Carbon dioxide lasers deliver flexibility and power
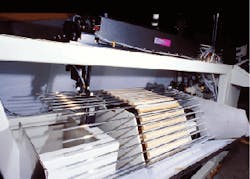
Carbon dioxide (CO2) lasers remain the most popular choice for industrial applications, because they can produce high continuous power, up to many kilowatts, with high efficiency. At the same time, their versatility has allowed them to be used for nonindustrial applications in research, where their mid-infrared (IR) wavelengths are useful, and in medical surgery. In recent years, this mature technology has benefited from new designs that lead to more compact lasers with greater output power per unit volume.
Principles of operation
Carbon dioxide lasers rely on transitions between the vibrational modes of the simple CO2 molecule (see Fig. 1). The upper laser level is the n3 asymmetric stretching mode, which drops into either the n1 stretching mode or the n2 bending mode with transitions at 10.6 and 9.6 µm, respectively. Simultaneous rotational transitions create large families of laser lines, so that CO2 lasers can either lase in narrow lines or effectively across a broad band.Excitation energy is supplied by an electric discharge, but adequate efficiency requires the mixing of CO2 with nitrogen (N2) and helium (He). Nitrogen captures the energy from the discharge and transfers it collisionally to the CO2 molecules, whose n3 state is close to the same energy as the first vibrational state of n2. Helium atoms, in turn, interact with CO2 to efficiently depopulate the lower lasing levels and also enhance the conduction of heat out of the gas mixture. Overall efficiency of CO2 lasers ranges from about 5% to 20%, and output power, depending on the design, can be as low as hundreds of milliwatts or as high as hundreds of kilowatts.
Main laser types
While all CO2 lasers work on the same principles, a large part of the versatility of such lasers stems from the existence of several distinct designs, which vary in how they use the working gas and how they remove waste heat (see Fig. 2). The simplest design is the sealed-tube CO2 laser, which has a glass tube filled with the CO2-N2-He mixture. Mirrors at each end form a resonant cavity. Because an electrical discharge quickly breaks down CO2, generally in a few minutes, hydrogen or water vapor is added to react with the carbon monoxide and oxygen to reform the CO2. A nickel cathode heated to 300°C can also catalyze the recombination reaction. Either procedure increases operating life to several thousand hours.Initial versions of sealed-tube lasers used a direct-current electrical discharge running along the length of the tube, which produces an output proportional to tube length—about 40-50 W/m. More-recent designs use an RF discharge perpendicular to the tube length. In particular, the development of much-higher-power sealed-tube lasers based on slab technology is increasing the application range of this type.
If the sealed tube is replaced by a waveguide, with an inner diameter of a few millimeters, we have the second major type—a waveguide laser. The waveguide laser has less lasing volume and thus a smaller power output, generally less than 50 W, but has a high-quality beam and can be easily tuned to any discrete CO2 line. Its compact size allows it to compete for some applications with HeNe lasers, but it is far more powerful, generating watts rather than milliwatts of output.
The power output of a sealed-tube laser is limited by the need to conduct heat out of the lasing gas. To increase the power, other designs use flowing gas, so that the heat can be removed by convection rather than conduction and thus at much higher rates. In slow-flowing gas lasers, gas at low pressure flows along the axis of the lasing tube producing around 80–100 W/m. In some designs, several tubes can be combined in a single coolant jacket.
Increasing the speed of the gas produces a fast-axial-flow laser, with a heat exchanger cooling the gas as it exits the tube. The gas is then recirculated with a small amount replaced with new gas each cycle. Multiple parallel tubes are connected in series optically with mirrors producing about 1 kW of output for every four to eight tubes (see Fig. 3). Such lasers generally produce up to 5 kW of power.All these types of lasers typically operate in continuous mode. For these lasers, discharge instabilities limit the internal gas pressure to about 100 Torr. For pulsed operation with pulses lasting from tens of nanoseconds to microseconds, much higher pressure, near or above atmospheric pressure, are allowed. Of course, higher pressures with more gas per volume increase the energy density available to the laser pulse. Lasers built in this way are termed transversely excited atmospheric lasers, or TEA lasers, with "atmospheric" referring to the internal pressure, not the composition of gases.
Given this higher pressure, TEA lasers can be built similarly to the other types with sealed tubes or slow, fast-axial, or transverse gas flow. The electric discharge is, however, always perpendicular to the beam axis. Because high pressure broadens the emission lines, modelocking can be used to produce nanosecond pulses. In addition, at pressures near 10 atm, line broadening allows nearly continuous tuning across a broad wavelength band, an advantage for many research and sensing applications.
New designs
Probably the most important recent development in CO2 laser design has been the perfection of slab-discharge sealed-tube lasers by Coherent Inc. (Santa Clara, CA). The basic innovation is to substitute rectangular or slab electrodes for the narrow electrodes conventionally used (see Fig. 5 on p. 137). While there is only a 2-mm gap between the electrodes, ensuring efficient gas cooling, the plates are quite wide, so that output scales according to electrode area (1 W/cm2), not tube length. For example, to obtain 500-W output, a power reached in 1996, an electrode need measure only 5 cm wide by 1 m long, while a conventional sealed-tube laser would have to be 10 m long. The technology was first introduced in the early 1990s and is continuing to expand into higher and higher power ranges, recently breaking the 1-kW mark.In slab-discharge lasers the lasing cavity is not the same shape as the output beam, so optical means are needed to spread the lasing action over the entire volume but still obtain a tight output beam. This is done by using two totally reflecting spherical mirrors of different radii at the two ends of the optical cavity. The mirror on the output end does not cover a small segment of that end, allowing the exit of a narrow beam.
The search for higher powers and more-compact lasers has led some researchers to experiment with novel gas-flow regimes. In research at the Samara Railway Engineering University (Samara, Russia), V. T. Volov has demonstrated very high power densities by introducing the gas at a high-speed vortex within the lasing cavity. The natural turbulence generated by the vortical flow and the lower pressure near the axis combine to yield high heat-transfer rates. Volov has demonstrated electrical power coupled into the discharge at rates as high as 300 W/cm2 without overheating.
Cutting metal and lifting cells
The most common applications for CO2 lasers are in manufacturing, where their high continuous output is ideal for cutting and welding. Although some metals reflect 90% of radiation at 10 µm, plastics, ceramics, cloth, and rubber absorb well at this wavelength. In addition, titanium, a tough metal to cut mechanically, absorbs strongly at 10 µm, so CO2 lasers are particularly useful for this material. Lasers have considerable advantages over mechanical means for cutting—with spot sizes as small as 50 µm, intricate patterns can be cut under the control of a small computer, so that prototypes can be easily created and modified.
Another major high-power application is heat treatment, where the laser beam is optically spread over a large area to rapidly change the crystalline structure of a product`s surface, increasing durability and strength. The very-high-power pulses possible with TEA lasers can also be used for thermally stripping paint off surfaces. Such lasers can deliver 8-J pulses at repetition rates of up to a couple of hundred hertz.
At lower powers, around 100 W, sealed-tube lasers have increasingly taken over product marking from ink-jet systems. Laser marks are more permanent, and lasers require less maintenance than ink-jet printers, which are prone to clogging.
Another application of CO2 lasers is in remote sensing, where their long wavelength and tunability make them ideal for detection of a vast range of molecules. Most molecules exhibit their characteristic rotational-vibrational IR absorption spectra in the same 10-µm range that CO2 lasers emit. By irradiating sections of the atmosphere, for example, and tuning the laser across an IR band, remote IR spectra can be obtained, revealing low levels of airborne gas and pollutants.
The sensitivity of CO2 laser spectroscopic systems is continuously improving. In recent research, detection levels in laboratory gas samples of a few parts per trillion have been achieved using the photoacoustic effect. In these experiments, energy absorbed from a pulse of laser radiation is converted by the trace gases into a tiny pulse of pressure that can be picked up by a sensitive microphone.
The remote-sensing capabilities are not limited to gases. A team of scientists working at the Commonwealth Scientific and Industrial Research Organization (Sydney, Australia) used an airborne tunable CO2 laser to map different mineral types on Earth. By switching among 100 wavelengths every 2 ms, sufficiently detailed reflection spectra were obtained to distinguish between silicon and carbonate minerals.
In medicine, high-power CO2 lasers have long been used in surgery, where the continuous beam cauterizes as it cuts. However, low-power lasers are finding uses in medical research as well, based on their ability to concentrate heat in a tiny area. For example, researchers at the National Cancer Institute (Bethesda, MD) have used a pulse from a CO2 laser to select specific human cells from a complex tissue slice. Under a microscope, a layer of heat-sensitive adhesive material is laid over the tissue sample, and researchers mark the cells to be selected. The laser irradiates the film over the selected cells, activating the adhesive, and the cells are lifted onto another slide.
FURTHER READING
Laser Focus World 32(7), 22 (July 1996).
K. Bondelie, Laser Focus World 32(8), 95 (August 1996).
M. R. Emmert-Buck et al., Science 274, 998 (8 Nov. 1996).
P. Repond and M. W. Sigrist, Appl. Opt. 35, 4065 (July 1996).
V. T. Volov, SPIE Vol. 2907, 256 (Feb. 1996).
About the Author
Eric J. Lerner
Contributing Editor, Laser Focus World
Eric J. Lerner is a contributing editor for Laser Focus World.