Small refractive lenses with very short-radius surfaces typically undergo quality assurance via visual inspection—a method increasingly unwieldy as these small lenses (for example, molded lenses) make their way more and more into mass-produced applications for automobiles, mobile devices, medical instruments, and the like. Many approaches have been taken to move the burden of lens inspection from humans to automated systems. Now, a group from the Centre of MicroNano Manufacturing Technology at Tianjin University (Tianjin, China) has come up with their own comprehensive defect-detection system that the researchers say combines transmitted fringe deflectometry, dark-field illumination, and light transmission to find lens microdefects.
The system was designed to move beyond just the characterization of scratches, pits, and dust to the detection of, for example, fine surface watermarks generated during lens production. The newly developed system combines transmitted grating-fringe illumination coupled with image-processing algorithms to highlight watermarks; backlighting and gray-scale threshold processing following light-transmission techniques to detect internal lens impurities; and a technique using sidelighting and the scattering properties of light to detect haze defects. The system performs batch measurement of multiple lenses at the same time. In experiments using lenses with diameters of 12 to 14 mm and batches of 12 pieces, measurement times of down to 17 s per batch were achieved; for smaller lenses, the measurement time was even shorter. The minimum detectable surface-profile defect width was 4.73 µm, while the minimum detectable internal impurity diameter was 9.46 µm. Such detection results can be used to guide optimization of process parameters for lens production. Reference: J. Pan et al., Appl. Opt. (2019); https://doi.org/10.1364/AO.59.000234.
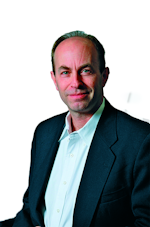
John Wallace | Senior Technical Editor (1998-2022)
John Wallace was with Laser Focus World for nearly 25 years, retiring in late June 2022. He obtained a bachelor's degree in mechanical engineering and physics at Rutgers University and a master's in optical engineering at the University of Rochester. Before becoming an editor, John worked as an engineer at RCA, Exxon, Eastman Kodak, and GCA Corporation.