Photopolymer resins boost visible-light curing speed
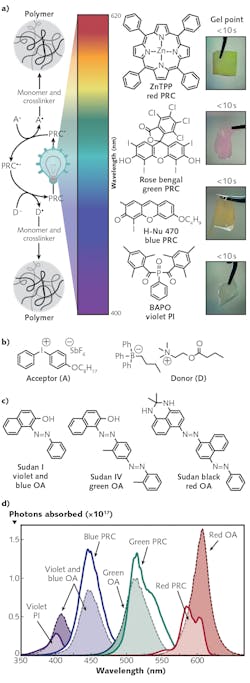
Engineering innovations in 3D printing methods such as stereolithography (SLA) and digital light processing (DLP) have driven design advances in fields ranging from aerospace to medicine. Such light-induced polymerization processes typically rely on relatively high-photon-energy ultraviolet (UV) light curing to transform liquid resins into solid objects. While using visible light for curing would offer advantages including reduced cost, improved biocompatibility, greater depth of light penetration, and reduced light scattering, visible-light curing has been too slow to be practical.
Now, chemical innovation in the form of novel resins developed by a team of researchers led by Zachariah A. Page, Assistant Professor of Chemistry at The University of Texas (Austin, TX), speed visible-light curing, with the promise of opening up new applications for 3D printing such as making opaque composites, multimaterial structures, and hydrogels containing live cells. The researchers developed violet-, blue-, green-, and red-colored resins that contain a monomer, a photoredox catalyst (PRC), two coinitiators, and an opaquing agent. When the PRC absorbed visible light from LEDs, it catalyzed the transfer of electrons between the coinitiators, which generated radicals that caused the monomer to polymerize.
“The innovation stems from the novel resins that contain a three-component light-reactive system, which enables rapid and efficient curing with low-energy visible light,” explains Page. “Additionally, the printer employed uses approximately monochromatic light-emitting diodes spanning the visible spectrum from violet to red, which goes beyond contemporary light-based 3D printers that rely on high-energy UV/violet light for photocuring.”
An opaquing agent helps confine curing to the areas struck by light, which improves spatial resolution. The optimized compounds enabled the printing of stiff and soft objects with small features (less than 100 μm), mechanical uniformity, and build speeds up to 1.8 inches per hour. Although the best build speed is still less than half that of the fastest rate obtained using UV light, it could be further improved by increasing the light intensity or adding other components to the resin, according to the researchers.
Materials photochemistry
Improving visible light photocuring efficiency requires a chemical understanding of how reactive curing agents (e.g., radicals or ions) are generated. Following absorption of light by a chromophore, photocuring occurs by one of two mechanisms: either direct photolysis of a photoinitiator (PI), or electron transfer from a PRC to a coinitiator followed by bond scission to generate radicals or ions.
Replicating traditional UV-based rapid high-resolution DLP 3D printing with low-energy visible LEDs necessitated the development of reactive panchromatic resins. These light-sensitive polymer resins incorporated monomer, crosslinker, and a PI or PRC + coinitiators. The monomer, crosslinker, and PI were held constant, while various PRC and coinitiator compounds were rationally combined to obtain a mixture that enables photocuring on the order of seconds. Specifically, three-component systems (PRC + two coinitiators) were examined to both promote PRC regeneration and potentially double the concentration of radicals produced per photon absorbed.
For Fourier-transform infrared (FTIR) spectroscopy and photorheology experiments, violet, blue, green, and red light was provided by collimated LCS series LEDs from Mightex Systems (Toronto, ON, Canada) with emission wavelengths centered at 405, 460, 525, and 615 nm (see Fig. 1). These LEDs were used in combination with a Mightex Systems SLC-MA02-U current-adjustable driver for intensity control, such that all intensities between experiments (printing, FTIR, and photorheology) could be matched. Light was delivered via a liquid light guide. Irradiation intensities were measured with a PM100D photometer from Thorlabs (Newton, NJ) equipped with Thorlabs S120VC silicon-based photodiode power sensor. Emission profiles were recorded with a QE pro spectrometer, in which the LED was connected to the fiber-optic system using a Mightex Systems 3-mm-diameter liquid lightguide.
3D printing
3D printing was performed using a custom-made, DLP-based 3D printer (Monoprinter, MA), which is compatible with four different exchangeable visible LEDs centered at 405 nm (violet, Luminus CBT-120-UV), 460 nm (blue, Luminus PT-120-B), 525 nm (green, Luminus PT-120-G), and 615 nm (red, Luminus PT-120-RA). Each LED contains a 12 mm2 emission surface area and a maximum current up to 30 A. The full width at half maximum (FWHM) of each LED is 16, 20, 34, and 19 nm for violet, blue, green, and red light, respectively.
Optical setup of the 3D printer uses two collimating lenses in front of each LED chip to align the LED light along the optical axis. Subsequently, an optical diffuser provides light homogenization. The relay-lens assembly comprises three convex lenses. MonoWare custom software was used to import STL design files and digitally slice them into a sequence of 2D image files for projection. The digital micromirror device (DMD) processes the signal delivered from the software and reflects the light towards or away from the lens, resulting in a pixel appearing bright or dark at the resin vat, respectively.
“We envision that visible-light 3D printing will facilitate lower-energy-consumption, next-generation 3D printers, including the LCD/LED 3D printers that are growing in popularity, as these don’t typically operate effectively in the UV range,” says Page. “Furthermore, we view visible-light 3D printing an integral step towards low-cost and portable multimaterial stereolithography.”
As such, visible-light photocuring has the potential to enable next-generation designer material fabrication, including wavelength-selective multimaterial structures that promise to advance a range of applications, from structural plastics (see Fig. 2) to tissue engineering and soft robotics.“In addition to multimaterial stereolithography, we anticipate that longer wavelengths of light will enable the production of composites that contain UV-absorbing or sensitive materials, such as particles that scatter light or biomaterials that degrade upon extended exposure,” concludes Page.
REFERENCE
1. D. Ahn et al., ACS Cent. Sci. (2020); https://pubs.acs.org/doi/10.1021/acscentsci.0c00929. (Note: Further permissions related to the material excerpted should be directed to the ACS.)
About the Author
John Lewis
Editor in Chief (2018-2021)
John Lewis served as Editor in Chief of Laser Focus World from August 2018 through October 2021, after having served as the Editor in Chief of Vision Systems Design from 2016 to 2018. He has technical, industry, and journalistic qualifications, with more than 13 years of progressive content development experience working at Cognex Corporation. Prior to Cognex where his articles on machine vision were published in dozens of trade journals, he was a technical editor for Design News, covering automation, machine vision, and other engineering topics, for over six years.