Photonics Products: High-power Fiber Lasers: Kilowatt-level fiber lasers mature
Fiber lasers combine active (laser-gain) optical fiber with one or more pump lasers, usually laser diodes. The many types of fiber lasers include low-power continuous-wave (CW) and low- and high-energy pulsed, including ultrafast fiber lasers. But what comes to mind for many people are the "big guns"—the kilowatt-class CW fiber lasers that are predominantly used in materials processing, including cutting, welding, brazing, surface treatment, and other applications, but are also being developed for the military as directed-energy weapons.
A fiber is essentially a very skinny, long rod—its configuration makes it one of two types of lasers that have an especially high surface area-to-volume ratio, making them easier to keep cool (the other is the disk laser—a wide, extremely short rod). Fiber lasers are relatively simple in their construction and are easy to maintain. They are compact and, because they are pumped with laser diodes, rugged and long-lived.
Large range of powers and wavelengths
Alexei Markevitch, market development manager at IPG Photonics (Oxford, MA), outlines the range of wavelengths and powers available for kilowatt-class fiber lasers. "IPG manufactures standard kilowatt-class CW lasers at 1 μm (ytterbium-doped fiber) and 1.5 μm (erbium-doped fiber) and also manufactures custom kilowatt-class lasers at 2 μm (thulium doped fiber), along with lasers that have Raman-shifted wavelengths between 1.1 and 1.7 μm," he says. "The longer wavelengths enable nonmetal materials processing and other new applications and are considered to be eye-safe, as the eye-damage threshold is many orders of magnitude higher than for 1 μm lasers."
Markevitch notes that the kilowatt-class fiber laser systems operate in CW or modulated modes up to 5 kHz, and have dynamic range from 10% to full power with no change in beam divergence or beam profile.
At 1 μm, the company's single-mode YLS-SM ytterbium-doped fiber lasers span a power range from 1 to 10 kW, says Markevitch. These single-mode systems are used in advanced materials-processing applications requiring extremely high power and brightness, such as fine cutting and surface structuring, cutting high-reflectivity metals, microwelding, sintering, and engraving, as well as remote processing and directed-energy applications.
"[IPG's] multimode YLS ytterbium-doped CW fiber lasers span a power range from 1 to 100 kW and can be manufactured up to several hundreds of kilowatts upon customer request," says Markevitch. "Their many uses include cutting, drilling, brazing, welding, annealing, heat treating, and cladding. With continuous improvement in their design, wall-plug efficiencies of standard industrial YLS system have now reached over 40%, and the industry record YLS-ECO series has a WPE exceeding 50%."
The same multimode YLS lasers are used for both high and low-brightness applications such as welding, drilling, and precision cutting—"a previously unheard of capability," Markevitch says. "The high brightness allows the use of long-focal-length processing lenses for vastly improved depth of field and minimal damage to optical components."
While high-brightness multimode lasers dominate in materials-processing applications, single-mode kilowatt-class CW lasers are gaining increasing attention, as they enable new applications that require high CW peak power with very small spot sizes and/or remote processing capability. Some applications of YLS-SM lasers described by Markevitch include high-speed slitting of stainless metals for sieves and filters, remote cutting of anode and cathode battery foils, remote and gas-assisted high-speed cutting of copper (Cu) and aluminum (Al) foils, and high-aspect-ratio narrow welding for minimal distortion of thin metals.
One particular example of kilowatt-class CW single-mode laser use highlighted by Markevitch is microstructuring of cast-iron and aluminum engines in the automotive industry. Environmental regulations requiring lower energy consumption as well as reduced pollution and carbon dioxide emissions create demand for thinner, lightweight engines. A new design for motor blocks with reduced wall thickness, aided by laser materials processing, results in 1 kg weight savings per cylinder.
To achieve higher mechanical resistance and optimize heat conductivity, the cylinders are sprayed with thin plasma coatings (see Fig. 1). Prior to the application of the cladding, the cylinder surface is microstructured with grooves that have a typical feature size of 100 μm or less.
Such surface structuring has traditionally been done by mechanical or water-jet processing. These legacy technologies have various drawbacks. For example, mechanical processing is slow, can be done only perpendicular to the surface, and requires a change of tools for processing different parts and groove sizes. A water jet has very high power consumption (120 kW per nozzle) and high water consumption (contaminating water with Al), creates a sponge effect in Al, requires drying in a vacuum chamber, and can only be done on Al parts.
"A single-mode YLS-2000-SM laser with nominal power of 2 kW can treat both iron (Fe) and Al parts, is easily adaptable to treatment of parts of different diameter with grooves of different sizes down to 30 μm, and has a maximum power consumption of 5.5 kW," explains Markevitch. "Different groove angles are also possible. Both quality and throughput are much improved over traditional technologies."
Modular design
Erik Zucker, senior director of laser products and technology at Lumentum (Bloomfield, CT) describes both the modular nature and the inner workings of the company's Corelight kilowatt-class CW fiber-laser line. "Our basic building block is a double-clad fiber, single-oscillator module with over 2 kW output power," he says. "Several of these modules may be combined to provide significantly higher power from a single beam. Our fiber lasers are predominantly used for 2D sheet-metal cutting of materials ranging from mild and stainless steels to aluminum, copper, and brass. They can also be used for metal welding, brazing, and cladding applications."The 2 kW fiber-laser module is made up of a single fiber oscillator that is end-pumped by an array of Lumentum's ST Series high-brightness, fiber-coupled laser diodes, which are designed and manufactured in-house, notes Zucker (see Fig. 2).
"Each pump produces 140 W of output power from a 106-μm-diameter fiber at over 50% wall-plug efficiency," he explains. "Multiple pump fibers are fusion-combined together into a single fiber, which in turn is spliced to one end of the oscillator. Fiber Bragg gratings define the cavity and output coupler. Because the 2 kW is produced from a single module, the beam-parameter product (BPP) is very low, typically 0.8 mm-mrad. This allows a small spot diameter with large depth of field to be focused on the workpiece in metal-cutting applications, which in turn creates a very high intensity and leads to extremely efficient cutting."
Zucker notes that 25-mm-thick mild steel can be cut with the 2 kW output from Lumentum's fiber laser, whereas a 4 kW CO2 laser can only cut steel up to a 22 mm thickness. The low BPP leads to fast cutting: for example, 1-mm-thick aluminum can be cut at 75 m/min with 4 kW, while the 6 kW version cuts 1-mm-thick stainless steel at 94 m/min.
Amada (Kanagawa, Japan), a development partner and customer of Lumentum, incorporates the 2 kW laser into its cutting tools. One feature enabled in part by the low BPP of the 2 kW laser is called ENSIS, which allows on-the-fly electrical adjustment of the beam spot size on the workpiece. For automated cutting jobs, says Zucker, ENSIS can adjust from thin to thick metal cutting without operator intervention, improving productivity at job shops.
Getting the light to the workpiece
Rofin-Sinar Laser GmbH (Hamburg, Germany), which makes CW high-power fiber lasers (FL Series) ranging from 500 to 8000 W in output power, provides a number of ways to get light from the laser to the workpiece. The company's lasers can be supplied with either direct-spliced fiber of single-mode or multimode beam quality, or with a fiber-to-fiber coupler or fiber-to-fiber switches of multimode beam qualities, which allow the user to plug up to four fibers for sequential or parallel beam use, says Wolfram Rath, product manager laser sources at Rofin.
The spliced version is more compact, with a single cabinet, while the switched version has a separate enclosure for beam management. The lasers are used for cutting, welding, and surface treatment, as well as for a variety of scanner-based applications that are supported by integrated scanner processing.
The FL Series fiber lasers use a large-mode-area double-clad fiber as their active medium, says Rath. "These consist of an active single-mode core and a cladding with large diameter, in which the pump beam is conducted," he notes. "The pump light from long-life pumping modules is fed to the cladding from both sides by means of pump couplers. They are passively cooled, tolerating individual single faults, and can be exchanged in the field if necessary. The resonator mirrors are formed by inscribed fiber Bragg gratings (FBGs)."
The laser reaches an output power of 2.4 kW from a single fiber laser module, with a nominal power of 2 kW. Up to four fiber laser units can be combined by an all-fiber power combiner for a total nominal power of 8 kW, which can be delivered by up to four 100-μm-core-diameter process fibers to the processing cell.
These high-power fiber lasers are a standard tool for metal laser cutting and welding within the macro application branch, says Rath (see Fig. 3). Standard cutting systems are typically equipped with compact fiber lasers having direct process fiber of 50 μm or 100 μm core size depending on the power and sheet-thickness range of the cutting systems. "Welding of automotive parts is realized frequently within several workstations that are connected to the laser by different fiber cables that can be as long as 100 m," Rath says. "This setup helps to minimize the cycle times and optimize the laser utilization. For example, the parts are assembled and clamped in station 'A' when the laser is welding a second workpiece at station 'B.'"Because the fiber laser can be adapted to the application by choosing the fiber size, the same laser can be used for different operations. For example, manufacturing of an automotive part is done using three different laser-processing methods that are performed subsequently in three working cells: coating removal (performed using a high beam quality and integrated scanner processing), cutting of an aperture for perfect fit, and welding.
Back-reflection isolation
Kilowatt-level industrial fiber lasers that perform operations on highly reflective materials are faced with the problem of back reflection, where light reflected from the laser optics' focal region on the workpiece passes backward through the laser system. "Typical back reflections are only a fraction of the laser power because of work-piece surface irregularities, lack of precise alignment with the surface normal, and the limited collection angle of the process optics; furthermore, in many cases the back reflection has a short duration (for example, piercing)," says Jake Bell, general manager at nLIGHT (Vancouver, WA). "Nonetheless, the design of some fiber lasers renders processing of reflective materials difficult or impossible."nLIGHT produces a series of materials-processing fiber lasers with power levels ranging from 500 W to 4 kW. Among other attributes, the nLIGHT alta series has a unique configuration to minimize back reflection. "Damage caused by back reflections usually results from deposition of optical power into polymer materials, which overheat and burn," explains Bell. "The nLIGHT alta strips the back-reflected light coupled into the feeding fiber and directs it to a water-cooled beam dump where it is converted to heat without any interaction with polymers, thereby eliminating the primary damage mechanism. The polymer-free isolator is designed to dump more than 500 W continuously (see Fig. 4)."
Bell says, "We evaluated the performance of the isolation system in the case of piercing, where the highest back-reflection signals occur in laser cutting. The test successfully processed 4000 consecutive pierces of copper with no interruptions or failed pierces. In contrast to the robust, hardware-based protection provided by our back-reflection isolator, some other fiber lasers employ software protection that disables the laser in the case of a back reflection; this approach may protect the laser, but it precludes successful continuous materials processing."
The back-reflected light that is dumped in the isolator is monitored using a photodiode, says Bell. The real-time output of this sensor is provided to the user for use in process monitoring, optimization, and control (for example, pierce detection) or for tool calibration (such as beam position and focus).
Other qualities of the nLIGHT alta lasers outlined by Bell include improved cutting and welding performance, in which the lasers can deliver a modulation rate up to 100 kHz and a rise and fall time of less than 5 μs. These capabilities allow faster piercing, faster processing of fine features, and better processing quality through minimal heat affected zone, he says.
"Most multi-kilowatt fiber laser systems employ an architecture based on combining the outputs of multiple, lower-power fiber lasers, resulting in significant shortcomings in cost, performance, serviceability, upgradeability, and amenability to technological advances," he adds. "We introduce a novel kilowatt fiber-laser architecture that solves these problems by housing the pump diodes and drivers in standalone pump modules and the gain fibers in a configurable gain module that can generate more than 4 kW of output power."
These lasers, which have tailorable beam quality (BPP ≥ 1.1 mm-mrad), have been used for high-quality cutting and welding of mild steel, boron steel, stainless steel, aluminum, brass, and copper, and have also been employed in emerging applications that include additive manufacturing and surface texturing and engraving.
Quick component replacement or upgrade
As described by Frank Gaebler, marketing director for materials processing at Coherent (Santa Clara, CA), first-generation fiber lasers were based directly on telecom platforms massively scaled to higher power, using a large number of separate pump laser diodes, each independently fiber coupled and permanently spliced together.
"This brute-force approach to higher power has several limitations," he says. "In particular, all the components are permanently spliced together. If one component fails or degrades, there is no way to replace it. For example, early models were found to be susceptible to back reflections from metal processing. If the fiber splices, pump diodes, delivery fiber, or any other laser component is damaged by such back reflections, the laser had to be factory-repaired or exchanged, negatively impacting uptime and net production.
Coherent makes a second-generation kilowatt-scale fiber platform (the Highlight FL) based on a flexible modular architecture (see Fig. 5). Engineers at Coherent have used a substantially different design approach that eliminates the complexity of multiple pumps and splices, with a modular architecture that also enables simple replacement and/or upgrade of the various components, including the delivery fiber, notes Gaebler.We use fiber-coupled high-power laser-diode bars rather than multiple separate laser diodes," he says. "Their output is then coupled into the gain fiber using free-space coupling; this coupling module is also used to connect the gain fiber to the detachable delivery fiber." He adds that this approach is particularly attractive to OEM system builders, as they can buy complete lasers or separate modules depending on their level of expertise or requirements for deep integration, and they can quickly change or replace the delivery fiber to suit different applications.
In terms of specifications, at present, Coherent's Highlight FL fiber lasers are targeting steady increases in maximum power, says Gaebler: the latest model delivers 3 kW with an increase to 4 kW expected sometime in 2016. "At present, our delivery fiber modules are available with a 100 μm core, which corresponds to a BPP of around 4 mm-mrad," he says. "A 50-μm-core delivery fiber has recently become available for some models that can achieve a reduction in BPP of up to 2X. As a result of their high power and low BPP, these HighLight FL lasers are well-suited for processing metals ranging in thickness from thin foil to a few millimeters."
Early fiber lasers sometimes struggled to cut, drill, and weld certain metals, notes Gaebler. For example, fiber-laser fundamental output wavelengths are usually around 1 μm. This is a wavelength region where brass and copper exhibit very high reflectivity, as evidenced by the extensive use of copper mirrors for beam delivery of near-infrared lasers of all kinds. Retroreflections have made these metals a significant challenge for machining with first-generation fiber lasers.According to Gaebler, unlike first-generation fiber lasers, the Highlight FL laser architecture is immune to back-reflection damage for two reasons: 1) the geometry and optical properties of the dichroic beam combiner mean that any back reflections cannot reach the pump diode bar; and 2) there are no fiber splices to be damaged by any back reflections. As a result, the lasers are not limited by qualifiers that urge extreme caution with reflective metals (see Fig. 6).
Companies mentioned in this article include:
Coherent
Santa Clara, CA
www.coherent.com
IPG Photonics
Oxford, MA
www.ipgphotonics.com
Lumentum
Bloomfield, CT
www.lumentum.com
nLIGHT
Vancouver, WA
www.nlight.net
Rofin-Sinar
Hamburg, Germany
www.rofin.com
For a complete listing of companies making high-power fiber lasers, visit the Laser Focus World Buyers Guide (https://www.laserfocusworld.com/directory).
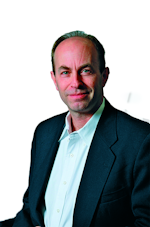
John Wallace | Senior Technical Editor (1998-2022)
John Wallace was with Laser Focus World for nearly 25 years, retiring in late June 2022. He obtained a bachelor's degree in mechanical engineering and physics at Rutgers University and a master's in optical engineering at the University of Rochester. Before becoming an editor, John worked as an engineer at RCA, Exxon, Eastman Kodak, and GCA Corporation.