PHOTONIC FRONTIERS: WHITE-LIGHT LEDS: White-light LEDs promise a bright future for solid-state illumination
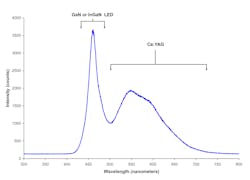
White-light emitting diodes (LEDs) already are standard in products from pocket flashlights to solar-powered night lights on suburban lawns. The office of Energy Efficiency and Renewable Energy at the US Department of Energy (DoE) heralds white-light LEDs as the "great white hope" for general illumination because they promise to bring down power consumption by improving efficiency well beyond today's fluorescent lamps. Progress is evident in steady improvements in efficiency measured in lumens output per watt of input power, and in the appearance of the first household solid-state lighting in stores. Yet formidable obstacles remain before solid-state lighting becomes the norm for homes and businesses. Costs need to come down so white-light LEDs make economic sense. Color balance needs to be improved for many applications. And tough technical challenges remain, particularly in reducing the decline in efficiency that now comes with higher drive currents.
How white are white-light LEDs?
The term "white-light LED" is in some ways a misnomer because LED emission comes from an electron recombining with a hole in a semiconductor, which releases a photon with energy equal to the gap between the valence and conduction bands. In practice, this spans a range of tens of nanometers, so the eye sees their emission as colored instead of white.
There are two ways to make LED emission look white to the eye. The simplest is to use a short-wavelength LED to excite one or more phosphors that emit at longer wavelengths and combine their outputs (see Fig. 1a). Alternatively, multiple LEDs emitting in different visible bands can be combined (see Fig. 1b). Both methods have advantages and disadvantages.Phosphor-based systems can be cheap and simple because they need only a single emitter. Combining a blue indium gallium nitride (InGaN) emitter with a single yellow phosphor produces whitish light with a high color temperature, around 6000 K. Adding a red phosphor can shift the color balance to the lower color temperatures (around 3000 K) often preferred for indoor illumination. However, the down-conversion of light by phosphors reduces energy efficiency, and converting from blue to red costs more energy than using only a yellow phosphor.
Using three or four separate LEDs spread across the visible spectrum promises higher efficiency because no energy is lost in stimulating phosphors. Careful choice of LED wavelengths and adjustment of relative power levels offers better color balance and adjustment of the balance to match customer preferences. However, the use of multiple LEDs increases component numbers and costs and green LEDs, like green diode lasers, don't match the performance of their blue and red counterparts.
So far, blue LEDs combined with yellow phosphors have succeeded in flashlights and outdoor night lights, applications where their color is good enough and efficiency and low cost are critical. The same factors are crucial for street lighting, where such white-light LEDs are spreading. Ann Arbor, Michigan, recently installed LED lamps with color temperatures of 6500 K in its downtown area.
Color temperature for indoor illumination is a big issue for many end users, and has slowed the shift from incandescent to fluorescent lighting. It is "an area of solid-state lighting more governed by opinion and emotion," says Fred Schubert of the Rensselaer Polytechnic Institute (Troy, NY). Some people insist on lamps with the 3000 K color temperature of incandescent bulbs, but others prefer higher color temperatures. Schubert suspects that many people are simply used to the red-rich light of incandescent bulbs. He notes that the color temperature of sunlight-often considered the acid test of color-varies from about 6000 K at noon to reddish at sunset.
Efficiency droop
A key issue that has emerged in efforts to scale white-light LEDs to higher power is efficiency droop. Light-emission efficiency reaches a peak at low current densities then declines as current density increases (see Fig. 2). First recognized in the mid-1990s, droop is most acute in LEDs with GaInN active regions. The DoE's office of Energy Efficiency and Renewable Energy lists it as a top technical issue to be resolved in solid-state lighting.1Droop typically appears by the time current density reaches a few tens of amperes per square centimeter and has become a critical problem as DoE and developers push to develop bright white-light LEDs for general illumination. The losses are substantial. At low drive currents, laboratory white-light LEDs can generate up to 250 lm/W, but luminous efficiency drops below 100 lm/W at the high drive currents needed for illumination.
All LEDs suffer some thermal droop, but the mechanisms behind the more severe droop seen in white-light LEDs have yet to be fully understood. At CLEO (San Jose, CA) last May, Schubert listed loss of injected electrons, Auger recombination in GaInN quantum wells, lack of hole injection in cladding and electron-blocking layers, and large electric fields within the active region as leading suspects.
Several techniques look promising for reducing efficiency droop. A leading approach is matching the polarization charges of layers within the nitride material, particularly between the quantum wells and quantum barriers, which reduces the troublesome internal electric fields.2 Others include making quantum wells wider, redistributing carriers within the quantum-well structure, and making doping more symmetric by p-doping parts of the active region.
These techniques are yielding improvements in the laboratory. In August, a group from Nichia Corp.'s Semiconductor Research Laboratory (Kaminaka, Japan) reported that driving an array of four yellow-phosphor white-light LEDs at 1 A yielded 1913 lm, more than a 20 W fluorescent lamp, at a luminescent efficiency of 135 lm/W, 1.5 times the luminous efficiency of a three-phosphor fluorescent.3 A team from the Gwangju Institute of Science and Technology (Gwangju, South Korea) and Samsung LED (Suwon, South Korea) increased quantum efficiency 20% by using trapezoidal quantum wells to enhance the overlap of electron and hole wave-functions at high current densities.4
Green LEDs
The biggest limitation on combining different colored LEDs to make white light is the lack of good green LEDs to provide light in the middle of the visible spectrum where the human eye is most sensitive. Traditional approaches have been to try to push the aluminum gallium indium phosphide (AlGaInP) system used for red LEDs and lasers to shorter wavelengths, and the InGaN materials used for blue LEDs to longer wavelengths.
Those approaches have had limited success. Efficiency of nitride emitters drops as indium is added to reduce bandgap energy and generate longer wavelengths. "It's a long-standing question in the scientific community as to why that occurs," says Kirstin Alberi of the National Renewable Energy Laboratory (Golden, CO). By changing the aluminum-to-gallium ratio in AlGaInP, she says, "you can get into the orange region, but as you start moving into the yellow or green, the bandgap goes indirect so efficiency is very low."
To get into the green gap from about 530 to 570 nm, NREL dropped aluminum from the system and used Ga0.7 In0.3P in the active layer. That blend is not lattice-matched to the GaAs substrate, so they fabricated a graded series of layers, allowing them to produce yellowish-green light at 562.3 nm, near the middle of the gap (see Fig. 3). So far the efficiency remains low, but Alberi says that combining the yellow-green light with a bluish-green InGaN LED and the usual blue and green LEDs could give a color-rendering index in the 90s, well beyond the 82 of compact fluorescents and close to the 100 of incandescent bulbs.Quantum dots and organic LEDs
Another way to enhance color is by developing new phosphors. Quantum dots are getting serious attention because they can generate the red light needed for color balancing, and their emission can be adjusted by adjusting their sizes.
Organic LEDs have become important in small displays, and hold out the promise of lower cost than inorganic LEDs, as well as fresh approaches to green sources. But organic LEDs also are hobbled by low performance and short lifetimes. In its solid-state lighting plan, DoE listed the highest luminance from an OLED panel last year as only 15 lm, with efficiency of 23 lm/W and a lifetime of only 5000 hours, just 10% that of inorganic white-light LEDs. The DoE is pushing to improve that performance, but the low current handling capacity of OLEDs could make them better suited for illumination panels than for use in bulbs.
Outlook
The best white-light LEDs can deliver more lumens per watt than any other lighting technology. The challenge developers face is doing the job for fewer dollars per lumen than entrenched technology. Today's first generation of solid-state lamps now costs about $20, in the same range as the first CFLs two decades ago. Those prices will come down as the technology improves and production scales up. Red, yellow, and green LED lamps are already standard in traffic signals because of their long lifetime and low energy usage. White-light LEDs do face challenges, but they will find a role if they can live up to their promise of long-lived, high-efficiency all-solid-state lamps.
REFERENCES
1. US Department of Energy, Solid-State Lighting Research and Development: Multi-Year Program Plan (March 2010).
2. M.F. Schubert et al., "Polarization-matched GaInN/AlGaInN multi-quantum-well light-emitting diodes with reduced efficiency droop," Appl. Phys. Lett., 93, 041102 (July 2008).
3. Y. Narukawa et al., "White light emitting diodes with super-high luminous efficacy," J. Phys. D: Appl. Phys., 43, 354002, doi:10.1088/0022-3727/43/35/354002 (2010).
4. S.-H. Han et al., "Improvement of efficiency droop in InGaN/GaN multiple quantum well light-emitting diodes with trapezoidal well," J. Phys. D: Appl. Phys., 43, 354004, doi:10.1088/0022-3727/43/35/354004 (2010).
Editor's note: Laser Focus World will be covering the market for high-brightness LEDs at the annual Laser & Photonics Marketplace Seminar, which will take place on Jan. 24, 2011, in conjunction with Photonics West. For more information, visit www.marketplaceseminar.com.
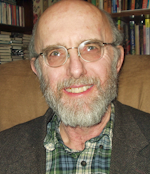
Jeff Hecht | Contributing Editor
Jeff Hecht is a regular contributing editor to Laser Focus World and has been covering the laser industry for 35 years. A prolific book author, Jeff's published works include “Understanding Fiber Optics,” “Understanding Lasers,” “The Laser Guidebook,” and “Beam Weapons: The Next Arms Race.” He also has written books on the histories of lasers and fiber optics, including “City of Light: The Story of Fiber Optics,” and “Beam: The Race to Make the Laser.” Find out more at jeffhecht.com.