PHOTONIC FRONTIERS: ORGANIC OPTOELECTRONICS - Organic LEDs try to live up to a bright promise
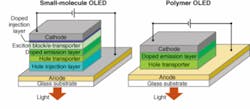
A couple of years ago, organic LEDs seemed destined to be the Next Great Thing in optoelectronics. Organic LED displays were all over the Society for Information Display conference in May 2005 (Boston, MA). The biggest screens reached 40 in., but the real action was in smaller displays for handheld devices. Philips (Eindhoven, The Netherlands) had one in an electric shaver and Kodak (Rochester, NY) had one on an electronic camera. Organic-LED displays promised to be thinner, lighter, and more efficient than liquid-crystal displays (LCDs) because they don’t require separate backlights. Organic LEDs (OLEDs) also can be viewed over a much wider range of angles. Could mass production be far behind?
We aren’t there yet. Kodak’s OLED camera quietly vanished from the market. Many MP3 music players have OLED displays today, but few of the current crop of other handheld electronic gadgets use OLEDs, says Ching Tang, a pioneer in OLED development at Kodak who recently joined the faculty at the University of Rochester.
What happened? While MP3 players use simple passive-matrix OLED displays that can be made less expensively than LCDs, other handheld devices require higher-performance active-matrix displays. And while OLEDs offer far better performance than LCDs for such applications, their cost is inhibiting their adoption, Tang says. “Right now the cost [of full-color OLEDs] is too high because it’s a new technology,” he says. “If the cost was not high, I think all handhelds would be using OLEDs.”
But cost is not the only issue. Although OLEDs have compelling attractions for small displays once costs come down, LCDs have a huge lead in the race for large-screen television and computer monitors because manufacturers have already invested enormous sums in LCD technology. Organic LEDs also face important technical issues, particularly attaining long-term stability and large-scale production. Similar issues face OLED development for solid-state white-light illumination, where efficient inorganic LEDs are offering tough competition. But organic optoelectronics may have an easier time winning in another potentially high-volume market-thin-film solar cells-where the low manufacturing costs of organics may beat more-efficient silicon (see “Organic solar cells,” p. 105).
Organics and light emission
Organic LEDs are based on organic compounds that conduct electricity like inorganic semiconductors but have other properties of plastics, leading to important differences in fabrication techniques, light emission, and durability from conventional inorganic semiconductors.
Two different classes of materials are used in OLEDs. One is a family of small organic molecules, which are evaporated from a warm area and deposited on a cooler material in a process that resembles photolithography in some ways but occurs at lower temperatures. Evaporative fabrication produces the best and most efficient devices, but is relatively complex and expensive. The alternative is liquid-state deposition of long-chain polymer materials, which can be printed onto a surface with an ink-jet process. Liquid deposition is attractively simple, but the device quality does not yet match those of small-molecule OLEDs. Both organic semiconductor processes can form LEDs on a greater variety of substrates than inorganic semiconductors.
The multilayer structures of OLEDs superficially resemble those of inorganic LEDs. When a positive bias is applied across the device, holes and electrons meet and recombine in an emission layer, generating light. Small-molecule and polymer OLEDs differ significantly in detail (see Fig. 1). In the small-molecule version (left), electrons and holes are injected from cathode and anode through injection layers and pass through transporter layers to reach the emission layer. In polymer OLEDs (right), the cathode injects electrons directly into the emission layer, but the anode injects holes through a hole transport layer. In practice, the emitted light emerges through the transparent anode, which is deposited on a glass substrate.
Recombined electron-hole pairs (excitons) transfer their energy to light-emitting dopants in the emission layer. The details depend on the exciton spin; nominally one-quarter of excitons are formed in a singlet (spin-zero) state and three-quarters are in a triplet (spin-one) state. Fluorescent dyes can only convert the energy of singlet states into photons; a triplet state cannot emit a photon to drop into a singlet state, so the energy must be dissipated as heat. An alternative is electrophosphorescence, in which molecules containing a heavy metal such as platinum capture the energy from both singlet and triplet states, and hold it long enough for the states to mix and convert the energy from triplet states into photons. Some losses remain, but efficiency can be increased by combining both types of emitters, operating at different wavelengths.
OLED displays
The most promising application so far for OLEDs is in small color displays. Although many OLED displays are monochromic (see Fig. 2), the display industry is more excited about full-color displays for applications such as cell phones. Because OLEDs directly emit light, they promise higher efficiency than transmissive LCDs, which require a separate backlight and inevitably filter out much of the emitted light. Unlike backlights, OLEDs do not have to be generating light all the time, further increasing efficiency. That higher efficiency translates into longer battery lifetime, a vital concern for small portable devices. Avoiding a backlight also makes OLEDs thinner and lighter than LCD displays. Organic LED displays also are viewable across a broader range of angles than LCDs; Samsung claims a viewing angle greater than 170° for a 2.65 in. display with 480 × 640 pixels.1 Organic LEDs also can be made flexible, or deposited on curved surfaces, unlike LCDs, which require extremely flat glass substrates.The leading approach is to fabricate an array of individually controlled red, green, and blue diodes, which add to produce white. Developers are also considering either filtering the output of white LEDs to produce the primary colors, or converting part of the light from blue emitters to green and red, but such conversions reduce overall emission efficiency.
Like LCDs, OLEDs are made with either passive- or active-matrix addressing. The electrodes in passive-matrix displays are strips running vertically or horizontally across the array; applying a voltage to one vertical and one horizontal grid element at a time, to switch on the LED where they intersect. Active-matrix OLEDs include dedicated electronic circuits that control switching of individual pixels; they are more expensive, but are faster and more efficient, making them more attractive for more demanding applications.Sizes of OLED displays are steadily increasing, with some demonstration displays targeted for wide-screen television reaching 40 in. However, OLEDs got a late start in the wide-screen race, and manufacturers have already made huge investments in factories to produce LCD screens. Organic LEDs also have a lifetime problem; the blue emitters fade after a few thousand hours of viewing. That’s not a problem with small, portable devices like MP3 players and cell phones, which have limited lifetimes and do not require continual operation of the display. But televisions typically are operated for thousands of hours each year, and viewers will get the blues if the colors on their expensive wide screen start fading after a year or two.
Illumination
White-light OLEDs are also in the race for solid-state illumination sources, where the key goals are good color rendition and high efficiency measured as lumens per watt. Both have been improving steadily. Universal Display (Ewing, NJ) has reported efficiencies above 30 lm/W from electrosphosphorescent OLEDs, double that of incandescent bulbs but still well below fluorescent lamps. This spring, a team led by Stephen Forrest, now at the University of Michigan, reached 37.6 lm/W.2 A 2001 roadmap developed by the Optoelectronic Industry Development Association (Washington, D.C.) and the U. S. Department of Energy envisioned ultimately reaching 120 lm/W.3
However, inorganic white-light LEDs are now ahead of OLEDs in meeting key requirements for solid-state lighting, says Jeff Tsao, who works on solid-state lighting at Sandia National Laboratories (Albuquerque, NM).4 Inorganic LEDs have already found niches in such markets as automobile headlights. Tsao says key problems with OLEDs include their lifetime and sensitivity to water and oxygen, which requires hermetic seals. Inorganics also promise inherently higher efficiency, says Lewis Rothberg of the University of Rochester. But developers of OLEDs are not ready to give up, and the potentially low cost of OLEDs may earn them a niche as low-intensity, large-area illuminators.
State of the art and outlook
Organic LEDs have a bright promise in principle, but realizing that bright future depends on meeting a number of practical challenges. Manufacturing costs must be driven down to carve out a larger niche for small OLED displays in handheld electronics. Efficiencies and operating lives must be increased. Patterning for high-resolution displays must be perfected. If all goes well, OLEDs are likely to find a growing niche in small portable devices where their light weight and potential efficiency offer big advantages. Large-screen television looks to be a tougher challenge unless breakthroughs bring big improvements.
REFERENCES
1. H.K. Chung and S.T. Lee, Information Display 21, 22 (Dec 2005)
2. Y. Sun et al, Nature 440, 908 (April 13, 2006).
3. Optoelectronics Industry Development Association, Organic Light Emitting Diodes (OLEDS) For General Illumination, An OIDA Technology Roadmap (March 2001) www.OIDA.org.
4. U.S. Department of Energy, Basic Research Needs For Solid-State Lighting, Report of the Basic Energy Sciences Workshop on Solid-State Lighting, available at www.er.doe.gov/bes/reports/files/SSL_rpt.pdf.
Organic solar cells poised for growth
Organic LEDs aren’t the only promising application of organic optoelectronics. “Organic photovoltaics have a very bright future,” says Lewis Rothberg of the University of Rochester. Organic solar cells can’t match the energy-conversion efficiency of silicon, but even amorphous silicon is expensive to produce. Organic optoelectronics should be much cheaper to produce in large volume, and area is the key to success in solar energy. If solar cells are cheap enough to cover your roof, you can afford to settle for lower efficiency per square foot. “If you can get any reasonable efficiency and photostability, you’re going to be in really good shape” with organic photovoltaics, Rothberg says.
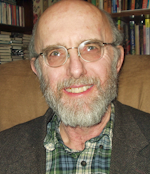
Jeff Hecht | Contributing Editor
Jeff Hecht is a regular contributing editor to Laser Focus World and has been covering the laser industry for 35 years. A prolific book author, Jeff's published works include “Understanding Fiber Optics,” “Understanding Lasers,” “The Laser Guidebook,” and “Beam Weapons: The Next Arms Race.” He also has written books on the histories of lasers and fiber optics, including “City of Light: The Story of Fiber Optics,” and “Beam: The Race to Make the Laser.” Find out more at jeffhecht.com.