Photonic Textiles: Laser lithography produces waterproof energy-storing cloth for smart garments
A supercapacitor with conductive graphene elements patterned using a combination of carbon-dioxide (CO2) and ultrafast lasers was created on nylon cloth.
Scientists from RMIT University (Melbourne, Australia) have developed a cost-efficient and scalable laser-printing method for rapidly fabricating textiles that are embedded with energy-storage devices. In three minutes, the method can produce a 10 × 10 cm smart-textile patch that is waterproof, stretchable, and readily integrated with energy-harvesting technologies.1
The technology enables graphene supercapacitors (energy-storage devices) to be laser-printed directly onto textiles such as nylon. In a proof of concept, the researchers connected a laser-printed supercapacitor with a photovoltaic cell to produce an efficient, washable, self-powering smart fabric that they say overcomes the key drawbacks of existing e-textile energy-storage technologies.
The growing smart-fabrics industry has applications in wearable devices for the consumer, healthcare, and defense sectors, including monitoring vital signs of patients, tracking the location and health status of soldiers in the field, and monitoring pilots and drivers for fatigue. Such textiles are ideally self-powered, leading to the inclusion of an energy harvester such as a photovoltaic cell or piezoelectric generator—and, of course, energy storage. In one approach, lithium batteries are glued or sewn into smart fabrics; another, which comprises fiber bundles with electrolytes and electrodes that form batteries, has low energy-storage capability.
“Current approaches to smart-textile energy storage, like stitching batteries into garments or using e-fibers, can be cumbersome and heavy and can also have capacity issues,” says Litty Thekkekara, a researcher in RMIT’s School of Science. “These electronic components can also suffer short-circuits and mechanical failure when they come into contact with sweat or with moisture from the environment. Our graphene-based supercapacitor is not only fully washable, it can store the energy needed to power an intelligent garment, and it can be made in minutes at large scale."
The research analyzed the performance of the proof-of-concept smart textile across a range of mechanical, temperature, and washability tests and found that it remained stable and efficient.
Lithographic fabrication
In the process, an elastomer solution made from polydimethylsiloxane (PDMS) is coated onto one side of nylon fabric while a graphene oxide and binder solution is painted on the other and dried to form a film 3 μm thick. A combination of a continuous-wave (CW) CO2 laser and a femtosecond laser was used to pattern the fabric; the CO2 laser provides photothermal reduction and the ultrafast laser provides a combination of photothermal and photochemical reduction. The combination is a single-step optical lithographic fabrication method leading to conductive fractal-patterned graphene films on the fabric; supercapacitor electrodes 10 μm thick over an area of 100 cm2 with an interelectrode distance of 80 μm were created.
For the photoreduction process, the CO2 laser beam was focused with an objective lens with a numerical aperture (NA) of 0.35. Photoreduction occurred for laser powers of 4.5 W up to 8 W, at which film breakdown occurred; the optimum power was found to be around 6 W. After washing and drying the resulting graphene-enhanced cloth 50 times in commercial laundering machines, it was found that the electrical conductivity of the thin film had not changed much from its initial state.
A polyvinylalcohol (PVA)/sulphuric acid (H2SO4) gel electrolyte was used in the supercapacitor. Both unencapsulated and encapsulated (with another layer of coated fabric) versions were fabricated, leading to energy storage densities of 3.45 mF/cm2 for the unencapsulated and 27 mF/cm2 for the encapsulated versions. After washing 50 times in commercial laundering machines, the retention of capacitance was 80%.
Min Gu, a researcher at RMIT and also at the University of Shanghai for Science and Technology, says the technology could enable real-time storage of renewable energy for e-textiles. “It also opens the possibility for faster roll-to-roll fabrication, with the use of advanced laser printing based on multifocal fabrication and machine learning techniques,” Gu notes.
The researchers have applied for a patent for the new technology, which was developed with support from RMIT Seed Fund and Design Hub project grants.
REFERENCE
1. L. V. Thekkekara and M. Gu, Sci. Rep. (2019); https://doi.org/10.1038/s41598-019-48320-z.
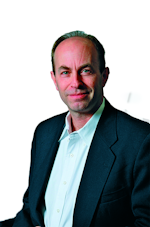
John Wallace | Senior Technical Editor (1998-2022)
John Wallace was with Laser Focus World for nearly 25 years, retiring in late June 2022. He obtained a bachelor's degree in mechanical engineering and physics at Rutgers University and a master's in optical engineering at the University of Rochester. Before becoming an editor, John worked as an engineer at RCA, Exxon, Eastman Kodak, and GCA Corporation.