PHOTOVOLTAICS: Microconcentrators boost efficiency of concentrator solar cells
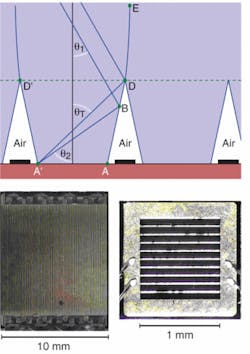
While the most heavily publicized approaches for raising the efficiency of photovoltaic solar cells usually involve improving semiconductor materials or fabrication processes, another effective approach is developing better concentrating solar optics. Much effort has gone into shaping large mirrors and lenses to put the maximum amount of sunlight on small, highly efficient solar cells that are created especially for high concentration ratios. Now, researchers at Ben-Gurion University of the Negev (Be’er-Sheba, Israel) and the Jerusalem College of Technology (Jerusalem, Israel) have created what they call all-dielectric microconcentrators (ADMCs), which, made of glass, lie atop the small solar cells themselves.1 The purpose of the ADMCs is to take light that would normally strike the grid of metal electrical “fingers” on the tops of the cells (and thus be wasted) and, via total internal reflection, route it directly to the cell’s active surface (see figure).
Choosing the width of the metal fingers on a concentrator solar cell involves a tradeoff: make them wider and their electrical resistance drops, boosting electrical efficiency; make them narrower and they cover less of the cell’s area, boosting sunlight-collection efficiency. But placing properly designed microconcentrator optics adjacent to the cell eliminates this tradeoff, allowing low resistance and high collection efficiency at the same time. What the Israeli researchers have done is create a simple microconcentrator design that is also highly efficient, due to its form as well as the fact that it is bonded directly to the cell, eliminating an optical reflection. In addition, the all-glass construction makes them resistant to yellowing.
While the researchers have modeled their ADMC designs, they have not yet fabricated them. The microfabrication techniques that look the most promising are direct-glass microfabrication procedures and glass sol-gel materials that can create the master for replication, according to Jeffrey Gordon, one of the researchers.
Only simple grid geometry needed
The ADMC consists of many parallel solid-glass troughs bonded at their narrower bottom ends to the solar cell. The trough-profile shapes are either combinations of parabolas and straight lines, or just straight lines (the details depend on variables such as the concentration ratios of the ADMCs). The grid-line spacing for a typical concentrator cell is about 100 µm. More-complex nonparallel grid geometries also exist, designed to capture as much electricity as possible with the lowest series resistance; but because the ADMC allows for greater metal coverage, it also enables the use of the simpler, less-expensive parallel-grid geometry, according to Gordon.
“Our ADMC will work with essentially any of the macroconcentrators used in concentrator photovoltaics,” says Gordon. “These range from simple Fresnel lenses to paraboloidal dishes to the more-sophisticated optics such as those we developed for SolFocus (Mountain View, CA). Furthermore, the macroconcentrator can either be separate from the ADMC, meaning that sunlight exits the macroconcentrator into air before reaching the ADMC, or optically coupled to the ADMC via a dielectric. Because the ADMC is tailored to the solar cell itself, the size, concentration, and location of the macroconcentrator are immaterial.”
Typical concentrator solar cells tailored to flux levels of hundreds of suns (for example, 200 to 500 suns) have a metallization coverage of about 12%, notes Gordon. “So, first, that means that a net gain of 12% (relative) would be realized just from the optics (please note, for nontrivial reasons, our ADMC incurs an incremental optical loss of essentially zero),” he says. “In addition, based on our simulation results, an additional 3% efficiency gain (relative) would be achievable from the reduction in the cell’s effective series resistance at the target flux levels. Hence, the overall or net gain would be about 15% (relative).”
The two Israeli universities have a provisional patent on the technology and would like to license it. Two commercial outfits have already expressed interest, says Gordon.
REFERENCE
1. O. Korech et al., Optics Lett.32(19) Oct. 1, 2007.
Editor’s note: For more on photovoltaics, see “Solar Electricity: its time has come,” p. 65; “Photovoltaics reach record efficiency,” p. 73; and “Is solar energy ready for take-off?” p. 132.
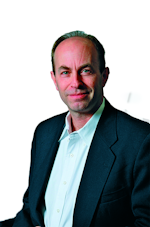
John Wallace | Senior Technical Editor (1998-2022)
John Wallace was with Laser Focus World for nearly 25 years, retiring in late June 2022. He obtained a bachelor's degree in mechanical engineering and physics at Rutgers University and a master's in optical engineering at the University of Rochester. Before becoming an editor, John worked as an engineer at RCA, Exxon, Eastman Kodak, and GCA Corporation.