Laser Materials Processing: Pulsed CO2 laser increases ablation rates for improved glass processing
Pulsed and powerful
Compared to conventional CO2 lasers, Fraunhofer ILT uses a 200 W average power, 40 kW peak power, m2 = 1.33, Q-switched pulsed CO2 laser with a pulse duration ≥250 ns and maximum repetition rate of 150 kHz. Because of the use of two acousto-optic modulators, laser radiation can be delivered in two modes: a Q-switched pulse (mode 1) for ablation and a modulated pulse (mode 2) for final surface correction (see figure).
Using a scanning strategy that delivers pulse power Pavg with duration tpulse and repetition rate frep with focus diameter ds across the bulk glass material at speed vs and pulse distance dx, an ablation depth of zabis achieved using mode 1 operation. Experimental calculations demonstrate material removal rates of 2.35 mm3/s, allowing fabrication of rough glass optics such as a honeycomb structure (for weight reduction) on fused silica or even freeform optics. White-light interferometry measurements of the initially ablated optical surfaces allow optimization of repetition rates and fluence values of the laser to maximize material removal.
The high roughness after the ablation process is reduced in a second laser-based process step. Using continuous-wave CO2 laser radiation, the surface is smoothed by a remelting process and the micro roughness can be reduced to <0.1 nm (see http://dx.doi.org/10.2351/1.4974905).
For the reduction of residual waviness, a third process for correction polishing is necessary using rectangular pulses and only 50 W power levels. This process limits ablation to lower material removal rates, allowing selective figuring of the glass surface in a final error-correction step called Laser Beam Figuring. By controlling the pulse duration of each laser pulse, glass material can be ablated selectively with ablation depths down to 3 nm. The lateral resolution of the ablation process is 100 μm and the vertical resolution is approximately 3 nm.
"The laser-based process chain enables the fabrication of complex-shaped optics made of fused silica with only one laser source," says Christian Weingarten at Fraunhofer ILT. "The surface quality of the fabricated optics is already sufficient for illuminating optics, but with the development of the laser-based correction polishing process, we will fabricate even higher quality illumination optics in the future."
REFERENCE
1. C. Weingarten et al., Appl. Opt., 56, 4, 777–783 (2017).
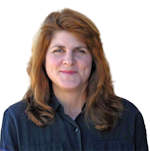
Gail Overton | Senior Editor (2004-2020)
Gail has more than 30 years of engineering, marketing, product management, and editorial experience in the photonics and optical communications industry. Before joining the staff at Laser Focus World in 2004, she held many product management and product marketing roles in the fiber-optics industry, most notably at Hughes (El Segundo, CA), GTE Labs (Waltham, MA), Corning (Corning, NY), Photon Kinetics (Beaverton, OR), and Newport Corporation (Irvine, CA). During her marketing career, Gail published articles in WDM Solutions and Sensors magazine and traveled internationally to conduct product and sales training. Gail received her BS degree in physics, with an emphasis in optics, from San Diego State University in San Diego, CA in May 1986.