Photonic Frontiers: Laser Space Instrumentation: Laser instruments earn their place in space for communications and lidar
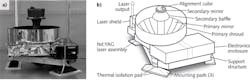
Lasers were born early in the space race, but the first successful space applications were based on the ground. Flashlamp-pumped solid-state lasers measured distance to the moon in 1962 and to satellites in 1964, but they had to be big and cumbersome to deliver the power needed for ranging. Gemini 7 astronauts tested a diode laser for communications in 1965, but clouds kept them from establishing a link to the ground receiver.
By 1971, a lamp-pumped 0.05 Hertz Q-switched ruby laser altimeter on the Apollo 15 Lunar Orbiter was mapping part of the lunar surface. However, neither lamp-pumped solid-state lasers nor gas lasers were suitable for long-term operation in space. Long-term robotic laser instruments became practical only with the development of diode-pumped solid-state lasers.
Lasers to Mars
The first high-profile space mission to carry a diode-pumped laser was the ill-fated Mars Observer. Launched in September 1992 carrying the Mars Orbiter Laser Altimeter, it was lost on August 21, 1993, three days before it was to enter Mars orbit. Smaller laser altimeters later mapped the Moon and the near-earth asteroid Eros.
A new Mars Orbiter Laser Altimeter, shown in Figure 1, was built for a smaller follow-on Mars mission, the Mars Global Surveyor, launched in November 1996. That mission was a brilliant success. From March 1998 until June 2001, the laser altimeter mapped elevations on Mars to within about 30 cm from pole to pole, producing the most accurate global topographic map of any planet in the solar system. The diode-pumped, Q-switched neodymium-YAG laser fired ten 48 mJ pulses/s, each lasting 8 ns.1 All told, it fired a total of some 670 million shots. That data is still paying dividends and is cited in a new report suggesting Mars once had glaciers.2
On January 12, 2003, NASA launched the first satellite-borne lidar for continuous global observations of Earth, the Geoscience Laser Altimeter System, on ICESat-1, to study changes in the Greenland and Antarctic ice sheets. It carried three 1064 nm Nd-YAG lasers that were each supposed to operate continuously for 18 months, initially firing 70 mJ pulses. However, the first laser failed in just 37 days, and output of the second dropped quickly, so NASA shifted to a series of short campaigns, allowing observations to continue until the last laser failed in October 2009.3 The altimeter achieved vertical resolution approaching 3 cm, vital for monitoring changes in the ice sheets, and also collected data on forest heights around the world.
Future NASA plans for terrestrial systems include the Lidar Surface Topography mission, recommended in 2007 by the National Research Council. Goals include a global topographic survey with 5 m resolution horizontally and 0.1 m vertically to map landslide and flood hazards for local planning. It could also record land topography and canopy structure simultaneously (see issue cover).
NASA modified the master-oscillator power amplifier (MOPA) design of the ICESat-1 laser for the MESSENGER mission to Mercury. Launched in August 2004, the probe reached Mercury orbit in March 2011, and as of this writing the laser altimeter is still collecting data on the planet's surface.4
Laser communications
Diode pumping also revived interest in high-speed laser links to deep space, where the limited speed of radio links had created a data bottleneck. After NASA's plans to launch a 5 W, 100 Mbit/s laser relay called the Mars Telecommunications Orbiter in 2009 was cut in the 2005 budget, focus was shifted to a simpler test called the Lunar Laser Communication Demonstration (LLCD).5The LLCD transmitter was based on commercial telecommunication parts, including a distributed-feedback diode laser, erbium-fiber amplifiers, and a modulator, to avoid the high cost of lasers customized for space, says Donald Cornwell, director of NASA's optical communications division (Washington, DC). Designed, built and operated by the MIT Lincoln Laboratory (Lexington, MA), the transmitter emitted 0.5 W at 1550 nm through a 10 cm telescope. A 16-ary pulse-position modulation encoded four data bits in pulse, to carry 622 Mbit/s from the Lunar Atmosphere and Dust Environment Explorer (LADEE) (see Fig. 2) in lunar orbit. To maximize sensitivity, the ground receiver used superconducting nanowire detector arrays operating at 1 to 3 K. A single 1550 nm photon can heat the 4 nm wire enough to stop superconductivity, says Cornwell. "It's amazingly sensitive, with detection efficiency of 70 to 80%," he adds.6
In October 2013, LLCD successfully demonstrated 622 Mbit/s downloads, six times the fastest radio link from the Moon, with a transmitter only half as massive. "We did all the demos we needed in the first three days, and for the rest of the time we just operated with it," says Cornwell. "We could operate the laser system to within three degrees of the sun, the same as with a radio link." A ground-based laser uploaded data at up to 20 Mbit/s, 5000 times faster than the best radio. "This demonstrates that this technology could serve as the primary communications system for future missions," he adds.
NASA's next laser test will relay data at gigabit rates between a pair of ground stations. Both up- and down-laser links in the Laser Communications Relay Demonstration (LCRD) will be in the 1550-nm band, with a pair linking each ground station with a transceiver on a geosynchronous communications satellite. Initial plans called for a two-year test, but NASA is considering up to five years after a 2018 launch.7
Beyond that, NASA will turn to putting a 25 kg laser into Mars orbit, using laser technology similar to LLCD, but with a larger 22 cm telescope and more advanced electronics. The uplink will be at 1 micron to provide the few hundred watts needed to serve as a pointing beacon. A downlink to the 5 m Palomar telescope could deliver over 100 Mbit/s from Martian probes when the planet is within 60 million km, and over 250 Mbit/s when Mars is within 30 million km. Cornwell says that has already been approved, adding that the Jet Propulsion Laboratory is studying a 5 kg laser link that could send 200 kbits/s direct from the Mars 2020 Rover to terrestrial receivers.
Lasers on Mars
Since August 2012, the Curiosity rover has been probing Martian rocks and soils with 30 mJ laser pulses lasting 5 ns focused onto a submm spot by an instrument called ChemCam (see Fig. 3).8 It uses a neodymium-doped rod of potassium-gadolinium tungstate [Nd:KGd(WO4)2 or Nd:KGW] because of its wide temperature range. The laser pulses ablate material from the surface and perform laser-induced breakdown spectroscopy (LIBS) on spots up to 7 m away."Typically we fire 30 shots for each location," says Roger Wiens of the Los Alamos National Laboratory (NM), ChemCam's principal investigator. Shock waves from the first few shots blow away Martian dust to expose bare rock. Then the laser ablates the exposed rock, and a spectrometer measures emission from the hot plasma to identify the elements present. "If weathering has left a gradient in composition near the surface, multiple laser shots can detect and measure the gradient in the rock," says Wiens.
An early finding made headlines when Curiosity discovered rocks that were formed at the bottom of a freshwater lake. Wiens says that it was "an environment we would consider habitable," although the rocks showed no direct evidence of life. The ChemCam instrument has fired nearly 200,000 shots (see Fig. 4) as of late September, and is operating almost every other day.Recently Wiens has begun splitting his time between ChemCam and the development of a new laser sampling system called SuperCam, chosen in July 2014 to fly on the Mars 2020 rover.
SuperCam will use Nd-YAG because the team has decided the extra thermal range provided by KGW is not needed. To collect more mineralogical data, it will adapt ChemCam technology to perform Raman spectroscopy as well as LIBS. "We take the laser beam used for LIBS, dial down the power, double the frequency, and with a few more tweaks you can do Raman spectroscopy out to about 12 meters," says Wiens. Adding that capability at modest cost will help meet the ambitious goals of Mars 2020, such as identifying the most interesting rocks to sample and cache in canisters for a future sample return mission.
Tough challenges
Space applications pose special challenges, including extremely reliable operation in extreme environments, and building laser systems to meet those demands is a challenge. NASA ran into problems when unexpectedly short lifetimes of the lasers on ICESat-1 led it to select a different architecture for the Advanced Topographic Laser Altimeter System (ATLAS), the replacement laser instrument on ICESat-2.
NASA's new design calls for a frequency-doubled Nd-vanadate (Nd-YVO4) MOPA that will fire 250 to 900 µJ pulses lasting 1.5 ns at a 10 kHz rate. The 532 nm output will be split into six beams, arranged in three pairs, and rated for a total lifetime of a trillion pulses.9 Originally planned for a 2016 launch, the spacecraft has run into problems with the laser and with photon-counting detection system needed to detect returns from the lower-energy pulses. Costs are up; the launch is likely to slip until 2017 or 2018.10
However, the payoffs from laser space instruments can justify the extra cost and effort. Often no other technology can meet demanding requirements such as high-speed data transmission from deep space or mapping changes in the Greenland ice sheet to provide invaluable ground truth on climate change.
References
1. D. E. Smith et al., J. Geophys. Res. 106, p. 23,689 (Oct 25, 2001).
2. S. Cull et al., Geology: 2014; doi:10.1130/G36152.1.
3. W. Abdalati et al., Proc. IEEE 98, 5, (May 2010); doi:10.1109/JPROC.2009.2034765.
4. A. W. Yu et al., Proc. SPIE 8959, 8590H (2014); doi: 10.1117/12.2041452.
5. S. Townes et al., 2004 IEEE Aerospace Conf., posted at http://trs-new.jpl.nasa.gov/dspace/bitstream/2014/38024/1/04-0216.pdf.
6. D. M. Boroson et al., Proc. SPIE 8246, (2012); doi:10.1117/12.914801.
7. J. D. Moores and K. E. Wilson, Proc. SPIE 8610, 86100L (2013); doi:10.1117/12.2010817.
8. CHEMCAM LINK; http://www.msl-chemcam.com/index.php.
9. N. Sawruk et al., Proc. SPIE 8599, 85990O (2013); doi:10.1117/12.2005590.
10. S. Clark, "ICESat 2 mission facing $200 million budget overrun," Spaceflight Now (June 1, 2014); http://www.spaceflightnow.com/news/n1406/01icesat2/.
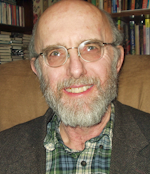
Jeff Hecht | Contributing Editor
Jeff Hecht is a regular contributing editor to Laser Focus World and has been covering the laser industry for 35 years. A prolific book author, Jeff's published works include “Understanding Fiber Optics,” “Understanding Lasers,” “The Laser Guidebook,” and “Beam Weapons: The Next Arms Race.” He also has written books on the histories of lasers and fiber optics, including “City of Light: The Story of Fiber Optics,” and “Beam: The Race to Make the Laser.” Find out more at jeffhecht.com.