The recent news that Continental, a sustainability and mobility solutions provider, will begin developing auto display solutions using Waterloo, ON, Canada-based VueReal's MicroSolid Printing technology marks another milestone for the novel approach to micropixel fabrication.
Though details about Continental's plans are scant, a VueReal LinkedIn post quotes Continental's director of strategy Ulrich Lüders saying it will implement the technology in its "most advanced automotive display solutions." And that the company also would benefit "from completely new possibilities in designing and manufacturing our interfaces, resulting in a never-before-seen user experience."
In a recent interview with Laser Focus World, VueReal founder and CEO Reza Chaji answered the headline's question with a "yes." He explained that the company is focusing first on growing in the microLED display market, particularly in the automobile industry, but that the company's technology can eventually apply to applications that integrate various micro-semiconductor devices, including biosensors or artificial intelligence (AI) chiplets. "MicroLED displays are the main application today, but it can go beyond that to sensors for autonomy, for health, security, biometrics—any application you need," he said.
Chaji said the company's goal is to enable companies to integrate the devices made using a semiconductor wafer process into surfaces to create new applications. "We want to offer this platform—provide the technology, the cartridge, and the idea because it enables a lot of people to come up with new applications, and it will expand the market much wider and faster," he said. The approach, he adds, is like what the smartphone did to the app market.
How solid printing works
The micro-solid printing technology addresses one of the most significant challenges in microLED adoption—the efficient transfer of LEDs from the wafer to the backplane. Current solutions—laser and pick-and-place systems—require costly upfront investment and are difficult to scale to high-volume production, Chaji said.
The new process uses proprietary systems to load the LEDs into a cartridge, inspect them to ensure they all meet quality standards, and then selectively put them where they need to be, Chaji explained. This process delivers high yield and throughput because "we don't need to pick and place the LEDs, and we don't need to laser for every LED to be released," he added. "And the way we develop the cartridge is less expensive than the way you prepare the LEDs with pick-and-place or laser."
Critically, the system can be integrated into existing production lines, which enables cost-effective display production "at any scale anywhere," Chaji said. "With our printer, the capex is very low, about a few million dollars vs. a few billion [for traditional display fabrication]." Then, with the cartridge, manufacturers can print displays at any volume, whereas traditional setups' initial cost is only practical for very high-volume production.
The system also uses less energy and is more environmentally friendly than traditional approaches, according to Chaji.
Going to market
VueReal's primary business strategy is to deliver and help companies integrate the technology into their existing production lines. To do this, the company plans to work with its partner companies to create a turnkey solution, enabling companies with little experience to incorporate microLED manufacturing into their facility. With that, "core customers can just copy and paste into their facilities and start producing products," Chaji said.
Eventually, VueReal plans to expand this offering to include systems that will integrate sensors and other chiplets and even allow customers to mix and match microdevices, enabling companies to selectively and mass print various devices—LEDs, sensors, AI chiplets, etc.—onto a surface to create new and different applications.
"We want to do hardware, so the idea is that we create cartridges with different devices," Chaji said. "And companies buy our printers, buy the cartridge, and come up with customized applications."
For strategic markets, VueReal works directly with OEMs to develop custom products. VueReal makes displays and lighting for select customers. In early December 2023, the company announced the successful development and shipment of high-resolution and high-transparency microLED displays to its partners.
In late March, Invest Ontario provided a Can$2 million grant, and Sustainable Development Technology Canada (SDTC) pledged Can$8.5 million to enable VueReal to increase its workforce and support research and development at the Waterloo facility.
Democratizing capabilities
Ultimately, VueReal aims to democratize display and smart-system production for applications in auto, smartwatch, smartphone, and AR/VR initially, then move beyond displays to help companies integrate sensors for fitness, health, security, and automation applications.
Chaji noted the technology will enable small and mid-size companies to develop and produce new products from low-volume prototypes and then scale production as necessary.
"My goal is to kind of make this platform as user-friendly as possible and then let people with creative ideas come up with a lot of applications," Chaji said.
ACKNOWLEDGEMENT
MicroSolid Printing is a trademark of VueReal.
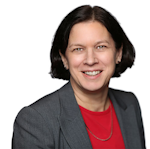
Patricia Panchak
Patricia Panchak has held editorial leadership roles for over 25 years—15 years of which were with IndustryWeek as the brand’s managing editor and then editor-in-chief. From 2011 through 2017, she then served as group content director for the Manufacturing & Supply Chain Group, which included IndustryWeek.
Since 2018, Patricia spent time as a business journalist, editorial consultant, and public speaker, specializing in business and manufacturing strategies and best practices; trends and emerging technologies; and public policy.