PHOTONIC FRONTIERS: HIGH-POWER LASER DIODES: Bringing high brightness to high-power laser diodes
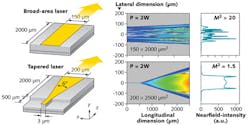
Laser diodes excel at converting electric power into light, with efficiency reaching 70%. However, increasing the power generally comes at a cost in beam quality. Wide-area laser diodes emitting watt-class powers in multimode beams can’t match the beam quality of narrow-stripe diodes that emit much lower power in a single transverse mode. Stacks of diode arrays can generate kilowatt-class power, but their beam quality is even worse, limiting them to applications that don’t require high brightness, such as heat treating and pumping bulk solid-state lasers.
Now developers are pushing to improve beam quality so they can put the high efficiency of diodes to work in high-power applications such as cutting and welding metal sheets, which require high-brightness beams.
Divergence, beam quality, and brightness
Laser diodes are well known for their large beam divergence, but that reflects the diffraction limit of the small emitting aperture. Beam quality depends not on the amount of divergence but on how it compares to the diffraction limit set by the laser’s output aperture. A narrow-stripe laser diode oscillating in a single lateral (or transverse) mode has good beam quality despite the large divergence caused by its tiny emission area, and that broadly diverging beam can be focused tightly. A diode stack emitting from a much larger aperture may have lower divergence, but its beam quality is much worse.
One measure of beam quality is the beam parameter product (BPP, sometimes designated Q), which is the product of beam diameter at the beam waist times the far-field beam divergence. Another is the brightness B, which is the power per unit area divided by the solid angle of the beam divergence—watts per square centimeter per steradian. Brightness is given by dividing the power P by π2 times the square of the beam parameter product Q:
(A different formula is needed for astigmatic beams.) Higher brightness means better beam quality.
Another widely used measure of beam quality is M2, which equals the measured BPP divided by the BPP for an ideal Gaussian beam. The result is a normalized value, with 1.0 indicating an ideal Gaussian beam and higher numbers denoting poorer-quality beams.
Single-emitter laser diodes
Brightness depends on power, and the power available from a laser diode stripe is limited by its volume and internal power density. As power density increases, lasers become vulnerable to internal and facet damage, and resistive heating reduces their power-conversion efficiency.
Broad-stripe lasers increase power by increasing the volume of the waveguide in the active layer, but broad-area lasers tend to multimode operation, degrading beam quality. Diodes with stripes around 100 µm wide and several millimeters long can emit more than 10 W, but beam quality is limited. Researchers have found that beam quality can be improved by tapering the width of the laser stripe, as shown in Fig. 1.
Recent experiments by m2k Laser (Freiburg, Germany) and DILAS (Mainz, Germany) showed striking differences in brightness of 5-mm-long broad-area and tapered InGaAs lasers emitting at 976 nm. A laser with a uniform 90 µm stripe emitted 10 W with slope efficiency of 1.1 W/A and peak electrical-to-optical efficiency of 65%. A similar laser with a 4° taper generated 10 W with peak efficiency of 56%, reflecting a lower 1.05 W/A slope efficiency. The big advantage of the tapered laser was brightness reaching 600 mm-mrad, six times higher than the wide-stripe laser.1 Unfortunately, the authors told Photonics West 2010 attendees, “packaging of tapered-lasers is a very challenging task and the existing astigmatism in tapered lasers also makes optics design for modules more complex.”
Diode arrays and beam combination
Although the output of individual laser diodes is limited, many laser diodes can be fabricated on a single substrate, and their output can be combined to generate much higher powers. At Princeton Optronics (Mercerville, NJ), dense arrays of VCSELs have produced powers exceeding 200 W.2 Stacks of many bars, each containing many edge-emitting laser stripes, can generate a couple of kilowatts but produce a poor-quality beam. No simple combination of mirrors and lenses can add two beams together to produce a beam with higher brightness, says John Marsh of the University of Glasgow. Instead, the combination increases the illuminated area or loses light.
Producing brighter and higher-quality beams requires more elaborate beam-combination methods. One is coherent combination, which matches the phases of the incoming beams so they add constructively. The other is spectral beam combination, which adds together beams of different wavelengths, like wavelength-division multiplexing in an optical fiber. Both have been studied for fiber lasers as well as for diode arrays.
Coherent beam combination
For diode arrays, the major challenge in coherent beam combination is to maintain coherence among the laser stripes. It might seem straightforward to fabricate stripes so close that evanescent coupling of adjacent stripes creates a single coherent “supermode.” Unfortunately, Marsh wrote in a review article, “that behavior is not stable, with the most stable supermode being that in which adjacent elements are 180 degrees out of phase,” producing undesirable dual lobes in the combined beam.3
An alternative is to drive several parallel diode amplifiers with the output of a single master oscillator, then recombine the beams to keep them in phase. A variety of configurations have been tried, but effective coherent beam combination has proved difficult with simple optical systems because it requires very stringent control of the optics.4
Recently, MIT Lincoln Labs (Lexington, MA) has shown that an active electronic control system can greatly improve beam combination in a master oscillator/power amplifier configuration. As shown in Fig. 2, they start with a single narrow-line master oscillator laser and direct its output through a diffractive optical element, which splits it into many separate elements. The output is passed through optical isolators, then each element is focused onto one of 21 slab-coupled optical waveguide semiconductor amplifiers (SCOWAs). The input light makes a double pass through the amplifiers, then is directed to a measurement system, with part split to a feedback loop.Separate current drivers for each waveguide amplifier receive feedback, which they use to adjust the phase of the amplified light to maintain coherence of all the amplifier outputs. Lincoln first used this approach for a single 21-element linear array. When they divided the master oscillator output between two 21-element amplifier arrays, they produced a combined output of 8.2 W. With eleven 21-element arrays, their continuous-wave output totaled 38.5 W, which they called “the highest power of actively coherently combined diodes with high coherence contrast.”5 It’s an approach Marsh calls “very interesting.”
Spectral beam combination
So far, spectral beam combination has proved easier than coherent beam combination. Total power and brightness scale with the number of wavelengths added to the beam. The big advantage comes from the ease of manipulating light by its wavelength. As shown in Fig. 3a, a diffraction grating or other dispersive optic can direct light from separate sources emitting at different wavelengths into a single waveguide or fiber. Similarly, optical filters can drop single wavelengths into an optical fiber.Spectral beam combination has its own limitations. One is the need for broad bandwidth in the optical system or transmission medium, although that requirement is not as stringent as it would be if the signal had to be amplified. It also needs laser sources spaced across a suitable range of wavelengths. And the resulting broadband signal is not suitable for applications that require monochromatic light, such as holography.
However, the reported results can be impressive. At the SPIE Defense, Security + Sensing meeting in April 2011, Robin Huang and colleagues at TeraDiode (Littleton, MA) reported that spectral combining of beams from commercial diode arrays could deliver a total of 1040 W through a 200-µm core fiber, as shown in Fig. 3b with beam parameter product of 18 mm-mrad, which they said was the lowest reported for a kilowatt-class direct-diode source. The published paper does not detail the system’s optical configuration, but it does say the source could cut 6.65-mm steel sheets.6
Outlook
Such laboratory demonstrations are welcome news. Combining high brightness with high power would be a big boost for direct-diode applications. Bright high-power diodes would do more than replace less efficient laser sources; they also would make new laser applications practical, and make some small contribution to improving overall energy efficiency.
The challenge now is to translate those impressive laboratory tests into practical technology.
REFERENCES
1. J. Gilly et al., “Comparison of concepts for high-brightness diode lasers at 976nm,” High-Power Diode Laser Technology and Applications VIII, Proc. SPIE, M.S. Zediker, ed., 7583, 75830S-1 (2010); doi:10.1117/12.840698.
2. J.-F. Seurin et al., “High-power high-efficiency 2D VCSEL arrays,” Vertical-Cavity Surface-Emitting Lasers XII, Proc. SPIE, C. Lei, J.K. Guenter, eds., 6908, 690808, (2008); doi:10.1117/12.774126.
3. J.H. Marsh, “Emerging technologies for high-power diode lasers,” IEEE Photon. Soc. Newsletter, 4 (December 2010).
4. T.Y. Fan, “Laser beam combining for high-power, high-radiance sources,” IEEE J. Selected Topics in Quant. Electron. V, 11, 567 (May/June 2005).
5. S.M. Redmond et al., “Active coherent beam combining of diode lasers,” Opt. Lett., 36 999–1001 (Mar. 15, 2011).
6. R.S. Huang, B. Chann, and J.D. Glenn, “Ultra-high brightness, wavelength-stabilized, kW-class fiber coupled diode laser,” Proc. SPIE, 8039, 80390N (2011); doi:10.1117/12.887332.
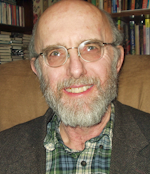
Jeff Hecht | Contributing Editor
Jeff Hecht is a regular contributing editor to Laser Focus World and has been covering the laser industry for 35 years. A prolific book author, Jeff's published works include “Understanding Fiber Optics,” “Understanding Lasers,” “The Laser Guidebook,” and “Beam Weapons: The Next Arms Race.” He also has written books on the histories of lasers and fiber optics, including “City of Light: The Story of Fiber Optics,” and “Beam: The Race to Make the Laser.” Find out more at jeffhecht.com.