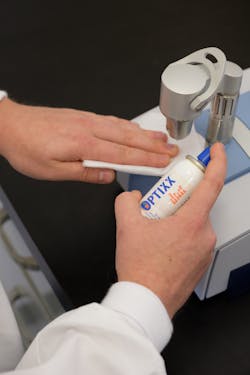
VENESIA HURTUBISE
Bar-code scanners, displays, scientific instruments, medical diagnostic tools, and laser materials-processing equipment all rely on optical elements such as lenses, prisms, diffraction gratings, optical filters, and mirrors. Typically produced in fabricating shops much cleaner than the average machine shop, such optical elements may still be subject to contamination from dust particle exposure, fingerprint smudges, gasified fumes, and other production debris that detrimentally impact optical element performance. Consequently, proper cleaning before final coating, packaging, and shipping is critical to avoid risk of poor optical-component performance or even permanent damage.
Many optical components such as mirrors and prisms are typically cleaned by hand. Light surface contamination of large, loose dust particles may only need a blast of clean, dry compressed gas to remove dust particles. Dry nitrogen or CO2 are typically best since other pressurized gases could release propellant and form liquid droplets on the optical surface.
More-robust optics can withstand more manual cleaning. These processes typically use lint-free fiber-optic wipes and a specialty fiber-optic cleaning fluid. The fluid loosens the contamination by eliminating static while the wipe binds dirt to its surface without scratching. Always pull the wipe in one direction and always dispose of the wipe after each use to avoid cross-contamination.
Use the right fluid
Some fabricators use methyl ethyl ketone (MEK), methylene chloride (MEC), methanol, acetone, or reagent-grade alcohol to clean optics. However, MEK and MEC are possibly toxic, and methanol and acetone could damage the substrate. Acetone is also damaging to skin. In addition, alcohol tends to leave streaks and residue behind (see Fig. 1).
There are some widely available alternatives to alcohol for cleaning fiber optics. Many of them clean optical elements just as well as, if not better than, alcohol. Such alcohol alternatives don’t leave a residue behind or absorb impurities from the air like alcohol can, so it provides more-thorough cleaning. Alcohol alternatives are typically nonflammable, adding to worker safety. They often come in hermetically sealed cans, which ensure the high-purity cleaning fluid isn’t contaminated. Hermetically sealed cans dispense the cleaning fluid in metered doses, reducing waste; won’t spill if tipped over; and reduce worker exposure.
Automated vapor degreasing
Many lenses, optical filters, and other optical elements are made from more-robust glass materials and are safely cleaned with more-automated procedures and tools. Vapor degreasing is a long-term batch-cleaning process that effectively cleans substrates while also addressing other burdens like sustainability and cost-effectiveness. Some companies are renewing their interest in vapor degreasing over other cleaning methods because it is a highly effective way to clean optical elements and address associated production concerns.
A vapor degreasing machine is a closed-loop system. Used within it is a specialized low-boiling, nonflammable fluid as the cleaning agent. The cleaning fluid constantly repurifies and recycles for hundreds of cycles before it needs refreshing. This limits fluid use, reduces waste generation, and lowers disposal costs.
The machine contains two chambers: the boil sump and the rinse sump. In the boil sump, the cleaning fluid heats the fluid into vapors. The warm vapors rise upward in the machine and are then trapped by a layer of refrigeration that creates a temperature inversion. The vapors then condense back into liquid form and return into the cleaning machine to be reused.
Once cleaned, a batch of optical devices is mechanically transferred to the internal rinse sump for final rinsing in a pure, uncontaminated fluid. The devices come out clean, dry, spot-free, and immediately ready for the next step in the process (see Fig. 2).Cleaning fluid effectiveness
When using a vapor degreaser to batch-clean optical elements, it is important to select a cleaning fluid that covers all the requirements needed to make the process successful and efficient. Using a sustainable cleaning fluid is an important factor. If the incorrect solution is selected, it jeopardizes the goal of effective, sustainable cleaning.
The cleaning fluids used within the vapor degreasing system have multiple chemical properties that are advantageous to photonic-element cleaning. However, it is important to look for certain features. A cleaning fluid should have a low surface tension and a very low viscosity; these properties help to wet every surface to remove contaminant and residue. It should also have high solvency to enable rigorous surface cleaning. It also must be heavy and dense, to help dislodge dust and lift away buffing compounds or other particulate from the surfaces. Vapor degreasing fluids also ensure a spot-free finish for parts that must meet stringent performance criteria. And because the cleaning fluid is engineered for specific photonic applications, delicate parts are easily cleaned and dried without damage.
Materials compatibility
Sensitive optical components are typically damaged if inappropriate cleaning fluids are used. For instance, plastic optics are easily softened by acetone, and some hygroscopic crystal materials may be dissolved through contact with water. Many vapor degreasing fluids have excellent materials compatibility and can be used on glass, fused silica, crystals, plastics, and metals (see Fig. 3).Sustainable solution
Vapor degreasing cleaning processes are subject to an increasing number of environmental regulations. It is not just the cleaning fluid itself that is scrutinized, but also the method in which it is disposed of. Vapor degreasing effectively addresses both of these concerns.
It is important to consider the long-term environmental impact in fabricating operations. The cleaning fluid must perform reliably and also be environmentally progressive. Look at the cleaning fluid’s safety sheets for this information. Does it include any potentially harmful or environmentally damaging substances like trichloroethylene (TCE) and n-propyl bromide (nPB)? If so, opt for a more environmentally sound version—for example, a cleaning fluid based on hydrofluoroether (HFE) or hydrofluoroolefin (HFO) formulations.
Many modern vapor degreasing chemistries are ozone-friendly and comply with environmental directives, including North American NESHAP standards and European F-Gas and REACH (Registration, Evaluation, Authorisation and Restriction of Chemicals) legislation. Importantly, they offer improved eco-friendly properties without compromising their performance.
Another environmental benefit of vapor degreasing fluid is its capacity for recycling. It is used repeatedly for hundreds of cycles before it needs refreshing or replacing (see Fig. 4). Additionally, it concentrates the soil and contaminants as it works, minimizing the amount of hazardous waste generated. Other cleaning processes such as aqueous cleaning require wastewater filtering, distillation, deionizing, and osmosis prepping for disposal. Also, vapor degreasing does not use precious natural resources like water or large amounts of energy to clean. They instantly remove water from surfaces without energy-wasting heat or air knives. Therefore, it helps conserve water and reduces fossil-fuel consumption, resulting in a lower total carbon emission and less greenhouse-gas output.Putting worker safety first
Worker safety is a priority for any fabricator. So, it is critical to choose a vapor degreasing cleaning fluid that is safe to use. When studying the safety sheets for any environmental implications, also look at whether the cleaning fluid is nonflammable and what the toxicity rating is.
The threshold limit value (TLV) is a commonly used rating for toxicity and is measured in parts-per-million (ppm). Higher values, those approaching 1000 ppm (the highest rating possible), indicate a safer cleaning fluid, while lower numbers specify a greater risk. A cleaning fluid that necessitates greater scrutiny has a TLV of 10–25 ppm. It’s best to use a cleaning fluid with a TLV of 200 or higher.
New sustainable cleaning fluids used in a vapor degreaser have impressive worker exposure limits. The permissible exposure limit (PEL), relating to the designated time limit that workers should be exposed to a chemical for sustainable fluids, is about 200–250 ppm. Compared with TCE, which has a 100 ppm PEL or nPB that is rated at just 0.1 ppm, sustainable cleaning fluids are significantly better for the safety of exposed workers.
Cost implications
Of course, having a cleaning process that addresses worker safety and environmental concerns is good. But if it is not cost-effective, it is just not worthwhile.
Vapor degreasing is low on energy consumption, which saves money. The cleaning fluid is also re-used many times without the waste disposal associated with other cleaning methods—another cost saving. It cleans quickly and effectively, and optical components come out of the vapor degreaser clean, dry, spot-free, and ready for the next stage in the production process, increasing the overall throughput and productivity.
Additionally, in many cases the modern cleaning fluids are used in existing equipment with the same operating methods. After emptying and cleaning the vapor degreaser of the previously used fluid, many of the replacement cleaning fluids can be “dropped in” to the machinery without a significant change to the cleaning process.
Cleaning is a critical step to achieve quality optical components. The most efficient and sustainable solution is through vapor degreasing and highly advanced cleaning fluids. This process is a cost-effective way to not only ensure optical components are perfectly clean, but also to tackle worker safety, regulatory requirements, and environmental concerns.
Venesia Hurtubise is a Technical Chemist at MicroCare, New Britain, CT; e-mail: [email protected]; microcare.com.