ROLLEX project demonstrates successful OLED roll-to-roll production
Dresden, Germany--Scientists from the Fraunhofer Institute for Photonic Microsystems IPMS and the Fraunhofer Institute for Electron Beam and Plasma Technology FEP for the first time manufactured a flexible organic light-emitting diode (OLED) in a roll-to-roll manufacturing process and encapsulated the device in a subsequent inline step. This process design would allow production in a single plant. See also, "VGA OLED microdisplay is picoprojector source." The method was developed in the frame of the project ROLLEX (roll-to-roll production of highly efficient light-emitting diodes on flexible substrates, support codes 13N8858 and 13N8857), funded by the German federal ministry of education and research (BMBF).
Professor Karl Leo, director of the Fraunhofer IPMS, said, “The successful assembly of an OLED in a roll-to-roll process means a breakthrough on the way to highly efficient and competitive devices. The achievement of this project proves the capacity of Dresden as a focal point for research in organic electronics.”
A major component of flexible organic LEDs is the homogenous encapsulation of luminescent layers with transparent barrier layer systems. Permeation of only small amounts of humidity or oxygen shortens the lifetime of the devices drastically, which explains the strong need for barrier systems protecting the luminescent materials on a large area without defects. However, the barrier layers should not absorb the emitted light and should not interfere with the colors of the light.
The researchers of the Fraunhofer Institutes deposited OLED materials on a cheap aluminum foil in a roll-to-roll pilot plant, further encapsulated the luminescent foil with a barrier layer system—patented by the Fraunhofer FEP—without compromising its luminosity.
Nicolas Schiller, head of the business unit Coating of flexible products at the Fraunhofer FEP adds, “The coating processes are all done in a roll-to-roll modus with a continuously moved substrate which opens up strong potential to reduce costs.”
Besides OLEDs, other devices such as organic solar cells or memory systems could be realized in intermediate terms. OLEDs convert electricity very efficiently into light of high quality. However, existing OLEDs on the market are costly and mostly deposited on rigid materials such as glass. The development of flexible OLEDs that can be manufactured on an industrial scale promises broader marketing of the environmentally sound and highly efficient devices.
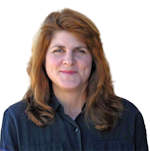
Gail Overton | Senior Editor (2004-2020)
Gail has more than 30 years of engineering, marketing, product management, and editorial experience in the photonics and optical communications industry. Before joining the staff at Laser Focus World in 2004, she held many product management and product marketing roles in the fiber-optics industry, most notably at Hughes (El Segundo, CA), GTE Labs (Waltham, MA), Corning (Corning, NY), Photon Kinetics (Beaverton, OR), and Newport Corporation (Irvine, CA). During her marketing career, Gail published articles in WDM Solutions and Sensors magazine and traveled internationally to conduct product and sales training. Gail received her BS degree in physics, with an emphasis in optics, from San Diego State University in San Diego, CA in May 1986.