MATERIALS PROCESSING: Reflective optics minimize 'focus shift' in high-power materials processing
One of the challenges in any materials-processing application that uses high-power, high-brightness lasers (kilowatt power levels) is "focus shift"—the shift in focus position of a laser beam at the workpiece due to thermal lensing effects caused by nonuniform heating of the beam-delivery optics and coatings, among other factors. Not only does focus shift change the beam diameter at the workpiece, but it also causes changes in the relative angle of the focused beam as well as the beam's power distribution, making it more Gaussian than the typical top-hat profile.
But by studying the properties of optical materials and the various methods for laser-beam delivery, scientists at Trumpf (Ditzingen, Germany and Plymouth, MI) have developed an optimized beam-delivery system that makes use of reflective optics to minimize focus shift.1
Configuration matters
Because any optical component through which a high-power laser beam passes is subject to thermo-optic effects, the optical path between the output laser beam and the work surface should have as few absorptive components as possible. For example, in a straight-through or 0° welding head used with a camera, the laser beam passes through a bending mirror that reflects the camera image but transmits the beam through two absorptive surfaces and the absorptive bulk mirror medium. Alternatively, in a 90° welding head, the bending mirror reflects the laser beam and transmits the camera image, sending the laser beam through just one reflective surface for 45% less thermal focus shift than the straight-through configuration, according to measured data.
To minimize the temperature gradient and subsequent thermo-optic effect, it is also important to maximize the beam "fill" of the optical elements. In addition, the cover slide at the output of the beam-delivery optics should be kept as clean as possible—even slight spatter from processing or dust and fingerprints can cause a significant increase in thermal focus shift. It is recommended that cover-slide monitors (photodiodes that analyze reflected signal power) be used in the optical setup in order to track the cleanliness and quality of this critical element.
Reflective optics
Quantitatively, antireflection coatings can absorb 0.12% of a laser beam's power, or up to 80 W per surface for a 16 kW beam. In a straight-through or 0° welding head, the presence of ten absorptive surfaces from five optical components (fiber-protection sleeve, collimating lens, bend mirror, focus lens, and cover slide) can waste 800 W of heat in a 16 kW system.
To reduce the presence of absorptive surfaces, Trumpf developed a reflective focus optic (RFO) that improves over both straight-through 0° and even 90° materials-processing heads (see figure). The RFO consists of two mirrors. The laser beam is transmitted through a fiber-optic cable and diverges as it exits the fiber. Instead of using a transmissive collimating optic to collimate the beam and a transmissive focus lens to focus the beam, the RFO incorporates a flat mirror and a focus mirror. The optical element for camera integration in conventional transmissive focus units is eliminated by using a special transparent focus mirror. Although a cover slide is still used with the RFO, cover-slide monitoring is a standard option and is recommended at powers around 8 kW and higher.
REFERENCE
1. D. Havrilla et al., "Latest Research Results with High Power Solid State Optics with Minimized Focus Shift," ICALEO 2010 Conf., Session LMP1, paper 103, Anaheim, CA (Sept. 27, 2010).
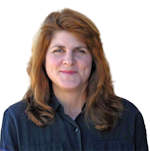
Gail Overton | Senior Editor (2004-2020)
Gail has more than 30 years of engineering, marketing, product management, and editorial experience in the photonics and optical communications industry. Before joining the staff at Laser Focus World in 2004, she held many product management and product marketing roles in the fiber-optics industry, most notably at Hughes (El Segundo, CA), GTE Labs (Waltham, MA), Corning (Corning, NY), Photon Kinetics (Beaverton, OR), and Newport Corporation (Irvine, CA). During her marketing career, Gail published articles in WDM Solutions and Sensors magazine and traveled internationally to conduct product and sales training. Gail received her BS degree in physics, with an emphasis in optics, from San Diego State University in San Diego, CA in May 1986.