EKOLAS research project leads to novel laser bars with 70% wall-plug efficiency
The number of infrared-light-based applications has multiplied in recent years. Long before infrared LEDs and VCSELs were used as light sources for facial recognition in smartphones, early manufacturers developed infrared lasers. Osram Opto Semiconductors (Munich, Germany) has been working for many years on high-power lasers for special applications such as metal processing using welding robots in the automotive industry. Osram, along with its partners, is now presenting the laser bars’ performance and efficiency results from the latest EKOLAS project, which was funded by the German Federal Ministry of Education and Research (BMBF).
In recent years, state-of-the-art laser technology has become an indispensable component for various industries, from medical technology to car manufacturing. The Efficient High-Performance Laser Beam Sources (EffiLAS) association is focused on securing and expanding Germany's leading technological and economic position in photonics. The aim of the association is to optimize various laser parameters such as performance and energy efficiency.
Laser bar with 70% efficiency at 300 W output
Together with its partners Laserline, Heraeus, Fraunhofer ILT, fiberware, and Welser Profile, Osram has worked on various assignments in the EffiLAS joint project EKOLAS. The main aim was to develop highly efficient infrared laser bars with outstanding output powers and to demonstrate them in industrial materials processing. About 10 years ago, the best laser bars achieved a power of 200 W with an efficiency of about 63%. Five years later, an output of 250 watts at an efficiency of no less than 60% was expected to be the limit of what could be achieved with the existing technologies. Conversion efficiency and cooling limited the output power of lasers at that time. The EKOLAS project, which was completed in February 2020, led to the development of an infrared laser bar with a maximum output of 400 W in continuous wave operation. With an output of 300 W, the bar sets a new standard with an efficiency of about 70% in the wavelengths of 1000 and 1020 nm.
The project partners were able to draw on experience gained in other ventures under the EffiLAS umbrella organization, including an understanding of materials science and simulation in the field of epitaxy, as well as fundamental expertise in chip and facet technologies.
"We are very excited to achieve, and in some cases even exceed, all of our targets in this project," says Sebastian Hein, EKOLAS Project Manager at Osram Opto Semiconductors. "The key to success was the development of innovative software tools for simulating the electro-optical properties of the lasers, which take into account the thermal distribution, temperature-dependent material properties and mode-dependent wave propagation in the resonator. These tools accelerated and simplified the necessary test runs, making a fundamental contribution to the results of the project.”
The newly gained knowledge from the simulation of certain processes can now be applied to other product groups and wavelengths in the range between 800 and 1060 nm. In addition to the advantages in product development, the results also bolster and consolidate the establishment of supply chains in Germany and the rest of Europe, thereby sustainably strengthening the industrial location.
For more info on EffiLAS, see https://www.effilas.de/en.html.
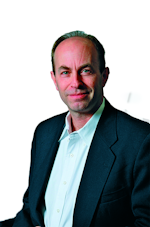
John Wallace | Senior Technical Editor (1998-2022)
John Wallace was with Laser Focus World for nearly 25 years, retiring in late June 2022. He obtained a bachelor's degree in mechanical engineering and physics at Rutgers University and a master's in optical engineering at the University of Rochester. Before becoming an editor, John worked as an engineer at RCA, Exxon, Eastman Kodak, and GCA Corporation.