures, shipyards, and construction machineries. For Martino, the laser substitution of plasma is leading the way to a sustainable revolution in which the investment for materials and electricity promise to generate consistent savings of CO2 emissions.Michael Hepp, product line manager of cutting at nLight, a U.S. a supplier of high-power fiber lasers, confirms that high-power fiber lasers have shown impressive productivity gains for metal cutting at thicknesses between 5 and 20 mm with nitrogen assist. He says in his experience, raw power has proven less useful for thin sheet, where other tool characteristics limit the speed; and also for thick steel, where oxygen assist is used. In these cases, other technological improvements, particularly beam shaping, have enabled significant advances in speed and quality. In Hepp’s view, laser power is an incomplete metric for measuring tool productivity, particularly in a job shop requiring flexibility in material and thickness. Thus, the focus for someone purchasing a tool is to understand which parameters provide productivity gains that are most valuable to their business, and to apply their investment dollars there.
Hendrik Meidert, senior product manager of TruLaser at TRUMPF, also sounds a note of caution regarding the limitations of high power alone. He points out that while laser powers of 30 kW or more can further increase laser cutting productivity, especially with fusion cutting, and have the potential to replace other processing methods with thick sheet, they can only be used in an economically and ecologically sustainable manner with sheet thicknesses for which high cutting speeds can also be converted into significantly shorter processing times for parts or sheets. This depends on the user’s part and material mix. The machine must have a high utilization rate to reduce part costs. This, in turn, requires suitable mechanical and optical components as well as functions to increase autonomy. The user must also take organizational measures to ensure smooth material supply and finished part removal so bottlenecks do not occur. For these reasons, and due to the decreasing marginal benefit of ultrahigh-power lasers, TRUMPF assumes laser powers between 6 to 25 kW will remain optimal for many applications.
Markus Kogel-Hollacher, R&D manager at Precitec, which manufactures laser-cutting heads, emphasizes the importance of the relationship between productivity and the laser’s optical elements. There is an almost linear dependence between laser power and productivity, at least in the power range up to 30 kW; at these powers, the behavior of the laser-cutting heads comes into focus, because they must function for 24/7 operation with constant cutting quality guaranteed throughout production.For this reason, Precitec has been studying the behavior of optical elements and perfected the reliable ProCutter 2.0 for 30 kW laser power (see Fig. 4). It is compatible with all laser sources, offers a higher NA of 0.18, and is super compact, lightweight, and equally suitable for bevel cutting. The cutting head operates automatically and with long-term stability up to 30 kW laser power, thanks to its sophisticated cooling concept, integrated sensors, and extended adjustment range.
In the current laser cutting market, there is an increase in the power of fiber lasers, which has greatly improved the versatility and productivity of laser cutting technology and the competitive positioning of lasers vs. mechanical cutting and plasma.
REFERENCE
1. Laser Cutting Machines – Global Market Trajectory & Analytics, Research and Markets (2021).
About the Author
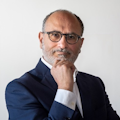
Antonio Raspa
Ultrafast Solid-State Laser Product Manager, Luxinar
Antonio Raspa is ultrafast solid-state laser product manager at Luxinar (Kingston upon Hull, U.K.), and an editorial advisory board member at Laser Focus World. He has more than 35 years of experience with solid-state laser design, photonics components, and fiber optics.
He holds a MSc degree in Electrical Engineering from Politecnico di Milano with a specialization in Quantum Electronics. Before joining Luxinar, he served as senior photonics program manager at the European Photonics Industry Consortium (EPIC; May 2020 – September 2022), preceded by Quanta System (1988-2000) as R&D manager for the development of solid-state laser sources and custom photonics systems for industrial and scientific applications. During this period, he participated, as Ozone LiDAR specialist, to the Italian research program in Antarctica. He then worked at Trumpf (2000-2008) and Rofin-Sinar (2008-2009) as a Product Manager for industrial laser products and processes. In 2009 he returned to Quanta System, organizing and managing a new plant for the production of sterile optical fibers for surgery.