Automotive Photonics: Laser-diode-based scanner paves the way for autonomous vehicles
Most drivers in the U.S. are aware that this country's transportation infrastructure is in need of substantial repair and improvement. In fact, the American Society of Civil Engineers recently rated our roads with a grade of "D."
Rapid developments in autonomous-vehicle technology have highlighted the need for road improvements, particularly the requirement for consistent, easily visible pavement markings—without these, it's difficult for autonomous vehicles to know exactly where they are on the road. In one notorious example, at a failed demonstration of self-driving car technology at the 2015 Los Angeles Auto Show, Volvo's North American CEO, Lex Kerssemakers, exclaimed, "It can't find the lane markings! You need to paint the bloody roads here!"
Nighttime visibility of pavement markings, in particular, is enhanced by embedding small glass retroreflecting "cat's-eye" spheres in the paint or thermoplastic material used to create markings. However, there are a number of process variables, including sphere diameter, sphere-placement density, and the depth to which the beads are embedded, which affect the precise level of marking retroreflectivity.
The color of the reflected light can also differ between locales depending upon the particular pigments used, and how well the paint bonds to the beads. In the worst case, it's possible that drivers will not be able to easily distinguish yellow lines from white lines at night. This has become increasing problematic since the elimination of lead chromate in paint, which delivered a highly saturated yellow color.
As a result, both federal and state governments have developed, or are developing, standards for pavement-marking retroreflectivity. In fact, the U.S. Congress mandated that there should be standards for the minimum retroreflectivity for all road markings about 25 years ago. But, they have still yet to set the actual values for those standards.
One reason that specifications for pavement marking visibility have been so long in coming is that there was no practical way to measure it properly. The traditional measurement technique involved manually placing a xenon or tungsten-based lamp instrument on the pavement and taking a handful of readings at prescribed intervals (typically 10 to 20 readings per mile) along a roadway. This method involves lane closures and traffic control, making it both hazardous to personnel and expensive.
More-sophisticated vehicle mounted measurement systems based on tungsten and xenon sources have also been recently introduced. These suffer from significant limitations, including an inability to correct for ambient lighting conditions (such as sunlight or oncoming headlights) and the inability to measure the color of returned light.
Road measurement via laser scanning
A new laser-diode-based scanning technology has been developed that performs highly accurate measurements of pavement markings at a 400 Hz sampling rate. For example, at a speed of 60 mph, this technique delivers a measurement every 2.6 in. The system can be mounted on a car using vacuum cups and simply driven along the road (see figure).
Developed by Gamma Scientific (San Diego, CA), the system, called the RoadVista Laserlux G7 (LLG7), incorporates between one and three laser diodes in various combinations of red, green, blue, or infrared output wavelengths. Within the instrument, the output of these lasers is combined to be essentially collinear and then directed to a galvanometer scanner, creating a scan line that is then projected out on to the roadway.
The lasers themselves are pulsed in synchronization with the scanning mirror so that they are only on when it sweeps in one direction, but not for the return. However, the detection system measures returned light from both the "on" and "off" scan phases, and then uses the "off" phase to establish an ambient light baseline. Together with narrowband filters, this enables elimination of stray light and permits measurements at any time of day or night.
The angle at which the scanned beam hits the road surface is critical, as retroreflection is very sensitive to incoming illumination angle. To eliminate the need for precision alignment by the operator, the system uses onboard sensors that automatically adjust height and tilt to dynamically maintain the necessary measurement geometry.
The system acquires reflectance data, along with GPS coordinates, and stores this on a flash drive. The use of red, green, and blue lasers enables marking color measurement in CIE color coordinates. Alternatively, the utilization of an infrared laser enables measurements of the road the way most self-driving cars will see it. In addition, the system can count and measure retroreflective pavement markers (the small trapezoidal reflectors embedded on many roadways) and identify missing or broken ones.
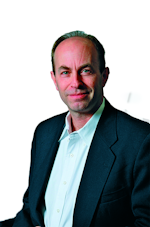
John Wallace | Senior Technical Editor (1998-2022)
John Wallace was with Laser Focus World for nearly 25 years, retiring in late June 2022. He obtained a bachelor's degree in mechanical engineering and physics at Rutgers University and a master's in optical engineering at the University of Rochester. Before becoming an editor, John worked as an engineer at RCA, Exxon, Eastman Kodak, and GCA Corporation.