LASER MARKING: How to choose the best laser for your marking application
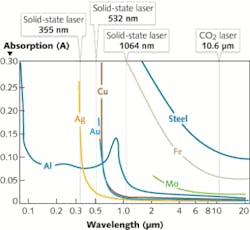
DENNIS KAMINSKI
In laser marking processes, the type of material, quality of mark required, and speed will all play a role in the optimum choice of laser. Although solid-state continuous-wave and CO2 lasers are used for marking, they are generally not used to mark metal, so this article will focus on solid-state pulsed lasers. Within that category, there are several technology options when choosing a pulsed laser for marking. These include Nd:YAG, Nd:YVO4 (vanadate), and fiber lasers, each with its pros and cons.
It is also important to understand how the material to be marked absorbs laser light at the wavelength of the laser chosen. Ferrous and non-ferrous materials have excellent absorption at 1064 nm, while precious metals do so at 355 and 532 nm. Plastics also absorb the higher wavelength laser output (see Fig. 1).
Laser technologies
The Nd:YAG laser was introduced more than 25 years ago and is the workhorse of the industry. Originally these lasers were lamp-pumped, but have subsequently evolved so that diode pumping is now most common. The diode-based systems are robust with excellent mean time before failure (MTBF). Some manufacturers expect more than 35,000 hours of life prior to failure of the diodes. One advantage of Nd:YAG lasers is their beam quality, which leads to a smaller spot size of the laser. The small spot size, along with short pulses, produces high peak power that can be beneficial in deep engraving with crisp, clear marks and small characters.
The vanadate laser can emit at three different wavelengths: 1064, 532 (green), and 355 nm (blue). Vanadate lasers are also diode-pumped and deliver beam quality with pulse-to-pulse stability, making them well suited for ablation marking and heat-affected zone (HAZ) applications. One of the vanadate laser markets is day/night marking—an automotive application in which a top coating is removed to allow light to backlight buttons at night—typically ablating a top coating to expose a lower surface without damaging it.
Approximately six years ago, fiber lasers were introduced to the marking world and have been the topic of discussion in virtually every marking opportunity. The fiber laser does not have the same beam quality as Nd:YAG or vanadate lasers, which limits the amount of peak power available. The fiber laser can anneal stainless steel due to its long pulsewidth and larger spot size, putting more heat in the part to draw the carbon to the surface. It’s worth noting that there only a handful of fiber-laser manufacturers that offer the laser source to a third party for integration into a marking system.
In terms of operating costs and consumables, these three laser technologies are almost identical, so an end user can choose the optimum laser technology without having to make cost tradeoffs. One thing to keep in mind is that the output power of all solid-state lasers degrades over time, but it is possible to calibrate the system to maintain the same power in the laser as the day it left the factory. This will allow the laser to maintain the same mark quality and speed as the day it arrived and was put into production.
Beam properties—Laser marking beam quality is specified in terms of an M2 value, which is typically provided by all laser manufacturers. A Gaussian beam has an M2 of 1 and allows for the smallest spot size in relation to the wavelength and optics used. The best beam quality found in Nd:YAG and vanadate laser marking systems has an M2 of 1.2. Fiber-based systems typically have an M2 value of 1.7, meaning a larger spot size and less power density. Basically, better beam quality produces smaller linewidths, sharper contours, higher marking speed (because of high power density), and deeper engraving. Good beam quality also provides better depth of focus than a laser with lower beam quality. Marking on a curved surface using a laser with an M2 of 1.2, for instance, will give a crisper mark as the depth of focus changes than will a laser with a higher M2 such as that from a fiber laser.
Pulse repetition rate—The YAG and vanadate lasers are quite different from the fiber laser with respect to peak power and pulse repetition frequency range. The pulse duration emitted by fiber systems configured as master oscillator fiber power amplifier (MOFPA) can be adjusted, which has a direct impact on the available pulse repetition rates available to optimize the laser marking process (see table).
Typical values | YAG | Vanadate | Ytterbium (fiber) |
Pulse duration (ns) | 10–150 | 5–30 | 10–200 |
Beam quality (M2) | <1.2 | <1.2 | <2 |
Peak power (kW) | High, 100 kW range | Medium, 80 kW range | Low, 10 kW range |
Average power (W) | 5–30 | 5–40 | 10–50 |
Pulse repetition frequency range | 5–80 kHz | 20–120 kHz | 20 kHz–1 MHz |
Applications
The most common terms used in laser marking include: engraving, annealing, ablation, and color change of plastics. Each of the lasers discussed can be chosen to optimize the performance of the laser marking process. When ablating day/night design components, a vanadate laser performs well due to the short pulses and pulse-to-pulse stability at higher repetition rates. This allows removal of a painted top surface without damaging pad-printed plastic base material (see Fig. 2). Ablation also is a common practice in marking anodized aluminum, which is by far the most forgiving laser process.When engraving material, it is important to have optimum parameters in regard to frequency and speed in order to evaporate the material. Typically, lasers with short pulses and high peak power perform best for this application.
All three laser technologies will have a place in industrial manufacturing for years to come. The technology will continue to evolve in order to meet the changing demands of the manufacturing environment. When selecting a laser marker, it is important to partner with a laser company that can demonstrate the advantages of each technology as it relates the material to be marked. Many manufacturers have application labs that will test materials with a laser that fits in regard to speed, quality, and budget.
DENNIS KAMINSKI is the Midwest regional sales manager for the TruMark Group of Trumpf; e-mail [email protected]; www.us.trumpf.com.