METAMATERIALS: Invisibility cloak without anisotropy doesn't quite do its job
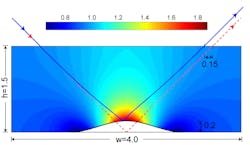
Scientists at the Massachusetts Institute of Technology (MIT) have determined that a recently popular approach to designing an invisibility cloak doesn't produce quite what was intended.1
While theory allows the design of optical invisibility cloaks that would perfectly hide things like cars, houses, and scientists from view, practical considerations make these designs virtually impossible to build. Such cloaks would be made from optical metamaterials, which are made up of structural components smaller than a wavelength of light, all of which must stay in alignment to each other to subwavelength-scale precision; for a cloak the size of a person, this would be an unattainable feat. In addition, large metamaterial cloaks would unavoidably absorb and scatter some of the light, defeating their purpose.
Making things easier
So cloaking designers have simplified things in two ways. First, they are looking mainly at very small cloaks a few wavelengths in size; this makes the cloaks easier to build. Second, they are interested in certain special cases that allow them to make cloaks from simpler materials. Arbitrarily complex cloaking arrangements require the use of optically anisotropic metamaterials, which have the strange property that the phase front of the light traveling through it can be designed to be nonperpendicular to the direction of the light's travel. Anisotropic metamaterials are the most difficult to construct. In contrast, certain simplified cloaking arrangements may get by with the use of optically isotropic metamaterials instead, or even gradient-index dielectrics.
In one of these special cases, researchers give up on trying to hide an arbitrary object, and instead settle for trying to hide a bump on a perfectly reflecting mirror. The bump must be simple in shape, smoothly varying in height, and also with perfect reflectivity. The mirror and bump can then covered with a transparent isotropic cloaking layer that has a flat outer surface and a refractive index that varies in a way that, it is hoped, renders the bump invisible.
Seeing the result
What the MIT scientists have determined is that the jump from an anisotropic to an isotropic cloaking material comes at a cost. While an optically anisotropic material permits perfect cloaking of the mirror bump, a cloak made from an optically isotropic material only partially cloaks the bump: Although the phase fronts of a light beam reflected at an angle from the bump accurately mimic what would result if there were no bump, the light beam itself is laterally shifted (see figure). In one example consisting of a bump 0.2 units high cloaked with an isotropic gradient-index material (with refractive index varying between just under 1 to about 1.4), a ray reflected at an angle of 45° is shifted laterally by about 0.15 units—so the lateral shift of the angled ray is almost as great as the height of the bump being cloaked. (Because the refractive index dips just under 1, the cloak must still be made of metamaterial.)
So, to perfectly cloak a bump on a mirror, an optically anisotropic metamaterial remains a necessity, say the MIT researchers. As for more interesting cloaking devices that are designed to hide something other than a small reflective bump, there are the other obstacles as well, such as high absorbance, narrow transmission bands, and insufficient rigidity. Think of the articles in the general science and technology media that have played up the idea of a large-scale optical invisibility cloak with little or no explanation of the difficulties involved—and imagine how many people might think a supple (perhaps machine-washable) invisibility cape is, as a result, just around the corner.
REFERENCE
- B. Zhang et al., http://arxiv.org/abs/1004.2551, Apr. 15, 2010.
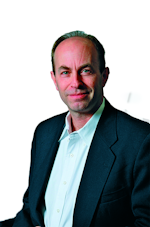
John Wallace | Senior Technical Editor (1998-2022)
John Wallace was with Laser Focus World for nearly 25 years, retiring in late June 2022. He obtained a bachelor's degree in mechanical engineering and physics at Rutgers University and a master's in optical engineering at the University of Rochester. Before becoming an editor, John worked as an engineer at RCA, Exxon, Eastman Kodak, and GCA Corporation.