Photonic Frontiers: High-efficiency Optical Pumping: 'Going green' cranks up the laser power
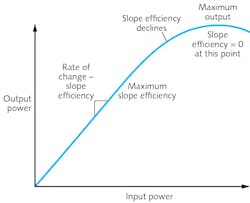
Efficient laser diode pumping launched the solid-state laser revolution. Flashlamp pumping was standard in 1990, but after three decades of development, the typical wall-plug efficiency for a neodymium laser was only 1%.1 Diode pumping dramatically increased wall-plug efficiency in three ways: more efficient conversion of electric power into light, more directional output, and better-matching narrow pump bands. That allowed wall-plug efficiency in the 10% range for neodymium diode-pumped lasers at 808 nm, but the diodes came at a steep price premium.
Diode pumping now dominates the solid-state market, with typical wall-plug efficiency at high powers in the 30% range and the best on the market exceeding 50%. Ytterbium has replaced neodymium as the dominant active laser material because of its higher diode-pumped efficiency. Fibers and thin disks have pushed rods from the market spotlight because of their higher efficiency. And developers continue pushing for higher optical pumping efficiency to improve laser performance, especially at high powers.
Measuring efficiency
Optical pumping efficiency can be measured in different ways.
The overall or "wall-plug" efficiency measures what fraction of the input electrical power emerges as laser power. This is the product of several factors: power-supply efficiency, the laser diode's light-emitting efficiency, efficiency of coupling pump light into the laser medium, pump light absorption, how many pump photons stimulate emission, the quantum defect or energy difference between pump and output photon, and laser cavity. It's the usual overall measurement.
Two other efficiencies also can be useful:
- Optical-to-optical efficiency-the ratio of input pump power to output laser power; and
- Slope efficiency-the increase of output power per unit input power above threshold. This is the linear part of the curve in Fig. 1, which shows how output increases linearly and then slows down before reaching maximum output power.
Pump laser diodes
Pump laser diodes are a key part of the efficiency equation, and their importance goes beyond simple electrical-to-optical conversion efficiency, says Marty Hemenway, lead optical engineer at nLight (Vancouver, WA). Diode bars emit light more efficiently than single-element diode chips, and they also cost less per watt of power. However, diode chips emit brighter, more concentrated beams that excite the active laser material more efficiently.
Design decisions depend on the specific case (see Fig. 2). For pumping fiber lasers, system efficiency depends strongly on the brightness delivered to the fiber, so the tradeoff favors the brightness of a chip over the higher but more diffuse power from a bar. Thin disks and bulk solid-state lasers are different because the diode pumps a broad area. In that case, Hemenway says, "it's less about brightness and more about power," so bars may be more efficient. Further complications come from factors such as temperature, which affects chip performance and reliability, and other details of the application.Ytterbium and high efficiency
Efficiency depends on the choice of the laser material as well as its structure, with ytterbium offering the best efficiency. It has one broad pump band at 915–940 nm, and a narrower but stronger band peaking at 976 nm. Both fall within the range of InGaAs laser diodes, which are particularly efficient emitters, and the longer-wavelength peak is "as good as it gets" for diode efficiency, says Bill Krupke, principal of WFK Lasers (Pleasanton, CA).
Moreover, the Stokes shift between the pump and the output is small in ytterbium. A 976 nm pump diode can power strong laser emission at 1030 nm for a quantum defect of only 6%. That helps ytterbium-doped fibers reach optical-to-optical conversion efficiency of 90% in the amplifier stage of a master-oscillator/power amplifier configuration.
Very high-efficiency fiber lasers
Good coupling of pump light into the gain medium also enhances efficiency of fiber lasers. Typical fiber lasers use the dual-core structure (see Fig. 3), with pump light coupled into the larger outer core and laser ions doped into the inner core, where laser emission occurs. Asymmetry of the outer core ensures that total internal reflection directs pump repeatedly through the inner core to excite the laser species. The inner core confines stimulated emission and produces a high-quality beam.Typical high-power ytterbium-fiber lasers for industrial applications have wall-plug efficiency over 30%, with output to 10 kW single-mode and 100 kW multimode. The highest wall-plug efficiency in a commercial laser is more than 50% from the ECO laser series, delivering up to 6 kW continuous-wave (CW), made by IPG Photonics (Oxford, MA). To achieve that high efficiency, the pump diodes are operated at peak efficiency rather than peak power. The need for more pump diodes to reach the desired power raises the laser price, but it's a cost-effective choice in countries like Japan with very expensive power.
The long interaction length of fiber lasers also brings tradeoffs at high powers. Nonlinearity increases with length of the laser medium, especially in single-mode lasers, so developers have switched to large-mode-area fibers to reduce power density in the fiber. That reduces nonlinear Brillouin scattering, which depletes laser power in the inner core, thus reducing efficiency.
Efficiency also becomes important at high powers to avoid a problem discovered about five years ago—sudden power drops caused by multimode instability.2 Excess heat causes thermal-optic effects to produce a gradient within the fiber. Above a threshold value, this can create two modes in the 20 to 25 μm core of a large-area fiber, and beating of those modes caused severe fluctuations. Now, progress is being made in suppressing it. At SPIE Photonics West 2016 in February, Nader Naderi of the Air Force Research Laboratory (Kirtland, NM) and colleagues reported kilowatt output with 84% slope efficiency in an amplifier with near-diffraction limited output, and "no sign of modal instability." They attributed their success to modulating the single-frequency master oscillator with a pseudo-random bit sequence and optimizing design.
Quest for eye-safe high-power lasers
The 1030–1080 nm ytterbium laser is far ahead in the quest for high power, but the Pentagon would prefer eye-safe lasers for tactical use to protect soldiers and civilians. The two leading candidates are thulium at 2 μm and erbium at about 1.6 μm, already available at CW powers to 200 W.
An important attraction of thulium is the efficiency possible by pumping it with 790 nm photons that can excite two thulium atoms in a cross-relaxation process. At Photonics West 2016, Alex Sincore of the University of Central Florida (Orlando, FL) and colleagues reported optical-to-optical efficiencies of 55–60% using that process. Krupke thinks thulium is the closest technology for high-power eye-safe lasers, but warns that sensors in the 2 μm band—needed to monitor the laser—are not well developed.
Sensors are much better near 1.6 μm, which Krupke thinks may make erbium-doped fibers a better long-term bet for eye safety. He notes that the Army Research Laboratory (Adelphi, MD) has doubled efficiency of 1480 nm indium gallium arsenide phosphide (InGaAsP) pump diodes that can pump erbium, which had been limited to about 20%. Another option is pumping with InGaAs diodes, and at Photonics West 2016, Daniel Creeden and colleagues at BAE Systems (Nashua, NH) described a 207 W erbium:ytterbium (Er:Yb) amplifier that achieved 50.5% slope efficiency, which they called the highest yet for pumping in the 900 nm band.
Diode-pumped alkali lasers
The Pentagon has a different optically pumped glimmer in its eye for longer-range megawatt-class lasers: diode-pumped alkali-vapor lasers, quasi-two-level lasers with very small quantum defects. In the early 2000s, Krupke showed that commercial diode lasers could efficiently pump rubidium, cesium, and potassium vapors.3 DILAS (Mainz, Germany) has demonstrated high-power pump diodes for all three.4
The leader so far has been rubidium, pumped at 780 nm—a wavelength readily available from gallium arsenide diodes. Rubidium vapor output is said to have reached the 10 kW range in unpublished experiments, with higher power in the works. Yet efficient operation requires about 10 atmospheres of helium as a buffer gas, complicating laser operation.
In the longer term, Krupke thinks potassium should prove more practical because it requires less than an atmosphere of helium buffer. It emits at 770 when pumped at 766 nm, a remarkably small quantum defect. So far, output has reached 1.5 kW with 50% optical-to-optical efficiency. The hope is that flowing gas systems could scale to higher powers than solid-state because of their high efficiency and easier cooling.
The future of efficiency
Optical pumping efficiency will continue increasing, but we're entering a transition zone where the benefits will change. Improving wall-plug efficiency of solid-state lasers from 1% to 50% reduces power bills and the size of the laser needed to do a job by a factor of 50. Going to 99% efficiency would only cut those numbers by a factor of two.
Yet improving efficiency from 50% to 99% efficiency would slash waste heat by a factor of 50, bringing other benefits. The most obvious would be greatly reducing the need for cooling water or massive refrigeration systems that outweigh the laser. More subtle benefits would come from pushing the envelope of laser performance by reducing heat-induced nonlinearities and refractive-index changes. And we could feel better by using less energy to become more productive.
REFERENCES
1. J. Hecht, The Laser Guidebook, 2nd ed., McGraw-Hill, New York, NY (1992).
2. C. Jauregui et al., Opt. Express, 20, 12, 12912 (Jun. 4, 2012).
3. W. F. Krupke et al., Opt. Lett., 28, 23, 2336–2338 (2003).
4. H. Kissel et al., "High-power diode laser pumps for alkali lasers (DPALs)," Proc. SPIE, 8241, High-Power Diode Laser Technology and Applications X, 82410Q (Feb. 9, 2012).
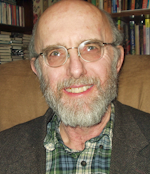
Jeff Hecht | Contributing Editor
Jeff Hecht is a regular contributing editor to Laser Focus World and has been covering the laser industry for 35 years. A prolific book author, Jeff's published works include “Understanding Fiber Optics,” “Understanding Lasers,” “The Laser Guidebook,” and “Beam Weapons: The Next Arms Race.” He also has written books on the histories of lasers and fiber optics, including “City of Light: The Story of Fiber Optics,” and “Beam: The Race to Make the Laser.” Find out more at jeffhecht.com.