The biggest project in the US Department of Energy’s first round of Advanced Research Projects Agency energy (ARPA-E) grants announced three years ago could pay off in a big way for the laser industry. Foro Energy (Littleton, CO and Houston, TX) has demonstrated that 20 kW of laser power delivered through a special optical fiber can drill through hard rock. “We have completed proof-of-concept testing, and are now developing field-deployable hardware,” says Foro chief technical officer Mark Zediker. He foresees applications in geothermal energy and production of oil and natural gas.
Mechanical drilling has been the standard in oil and gas production for more than a century. However, penetrating the hardest rocks, such as granite and basalt, requires applying tens of tons of weight to press down on the drill, and wears out the bits quickly. That can make drilling uneconomical for many potential geothermal energy sites, or for oil and gas fields capped by hard rock.
In 2009, ARPA-E gave Foro a $9.14 million grant to develop a “low-contact” drilling technology to aid development of geothermal energy, which often must be extracted from very hard volcanic rocks. The agency’s goal was to reduce drilling costs by up to a factor of 10, helping to make carbon-free geothermal energy competitive with fossil-fuel energy generation. With private funding, Foro is studying the same technology for oil and gas production.
The Foro process delivers the high-power laser beam to the rock surface, rapidly heating it to hundreds of degrees Celsius. The laser power is integrated with a mechanical drilling bit. The thermal shock “spalls” and softens the rock a couple of millimeters into the surface, then the mechanical drill clears it away.
This hybrid laser-mechanical process dramatically reduces energy requirements. Big drill rigs require about 2000 HP, equivalent to 1.5 MW. Powering a 20 kW fiber laser takes only 100 kW of power, and the drill needed to remove the softened rock requires only 10 HP, or 7.5 kW.
Proposals for laser drilling for petroleum go back almost five decades, but suitable high-power lasers and other technologies were lacking. The most powerful laser on the market in 1980 was a room-sized 10 kW carbon dioxide laser that included a wind tunnel. Military research lasers reached a megawatt, but were budget-busting behemoths that ran for only brief intervals. What helped to make Foro’s system commercially feasible was the development of high-power fiber lasers like the 20 kW fiber laser they bought from IPG Photonics (Oxford, MA). “The commercial viability of the program was substantially improved by those lasers,” says Zediker.
Another key enabling technology is the special optical fiber Foro developed to carry power from the laser sitting at the surface down at least 4 km into the ground. Transporting up to 20 kW over such long distances required reducing the stimulated Brillouin scattering that limits power transmission in conventional fibers. The company isn’t describing its exact recipe, as it is the subject of several pending patent applications, but Zediker says it involves increasing core size, using multimode transmission, avoiding core polarization, using an incoherent multimode laser source, and varying temperature and mechanical stresses along the length of the fiber.
The fiber cable is threaded through the drill rig and protected by a metal sheath, like those used on fiber sensors in oil and gas wells. A gel surrounds the fiber inside a 0.125 in. metal sheath; the cable has been tested to temperatures of 200°C and the pressures expected at depths to 4 km. Fiber attenuation is close to the Rayleigh scattering limit at the 1070 nm wavelength of the fiber laser, or about 0.7 dB/km, corresponding to 3 dB attenuation in a 4 km fiber. They have transmitted more than 20 kW through a 1.5 km length.
Another important innovation is a fiber connector built to withstand the high temperature and pressure in a deep well—without requiring the flowing-water cooling normally needed at 20 kW power levels, which is impractical at the bottom of a well. The output port is mounted within the drill bit so the laser light heats the rock just beneath the drill. The down-hole end also includes an optical slip ring that also has been tested at 20 kW. That flexibility is important for future applications, such as use in directional drilling, in which the drill turns underground to drill outward from the main borehole.
100 kW soon
Foro already has secured over 3800 pending US and foreign patent claims. Near-term plans include testing the system at higher powers. Moving from the laboratory to the real world is challenging, but Foro has attracted serious interest from drilling companies interested in working with them, including the Brazilian oil company Petrobras (Rio de Janeiro, Brazil).
Commercial success could bring major new geothermal resources on-line, reducing carbon emissions and energy costs. It also could open previously inaccessible oil and gas reserves. And Zediker predicts that laser drilling “will create a strong market pull for laser powers of 20 kW and higher, the first truly commercial application of very high laser power.”
Foro is studying other ways to combine its fiber-optic beam-delivery technology with mechanical tools to make the extraction of natural resources faster, safer, cheaper, and more effective. The oil, gas, geothermal, and mining industries spend more than $100 billion annually on resource extraction, so it’s a big market with lots of opportunities.
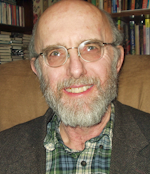
Jeff Hecht | Contributing Editor
Jeff Hecht is a regular contributing editor to Laser Focus World and has been covering the laser industry for 35 years. A prolific book author, Jeff's published works include “Understanding Fiber Optics,” “Understanding Lasers,” “The Laser Guidebook,” and “Beam Weapons: The Next Arms Race.” He also has written books on the histories of lasers and fiber optics, including “City of Light: The Story of Fiber Optics,” and “Beam: The Race to Make the Laser.” Find out more at jeffhecht.com.