A robotic hand that has bones, ligaments, and tendons almost sounds like something out of a sci-fi movie. But it’s actually very real, thanks to a team of researchers at ETH Zurich (Zurich, Switzerland) and engineers from Inkbit, a Massachusetts Institute of Technology (MIT; Boston, MA) spinoff additive manufacturing startup (see Fig. 1).
The collaborative team has developed a laser scanning technique called vision-controlled jetting (VCJ), an inkjet deposition process that continuously scans the print surface using lasers and high-frame-rate cameras (see video below).
Conventionally, 3D printers create an object layer by layer; each layer is then cured immediately under an ultraviolet (UV) lamp. Following each curing step, surface irregularities are scraped off—but this only works with fast-curing materials such as polyacrylates. Slow-curing polymers hamper the printing process because it takes longer for them to solidify.
As slow-curing polymers including thiol-ene and epoxies are ultimately more robust and durable, resistant to UV light and humidity, and tout more advanced elastic qualities than conventional fast-curing polymers, the researchers say they show great promise for biomedical products—medical implants and organs-on-a-chip, for example.
The VCJ approach allows real-time scanning of the printed layers to immediately check for surface irregularities before the curing process, explains Thomas Buchner, a researcher with ETH Zurich’s Soft Robotics Lab. And it’s done without slowing the printing process. VCJ uses the scan data and corrects for flatness in each consecutive layer contact-free, which Buchner says allows the use of materials “with advantageous features like UV stability and springiness that would clog conventional contact-based inkjet printers using mechanical planarizers.”
Soft, elastic, and rigid materials can be 3D-printed, thanks to VCJ, to create structures that are delicate and more complex. The team’s robotic hand, complete with multifaceted features including bones, ligaments, and tendons, is a prime example (see Fig. 2 and video below). Slow-curing plastics also tout long lifespans, Buchner says, prints of such materials via the VCJ system “is handy for research and commercial applications.”
The background
The work on what has become the VCJ system began about eight years ago with research published in ACM Transactions on Graphics. This initial work used a full-field optical coherence tomography (OCT) setup as part of an extension of an initial printer developed by a team at MIT. That original scanner met the technical requirements, says Aaron Weber, Inkbit’s director of engineering, but ultimately became too expensive to implement into a commercial 3D printer. The setup was also quite slow.
Further development of the technology allowed the team to modify the 3D scanning system into one that is based on classic triangulation—a more cost-effective approach (see Fig. 3).
“We have been able to achieve our cost, speed, and resolution requirements through the careful selection of off-the-shelf components mounted in a custom mechanical package,” Weber says. “We now have the flexibility to swap in individual components to match changes in material properties without having to change the entire scanning architecture.”
The ETH Zurich team got involved in 2020.
“Technologically, we could print multimaterials and print at scale starting in 2021,” Buchner says. “Together, we’ve pushed the VCJ technology to what it is now.”
The future
Next on the ETH/Inkbit team’s agenda is a focus on robotics applications (see Fig. 4). Buchner says they are working to develop a customized solution enabled by the vision-controlled printing technology, and plan to investigate how soft, rigid structures can provide scaffolds for biological cells.
He cites artificial intelligence (AI), virtual reality (VR), and the Metaverse as other areas to investigate. Advances in 3D printing will make digital ideas become physical reality. Generative AI can start creating 3D objects, which Buchner says a VCJ-involved 3D printer will be able to realize, “no matter how complex the arrangement of material voxels is.”
“We can create customized and personalized products faster now,” Buchner adds. “Prototyping can be closer to a final product, assembly times are minimized as they are complete, and functional systems can be printed in a single process.”
FURTHER READING
T. J. K. Buchner et al., Nature, 623, 522–530 (2023); https://doi.org/10.1038/s41586-023-06684-3.
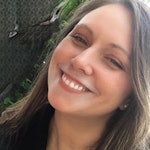
Justine Murphy | Multimedia Director, Digital Infrastructure
Justine Murphy is the multimedia director for Endeavor Business Media's Digital Infrastructure Group. She is a multiple award-winning writer and editor with more 20 years of experience in newspaper publishing as well as public relations, marketing, and communications. For nearly 10 years, she has covered all facets of the optics and photonics industry as an editor, writer, web news anchor, and podcast host for an internationally reaching magazine publishing company. Her work has earned accolades from the New England Press Association as well as the SIIA/Jesse H. Neal Awards. She received a B.A. from the Massachusetts College of Liberal Arts.