Pasadena, CA--A new form of silicon (Si) photovoltaic cell created by researchers at the California Institute of Technology (Caltech) consists of Si wires embedded in a polymer substrate.1 The arrangement has two advantages: first, far less Si can be used to usefully absorb the same amount of sunlight as a standard Si solar cell; and second, the Si/polymer cell is flexible.
The silicon-wire arrays absorb up to 96% of incident sunlight at the peak absorption wavelength, and 85% of the total collectible (above-bandgap) sunlight; this occurs despite the fact that the wires in the arrays cover only between 2% and 10% of the total surface area. In addition, the arrays have an internal quantum efficiency of between 90% and 100%. "High absorption plus good conversion makes for a high-quality solar cell," says Harry Atwater, who is a Howard Hughes Professor, a professor of applied physics and materials science, and the director of Caltech's Resnick Institute. "We've surpassed previous optical microstructures developed to trap light."
Scattering increases apparent area
Each wire measures between 30 and 100 microns in length and only 1 micron in diameter. "The entire thickness of the array is the length of the wire," says Atwater. "But in terms of area or volume, just 2% of it is silicon. The collective scattering interactions between the wires make the array very absorbing."
"Having these be complete flexible sheets of material ends up being important," notes Atwater, "because flexible thin films can be manufactured in a roll-to-roll process, an inherently lower-cost process than one that involves brittle wafers, like those used to make conventional solar cells."
The next steps, according to Atwater, are to increase the operating voltage and the overall size of the solar cell. "The structures we've made are square centimeters in size," he says. "We're now scaling up to make cells that will be hundreds of square centimeters--the size of a normal cell."
REFERENCE:
1. Michael D. Kelzenberg, et al., Nature Materials, published online: 14 February 2010 | doi:10.1038/nmat2635
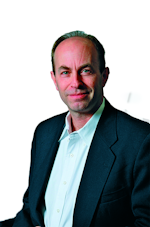
John Wallace | Senior Technical Editor (1998-2022)
John Wallace was with Laser Focus World for nearly 25 years, retiring in late June 2022. He obtained a bachelor's degree in mechanical engineering and physics at Rutgers University and a master's in optical engineering at the University of Rochester. Before becoming an editor, John worked as an engineer at RCA, Exxon, Eastman Kodak, and GCA Corporation.