Most laser beams have a Gaussian irradiance profile, although it can be beneficial to use a non-Gaussian beam in certain applications. The irradiance cross-section of Gaussian beams decreases symmetrically with increasing distance from the center; in contrast, flat-top beams, also known as top-hat beams, maintain a constant irradiance value through a beam cross-section, providing a consistent intensity across the target of a laser system (see Fig. 1). This results in more accurate and predictable results in applications such as semiconductor wafer processing, other materials processing, and nonlinear frequency conversion with high-power beams. Compared to Gaussian beams, flat-top beams can generate cleaner cuts and sharper edges in processing systems, but generating a flat top adds additional system cost and complexity. Understanding the benefits of flat-top beam profiles and the different methods for generating them will help laser system integrators better understand what beam profile is the best for their application.
Properties of Gaussian beams
Gaussian lasers are more common and cost-efficient than laser sources with other beam profiles. Most high-quality, single-mode laser sources emit a beam following a low-order Gaussian irradiance profile, which is also known as the TEM00 mode. Lower-quality sources will have some level of other laser modes present as well, but it is often assumed that lasers have an ideal Gaussian profile to simplify system modeling. If a Gaussian beam and flat-top beam have the same average optical power, the Gaussian beam will have a peak irradiance twice as large as that of the flat top beam. As a Gaussian beam propagates through an optical system it retains a Gaussian irradiance profile, even if the peak value or beam size change. This means that Gaussian beams remain constant under transformations.
What’s wrong with Gaussian beams?
Gaussian laser profiles have several disadvantages, such as the low-intensity portions on either side of the usable central region of the beam, known as “wings.” These wings typically contain energy that is wasted because it is at a lower intensity than the threshold required for the given application, whether it is materials processing, laser surgery, or another application where an intensity above a given value is needed (see Fig. 2). The wings of a Gaussian beam may also damage surrounding areas outside of the target area, extending the heat-affected zone. This is unfavorable in situations like laser surgery and precise materials processing where high accuracy and minimized damage to surrounding areas are prioritized. Features formed using a Gaussian beam won’t have particularly smooth edges because of this effect, which reduces system accuracy.
Why use a flat-top beam?
The lack of wings and steeper edge transitions in flat-top beam profiles result in more efficient energy delivery compared to Gaussian beams, as well as smaller heat affected zones.2 Figure 2 reveals how the energy of a flat-top beam is more clearly contained in a given area than that of a Gaussian beam. Any features etched, welded, or cut using a flat-top beam will be more accurate and there will be less damage to surrounding areas.This primary advantage of flat-top beams makes them beneficial for a wide range of different situations. In laser-induced damage threshold (LIDT) testing and other metrology systems, the well-defined and consistent irradiance profile of flat-top beams minimizes both measurement uncertainty and statistical variance. Flat-top beams are also advantageous in many fluorescence microscopy, holography, and interferometry systems.3
One method for evaluating how close an actual laser beam is to a perfect flat-top profile is to analyze its flatness factor (Fη), which is calculated by dividing the average irradiance value by the beam’s maximum irradiance value as described in ISO 13694.2
What are the disadvantages of a flat-top beam?
Flat-top beams are not perfect or ideal for all situations. They are not as cost-efficient as Gaussian laser beams because an additional beam-shaping assembly is needed to convert a laser’s Gaussian output into a flat-top profile. The assembly can either be built directly into the laser source or used externally outside of the laser at some other point in the system. These beam-shaping components are dependent on input beam size and sensitive to x-y alignment. In addition, flat-top laser beam profiles, unlike Gaussian beam profiles, do not remain constant under transformations. This means that an incident flat-top beam profile will not hold a flat-top shape as the beam propagates through the system. The flat-top beam profile will eventually evolve into a profile resembling an Airy disk distribution.
How do I achieve a flat-top beam?
When a flat-top beam profile is desired but the system is very cost-constrained and performance does not have to be incredibly high, Gaussian beams are sometimes physically truncated using an aperture to form a pseudo-flat-top profile. This cuts off and wastes the energy in the Gaussian beam’s wings and does not flatten the central portion of the beam, but this method may be useful when maintaining low cost is a primary factor.
For higher-performing systems requiring a more efficient use of costly laser energy, beam-shaping assemblies are used to transform Gaussian beams into flat-top beams. There are several different types of beam shaping assemblies including refractive, reflective, holographic, and diffractive designs. Refractive beam-shaping assemblies use field-mapping aspheric or freeform lenses and other refractive components to manipulate the phase of a beam (see Fig. 3). They benefit from uniformity in the distribution of intensity and flat phase fronts. The amplitude and phase of incident beams are manipulated by passing through optical elements in a Galilean or Keplerian lens assembly. This process is typically highly-efficient (>96% throughput) and wavelength-independent within the range of the assembly’s design. Refractive beam shapers producing collimated flat-top beams are beneficial for holography and microscopy systems, especially those operating over long distances.Diffractive beam shapers, on the other hand, utilize diffraction instead of refraction to change an incident laser beam’s irradiance distribution. An etching process forms a specific micro- or nanostructure in a substrate, forming a diffractive element. The effects of the element and wavelength range are usually dependent on the height and zone spacing of the structure. Because of this, diffractive optical elements must be used at their design wavelengths to avoid performance errors. Diffractive beam shapers are more dependent on divergence, alignment, and beam position than refractive designs. However, diffractive beam shapers are particularly advantageous in space-limited laser systems because they are often composed of a single diffractive element instead of multiple refractive lenses. Diffractive beam shapers can form both flat-top and Airy disk beam profiles.
Laser beam integrators, or homogenizers, are another type of beam-shaping assembly. They are composed of an array of multiple lenslets, or small lenses, that separate the incident beam into smaller beams, or beamlets. A focusing component lens then superimposes the beamlets at the target plane. The final output profile is typically the sum of the diffraction patterns determined by every lenslet in the array. They can transform an incident Gaussian beam into a homogenized flat-top profile from incident Gaussian beams. However, these systems often experience random irradiance fluctuations, resulting in the output beam profile not being perfectly flat. A comparison of the different beam shapers discussed above can be found in the table.Flat-top beams are beneficial for a wide variety of laser systems where precision and efficiency are prioritized over minimizing cost. With refractive, diffractive, and other beam-shaping designs on the market today, laser system integrators have many available options when selecting a beam shaper. The table provides some useful rules of thumb, but contact your optical component supplier for more guidance on choosing the best beam shaper to make the most of your laser system.
REFERENCES
1. A. Laskin et al., Proc. SPIE, 9887, 98872E (Apr. 27, 2016); doi:10.1117/12.2217927.
2. See iso.org/standard/72945.html.
3. M. Eryilmaz et al., Cancers, 10, 1 (Jan. 22, 2018); doi:10.3390/cancers10010025.
4. Y.-J. Hung et al., J. Vac. Sci. Technol., 35, 3 (Apr. 11, 2017); doi:10.1116/1.4980134.
5. A. Laskin et al., Proc. SPIE, 9950, 995002 (Sept. 27, 2016); doi:10.1117/12.2235712.
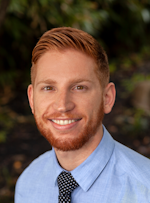
Cory Boone | Technical Marketing Manager, Edmund Optics
Cory Boone is the Technical Marketing Manager at Edmund Optics’ Barrington, NJ, USA office. He is responsible for managing the creation of technical marketing content, including application notes, published articles, web copy, email campaigns, video scripts, trade show materials, case studies, and other marketing literature. He plans the company’s technical content strategy and acts as the technical voice of the marketing department. Cory is also active in educational outreach and spreading general awareness of the optics industry. He received a B.S. in Optical Sciences and Engineering along with minors in Math and Material Science Engineering from the University of Arizona.
Kristina Kaszei | Product Support Engineer, Edmund Optics
Kristina Kaszei is Product Support Engineer at Edmund Optics (Barrington, NJ).