High-power and high-energy lasers have spawned countless applications in industry, academia, and the military. However, the same laser characteristics that enable these applications also give these lasers the capacity to damage and destroy the very optics used to control their beams. In response, optical designers and fabricators have built up a store of knowledge based on both theory and application (with the latter being especially important) that has allowed them over time to steadily raise the laser-induced damage threshold (LIDT) of optics, including their coatings, intended for use with high-power and high-energy lasers.
High-LIDT optics typically require one or more of the following: a glass selected to be highly transmissive at the laser wavelength and to have few internal flaws; especially high-quality surface treatment (grinding and polishing) to minimize size and number of defects; high-LIDT-compatible optical coating materials; and coating-deposition techniques that minimize defects. (The concept of LIDT can even be extended beyond optics to mechanics and optoelectronics.)
The topic of LIDT is vast. Laser Focus World has covered LIDT extensively (including a book review).1-7 As a result, this short product-focused article on high-LIDT optical coatings will not delve into the science and accumulated wisdom behind these coatings—instead, a sampling of commercial products will be presented along with some technical background behind them provided by their manufacturers. Following are a few illustrative examples of what can be had on the market.
Polarizing optical coatings
“The higher-power work we are doing here is twofold: narrowband antireflection (AR) coatings and noncemented polarizing beamsplitter (PBS) cubes,” says Michael Gartman, design engineer, optics at Thorlabs (Newton, NJ). “We appreciate how critical cleanliness is for high-power parts, so all of our parts are prepped, cleaned, and loaded in a class 10,000 clean room. These coatings are composed of hafnia and silica and are e-beam deposited without using ion-assisted deposition, which can degrade LIDT. We have tested these parts extensively, both internally and with an outside laser-damage vendor.”
As an example of a product line that would demonstrate Thorlabs’ expertise with high-LIDT coatings, Gartman chooses the company’s high-power laser-line PBS cubes (see Fig. 1). The cubes are designed for the three major Nd:YAG harmonics, as well as for other common high-power laser lines such as laser diodes at 405 nm and 780–808 nm. “We have a customer demand for laser-line-targeted PBS cubes with higher damage threshold than is typically available,” says Gartman. “We have extensive in-house knowledge of optical contacting, which creates adhesive-free bonds, so we saw an opportunity there.”
After cleaning and prepping in the clean room, the parts are contacted in the same room to prevent contamination, Gartman explains. After assembly, the parts are tested for laser damage and results are published on Thorlabs’ website. “We achieved greater than 10 J/cm2 at 10 ns for the 532 nm and 1064 nm parts, as well as 3 J/cm2 at 10 ns for the 355 nm parts, while maintaining high transmission and an extinction ratio of greater than 2000:1,” notes Gartman. “There’s going to be some interplay between extinction ratio, LIDT, and getting the parts contacted; thicker coatings result in higher extinction ratios, but more difficulty contacting, and potential lower LIDT. There is some tradeoff there. Using fused silica as a substrate also results in some design tradeoffs—typically with PBS cubes, a higher-index glass is used to broaden the bandwidth as well as increase extinction ratio. Coatings deposited on fused silica, however, tend to have higher damage thresholds than coatings deposited on other glasses.”
High-power coatings on PBS allow for their ease of use as attenuators without resorting to the relatively complicated geometries of crystal polarizers, says Gartman, who adds, “The PBS cubes are often used as beam combiners or for picking off a sample beam, but most of the customers use them to attenuate their beams, either alone, in pairs, or with the addition of a half-wave plate.”
Coatings for inertial-confinement fusion
“Optimax manufactures ARs, mirrors, and filters for both pulsed high-energy and CW high-power laser applications,” says Pete Kupinski, optical coating manager at Optimax (Ontario, NY). “The most-challenging pulsed applications are typically found in inertial-confinement fusion programs, where pulse lengths range from picoseconds to nanoseconds and the wavelengths from deep ultraviolet (DUV) to near-infrared (near-IR). The most-difficult high-average-power laser applications are typically for military applications.”
Kupinski discusses a difficult project Optimax had with a customer in the nanosecond regime at a 211 nm wavelength, for which the customer required optics and coatings at this wavelength that could survive an unprecedented amount of fluence without laser damage. “This project required several rounds of product development, bringing both Optimax’s and the customer’s expertise to bear,” says Kupinski. “Collaboratively, we were able to arrive at a process that met their specification. Work to continue to improve the coatings performance is ongoing.”
For many high-energy laser applications, including the one described above, Optimax finds that it is critical to have good engineering control of both the polished surface of the optic and the coating, according to Kupinski. “Control of defects and contaminants in the first 150 nm of a glass lens surface is as critical as the coating in some cases,” he says. “For high-energy laser applications, good performance is often in the details: lens-fabrication processes, lens-cleaning processes, coating process, coating design, and packaging all matter. To maintain the required process control for these applications, Optimax has a division dedicated to these types of optics, called the Laser Grade Optics group.”One of the group’s instruments is a photothermal common-path interferometer (PCI, see Fig. 2) that is capable of measuring coating and glass absorption to less than one part per million. “Optimax has the ability to make these measurements for applications spanning from the UV to near-IR,” says Kupinski. “Our measurements have been benchmarked against five laboratories in the U.S. and Europe that specialize in these types of measurements. Low absorption is critical for good lens performance in high-average-power laser applications, not only for LIDT reasons but also to limit optic heating and distortion in use.”
HR and other coatings
II-VI Laser Solutions (Saxonburg, PA) produces a broad variety of high-LIDT optics, says Steve Rummel, the company’s vice president of IR optics. “For high-power CW (>10 kW) fiber-laser applications, II-VI has developed a high-reflection (HR) coating for metal substrates such as copper or aluminum (see Fig. 3). This HR coating has been tested at ≥200 MW/cm2 in the 1070 nm range. For high-power CO2 laser applications such as extreme-ultraviolet (EUV) lithography, coated diamond optics are used. Antireflection (AR)-coated diamond has achieved a pulsed LIDT ≳ 25.0 J/cm2 and CW LIDT over 2.5 MW/cm2.”Other high-LIDT optics from II-VI include custom pulsed coatings designed for infrared laser applications, such as AR, partial and high reflectors, mirrors (total reflectors), and phase-shift-controlled designs, notes Rummel.
“The oxide-enhanced high-reflector (HR) coating was designed to complement simple or complex diamond-turned optical surfaces on metal mirror substrates,” Rummel says. “As the power of fiber laser cutting and welding systems continues to increase, a coating that can take that kind of energy is required.”
In high-power fiber laser cutting systems, water-cooled metal mirrors provide greater stability in the >10 kW range, notes Rummel. The oxide-enhanced HR coating supports complex mirror geometries such as faceted mirrors and variable-radius mirrors (VRMs) that add flexibility to these laser systems. Beam-shaping mirrors with this coating give customers options for complex cutting applications, he adds.Coatings for materials-processing optics
“Jenoptik designs and produces high-LIDT optical coatings for many of our products,” says Jay Kumler, president of Jenoptik Optical Systems, North America (Jupiter, FL). “We have invested significantly in the development of high-LIDT AR coatings for the UV, visible, and near-IR spectral bands. One particular type of coating that is especially high-performance is our AR coatings for 355 nm and 266 nm, which are used in our Silverline f-theta laser materials-processing lenses (see Fig. 4). The high-LIDT coatings that were specifically designed for this application extend the lifetime of these lenses and help the lenses provide high-uniformity, high-consistency spots on the target.”
High-LIDT is especially important when using short-pulse lasers—the high-performance coatings are critical for applications like laser drilling, perforating, and annealing. “Our Silverline lenses handle beam powers up to 4 kW without active cooling,” says Kumler. “If the coating on these lenses had lower LIDT, the lenses would need to be replaced frequently, driving up the cost to the manufacturer.”
REFERENCES
1. L. Gallais, “Optical materials withstand assault from high-power ultrashort-pulse lasers,” Laser Focus World, 50, 6, 25–30 (Jun. 2014).
2. J. Wallace, “LIDT wavelength-scaling rule of thumb shown to be inaccurate,” Laser Focus World, 51, 8, 9 (Aug. 2015).
3. J. Yager, “Advances in Optical Systems: How to apply laser-induced damage threshold (LIDT) test techniques,” Laser Focus World, 52, 10, 25–29 (Oct. 2016).
4. G. Overton, “Laser Optics: Meter-class, high-LIDT optics meet petawatt, ultrafast requirements,” Laser Focus World, 52, 12, 19–21 (Dec. 2016).
5. M. Thomas, “New laser-damage evaluation techniques boost testing capabilities,” Laser Focus World, 53, 5, 27–30 (May 2017).
6. J. Wallace, “Combining optics surface-treatment techniques can boost the laser-induced damage threshold of fused silica,” Laser Focus World, 54, 1, 12 (Jan. 2018).
7. J. Wallace, “Book Review: Laser-Induced Damage in Optical Materials,” Laser Focus World online (Mar. 2015); http://bit.ly/LIDTbookreview.
For More Information
Companies mentioned in this article include:
II-VI Laser Solutions
Saxonburg, PA
Jenoptik Optical Systems Jupiter, FL
www.jenoptik.us/products/optical-systems
Optimax
Ontario, NY
Thorlabs
Newton, NJ
DISCLAIMER: While we try to include information from the broadest possible number of companies that manufacture the products featured in our Photonics Products series, because of limited word count as well as deadlines that cannot always be met by requested contributors, we cannot possibly include all companies and regret if your company is not included in our series.
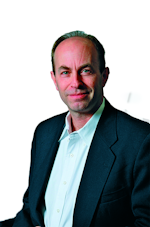
John Wallace | Senior Technical Editor (1998-2022)
John Wallace was with Laser Focus World for nearly 25 years, retiring in late June 2022. He obtained a bachelor's degree in mechanical engineering and physics at Rutgers University and a master's in optical engineering at the University of Rochester. Before becoming an editor, John worked as an engineer at RCA, Exxon, Eastman Kodak, and GCA Corporation.