Disk-laser power-scaling limits examined and potentially counteracted

A group of Swiss, French, and German researchers has determined through computer modeling that further increasing the output power of very high-power thin-disk lasers can be hindered by effects arising from thermal distortion of the disk and mount, which then causes misalignments. The group has also developed, again through computer modeling, a way to design thin-disk laser resonators that are insensitive to this thermal effect. The researchers hail from the Institute for Particle Physics (Zurich, Switzerland), the Paul Scherrer Institute (Villigen-PSI, Switzerland), ENS-PSL Research University at College de France (Paris, France), the Max Planck Institute of Quantum Optics (Garching, Germany), and Johannes Gutenberg Universität Mainz (Mainz, Germany).
A high-power thin-disk laser gain medium typically has a thickness of 100 to 400 μm, has a dielectric rear mirror, and is water-cooled via its back face. Because the disk is so thin in the direction of the laser axis, the temperature gradient within the disk is almost entirely in the axial direction, and thus one-dimensional and minimizing thermal-lensing effects—one of the great advantages of the disk laser, allowing power scalability. But at a high-enough power, the high heat load causes the disk to bend the disk/heat-sink assembly, misaligning the resonator (because the pump beam comes in at an angle to the normal), further worsening performance as the off-center beam heats the disk lopsidedly. In one example, a 20-mm-diameter, 140-μm-thick ytterbium-doped YAG (Yb:YAG) disk receiving a heat load of 50 W/mm3 results in a 1 mm lateral misalignment as the resonator warps and moves the beam. The researchers define a parameter G that should be minimized for proper resonator design-in another approach, active feedback could be used to keep the beam centered. Reference: K. Schuhmann et al., arXiv:1607.08873v1 (Jul. 29, 2016).
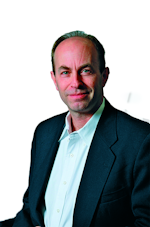
John Wallace | Senior Technical Editor (1998-2022)
John Wallace was with Laser Focus World for nearly 25 years, retiring in late June 2022. He obtained a bachelor's degree in mechanical engineering and physics at Rutgers University and a master's in optical engineering at the University of Rochester. Before becoming an editor, John worked as an engineer at RCA, Exxon, Eastman Kodak, and GCA Corporation.