Photonic Frontiers: laser weapons - Pumping up the power
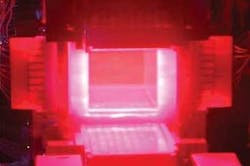
A big shootout is coming on the laser weapon frontier. By the end of next year, Northrop Grumman (Los Angeles, CA) and Textron Defense Systems (Wilmington, MA) are to demonstrate 100 kW output from competing diode-pumped solid-state lasers. The tests are sponsored by the Joint High Power Solid State Laser Program (JHPSSL) at the Air Force Research Laboratory (Kirtland AFB, NM) to show that solid-state lasers can meet military power requirements. Meanwhile, the Army Space and Missile Defense Command (Huntsville, AL) is evaluating industry designs for a beam-control system for its High Energy Laser Technology Demonstrator (HEL TD). The Army plans to integrate a ruggedized solid-state laser with the beam-control system on a wheeled vehicle for tests against targets in 2013.
These developments are vivid demonstrations of the tremendous progress in solid-state lasers. Diode-pumped Nd:YAG lasers are leading the 100 kW race, but military researchers also are developing high-power fiber lasers and diode-laser arrays for direct use as weapons. The armed services are looking at their battlefield needs. Northrop Grumman, builder of the only three megawatt-class U.S. gas lasers, in January opened a facility for making high-power solid-state lasers and integrating them onto military vehicles. “We firmly believe that directed energy is going to revolutionize the way we fight wars,” says Dan Wildt, director of business development for directed energy systems at Northrop Grumman.
Why solid-state laser weapons?
Solid-state lasers can’t match the raw power of chemical lasers, which have reached megawatt-class power and 30% efficiency. But raw power isn’t the only consideration on the battlefield. Field commanders want nothing to do with the logistics of delivering and handling bulky tanks of chemical fuels. Without fuel, a chemical laser would become another piece of broken equipment ditched on the side of the road.
Solid-state lasers run on electricity, so all they need is a portable generator and the diesel or gasoline that powers military vehicles. That’s a big logistical advantage, and a major reason the Pentagon chose not to go ahead with a mobile version of THEL, the Tactical High-Energy Laser, which shot down targets successfully but requires deuterium-fluoride fuel. Chemical lasers remain the most mature technology for near-term applications in airport defense, Wildt says, but he says solid-state lasers could replace chemical lasers when they reach sufficient power levels.
Battlefield lasers don’t have to match the range of megawatt-class lasers developed for long-range missile defense. Military planners consider 100 kW the threshold for defense over the scale of a battle, a few kilometers. The joint office’s goal is to demonstrate that power with a solid-state laser-each armed service has its own plans for using such lasers. The Army envisions mounting a laser in a truck or tracked vehicle to defend against rockets, artillery, and mortars (RAM in military jargon). This year the Air Force will test a chemical laser called the Advanced Tactical Laser in a C-130 “laser gunship,” and is considering putting a solid-state laser in a variant of its forthcoming Joint Strike Fighter. The Navy envisions laser defense of ships against cruise missiles.
Joint High Power Solid State Laser Program contractors demonstrated 25 kW operation for 300 seconds at the end of 2005. The joint program settled on diode-pumped Nd:YAG slab technology for the 100 kW phase-three demonstration, although it probably can’t reach the 30% efficiency of chemical lasers, says director Mark Neice. “Fiber lasers do hold the promise of being able to demonstrate those efficiencies,” he adds, but they have yet to reach the power level or maturity of solid-state or chemical lasers.
Solid-state heat capacity laser
The current record for solid-state laser power is 67 kW, which the Lawrence Livermore National Laboratory (Livermore CA) reported late last year from its Solid State Heat Capacity Laser (see Fig. 1). The Livermore system reached 25 kW in phase 2 of JHPSSL, but was not selected for phase 3. Laboratory officials hope to get military funding for a 100 kW field demonstration based on their design, but have yet to find a sponsor.
The heat-capacity laser uses massive diode arrays to pump slabs of ceramic Nd:YAG, made by fusing powder into a solid under high pressure to make transparent 10 cm slabs. The diode arrays are nearly 5 years old and limited to pulsed operation with a 10% duty cycle, explains program manager Bob Yamamoto. It reached average power of 25 kW by running four slabs in series perpendicular to the laser axis. To reach 67 kW, Livermore added another slab and pushed the pump-diode arrays to a 20% duty cycle. “But we have only run at that power for half a second,” Yamamoto says. “We don’t want to blow them up.”
Modules in series
Textron didn’t bid on the phase-2 JHPSSL demonstration, instead spending the time developing technology with internal funds. Ceramic Nd:YAG slabs were a key feature in design of the company’s phase-3 JHPSSL laser. Originally, the main attraction of the ceramic process was the ability to fabricate Nd:YAG slabs larger than is possible using crystalline YAG, but experiments showed the ceramic had smaller variations in refractive index and was more resistant to thermal cracking. The ceramic is as clear as the crystal, says Dan Trainor, director of laser systems. “If I handed [the ceramic] to you, you couldn’t tell the difference between it and the crystal,” he says.Another key element of the Textron design is a cavity structure they call “ThinZag,” in which the beam zigzags through pairs of Nd:YAG slabs tilted with respect to the laser axis (see Fig. 2). The green Nd:YAG slab is sandwiched between a pair of silica windows, with prisms that couple the beam into and out of the structure. Index-matched coolant flows between the silica slabs and the Nd:YAG. The slab is tilted relative to the beam direction so total internal reflection occurs at the outer faces of the windows, bouncing the beam back and forth through the Nd:YAG gain medium. Diode pumping is through the silica windows. In an actual laser, two ThinZag slabs are mounted together, with coolant flowing between the inner silica windows.
A single, two-slab module produces more than 15 W. Textron is stacking six of them in series to make a single 100 kW power oscillator, avoiding the need to phase-match separate beams. The total-internal-reflection design also avoids potentially troublesome optical coatings.
Modules in parallel
Northrop Grumman instead relies on parallel chains of slab amplifiers fed by a common master oscillator. To reach the 25 kW JHPSSL 2 goal, it ran two chains of four amplifiers in parallel. To reach 100 kW, it will use eight parallel chains. The company would not say whether it uses crystalline or ceramic YAG.The 15 kW diode-pumped chains are a standard design called Vesta, each containing a series of four Nd:YAG slab gain modules (see Fig. 3). Each slab is mounted between two coolers. The whole Vesta device has run for 20 minutes at a time with no change in performance, according to Jacqueline Gish, director of technology development for directed-energy systems. “Nothing limits us to 20 minutes; you just get bored after a while,” she says.
Because the amplifier chains are driven by the same oscillator, it’s straightforward to phase pairs of the beams relative to each other. “We consider it to be very low risk,” Gish says. The Vesta modules are intended as building blocks for a variety of military applications. “I can take a mission and decode how much power I need, and then tell how many building blocks I need to add,” says Wildt. “Our process doesn’t care how many we phase together.”
Outlook
The 100 kW JHPSSL lasers won’t be ready to deliver to the battlefield. The program aims to demonstrate technology that the armed services can adapt for their weapon platforms on the ground, in the air, or at sea. The high-energy laser and the beam-control system are “the two technology drivers” for weapon systems, says William Gnacek, HEL TD program manager at the Army Space and Missile Defense Command. Once those technologies are demonstrated, a ruggedized laser and beam-control system will be integrated with power generation, thermal management, and fire control and communications systems for use on a wheeled vehicle to be tested against rockets, artillery and mortars in 2013.
Military agencies are also looking at less mature technologies. Neice is working on a joint program to develop fiber lasers, which he says have the potential to match chemical-laser efficiency. Key technical issues are raising output of single-mode lasers and developing ways to combine their output into a high-quality beam. The Defense Advanced Research Projects Agency (DARPA, Arlington, VA) has launched a program called Architecture for Diode High Energy Laser Systems to develop diode lasers with efficiency greater than 60% and high-quality, low-divergence beams delivering 10 kW.
But the biggest challenge may be to build lasers that meet the needs of troops on the battlefield. Yamamoto recently attended a conference at a military base and talked with warfighters. “When I said ‘laser,’ they rolled their eyes,” he recalls. They don’t want complex equipment with thick manuals, he says. “They want a three-inch green button ‘laser on’ and a three-inch red button ‘laser off.’
About the Author
Jeff Hecht
Contributing Editor
Jeff Hecht is a regular contributing editor to Laser Focus World and has been covering the laser industry for 35 years. A prolific book author, Jeff's published works include “Understanding Fiber Optics,” “Understanding Lasers,” “The Laser Guidebook,” and “Beam Weapons: The Next Arms Race.” He also has written books on the histories of lasers and fiber optics, including “City of Light: The Story of Fiber Optics,” and “Beam: The Race to Make the Laser.” Find out more at jeffhecht.com.