High-power Laser Diodes: Diode-laser enhancements boost efficiency and reliability
High-power diode lasers have become the workhorses of industrial laser technology: They are at the heart of every fiber laser, they pump disk and other solid-state lasers as well, and they are increasingly often used in direct-diode applications.
The development of diode lasers follows the priorities of their industrial users, with a key performance indicator expressed in the cost-per-watt relation. Diode lasers have been available in ever-improving commercial quantities and qualities for quite some time, but it has taken important improvements in performance to enable new areas of application. And diode lasers are still advancing—in particular, their efficiency, peak power, brilliance, and range of emission spectra. Academic research has resulted in new performance records, including more than 60% conversion efficiency at 1 kW and output powers of more than 1.5 kW from a 1 cm bar.1
275 W from a passively cooled bar
Further improvements in output power require complex design considerations regarding materials, solid-state physics, thermal processes, and optics, to name just the most important. And, while a laser system can be optimized for higher output power, this can’t be achieved separately from the optimization of other parameters such as lifetime, efficiency, and beam quality.
Based on decades of research, Jenoptik has developed a new modular diode laser that is passively cooled and suitable for hard-pulse (in which the laser is cycled between on and off states on time scales of about one second) and continuous-wave (CW) conditions. It has been tested for output powers of more than 400 W (see Fig. 1). The actual working output level has been set to 275 W to ensure the highest power-conversion efficiency of 60% and maximum lifetime.
Compared to diode lasers from other manufacturers, the output power of the new device is more than doubled; in comparison with previous Jenoptik diode lasers, the output power has increased by more than 40%. This progress is the result of a change in the cooling scheme (see Fig. 2). The new design uses a double-side cooling arrangement in which the heat sink extends beyond the actual exit facet. A numerical simulation of the heat-conduction processes shows the temperature distribution in the diode laser under realistic conditions.At a heat load of 200 W (corresponding to an optical output power of 275 W) and a thermal resistance of the cooling plate of 0.05 K/W at room temperature, the previous Jenoptik design heats up to a maximum of 76°C, whereas the new design reaches a maximum temperature of only 68°C.
Nonsoldered joining improves reliability
The diode is attached to its copper heat sink with hard alloy, which allows for high stability when the power is switched. Depending on the driver electronics, the diode laser can be “hard pulsed”—that is, turned off and on to maximum power repetitively without technical limitations.
The conventional way to mount a gallium arsenide (GaAs) laser bar to a copper heatsink is indium soldering. Copper is well known for its advantages as a heatsink material, which include high thermal conductivity, low cost, and easy processing. The problem with copper is the large difference in the coefficient of thermal expansion (CTE) in comparison to GaAs (in other words, a CTE mismatch). This leads to mechanical stress when the system changes its temperature. The extraordinary softness and ductility of indium is required to prevent GaAs from cracking when cooling down after soldering. But these soft and ductile properties of indium are what lead to fatigue of the solder join under hard pulsed conditions.
Jenoptik uses a novel approach with a much stronger metallic join. It comprises a new structure in which a nonsoldered metallic joining layer is used between two metallic buffer layers (see Fig. 3). The strength of the joining material makes it resistant to the stress generated by hard pulsed operation, making the usage of copper possible.Upscaling to multikilowatt power
The assembly technology and new cooling scheme allow the diode laser to be used in a passive cooling mode. With a footprint of about one square inch, it is well suited for the creation of a diode array from a large number of individual diode bars. High-power systems using modules that add up to 10 kW are a typical use case for these diode lasers.
Jenoptik has engineered a test module with a size of 104 mm total length and 36 mm width (54 mm with cooling connector). It consists of four diode bars and a cooling element that is prepared for additional water cooling (see Fig. 4). For comparison, a similar setup with conventional 80 W bars would require about 14 bars plus cooling.Applications from materials processing to healthcare
The new technology enables simple modules with a small footprint that can serve in all kinds of materials processing tasks such as cutting, welding, and brazing. New applications such as laser cleaning may immediately benefit from the 50% saving in the form factor and less complex systems.
Uses other than materials processing exist that benefit from the high power of these lasers as well, such as laser printing and marking. Applications in the healthcare sector usually do not depend on the highest available power—here, laser lifetime is more important and can be extended substantially by running at lower power levels. Furthermore, a diode laser can be coupled with an optical fiber to deliver the power to the point of treatment at the patient.
REFERENCE
1. P. Crump and A. Thoss, “Diode Lasers: Research gives high-power diode lasers new capabilities,” Laser Focus World, 55, 1, 77–80 (Jan. 2019); http://bit.ly/ThossRef1.
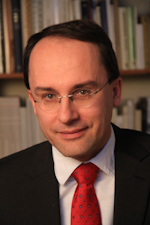
Andreas Thoss | Contributing Editor, Germany
Andreas Thoss is the Managing Director of THOSS Media (Berlin) and has many years of experience in photonics-related research, publishing, marketing, and public relations. He worked with John Wiley & Sons until 2010, when he founded THOSS Media. In 2012, he founded the scientific journal Advanced Optical Technologies. His university research focused on ultrashort and ultra-intense laser pulses, and he holds several patents.
Matthias Schröder | Project Manager, Jenoptik Laser
Matthias Schröder is Project Manager at Jenoptik Laser (Jena, Germany).
Marco Koschorreck | Head of R&D, Jenoptik Laser
Marco Koschorreck is Head of R&D at Jenoptik Laser (Jena, Germany).