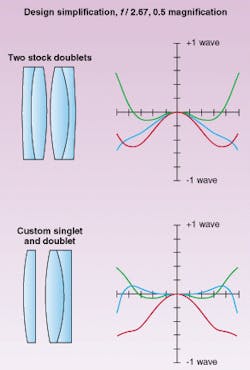
Many engineers consider only catalog optics when putting together a new design. This may stem from overestimating the cost and lead time of custom components, underestimating the true cost of stock components, not appreciating the advantages of custom components, or a combination of all three—particularly in the case of infrared (IR) systems where stock components have been optimized for the visible spectrum. Conventional wisdom in choosing catalog over custom optics is moving further away from actual reality, however, as advances in computer-aided lens design and manufacturing techniques have cut the cost and lead time associated with custom optical components.
Catalog optics still provide a valuable resource and excellent solution in many cases. As a custom optics supplier, I keep the catalogs of prominent suppliers by my desk and frequently recommend stock components to people calling up to have optics made. Ultimately, the best advice in any successful design process is to consider all of your options.
For example, a university customer I worked with recently needed an achromat to work from 0.9 to 1.7 µm. The closest stock achromat had a 108-mm focal length and a 30-mm diameter. This lens was well corrected in the visible with about one wave of secondary chromatic aberration. In the IR range of interest, primary chromatic aberration was under-corrected by 10 waves (see Fig. 1). With judicious glass choices and reoptimizing for the infrared, a better design was achieved with the primary chromatic aberration balanced. (Due to the extended wavelength range, the secondary color is significant at 1.4 waves, but is still seven times better than the visible doublet). The design time to do this was less than 20 min, including test-plate fitting, and only common glasses were used.
In this example the problem was the broad wavelength range. Now, suppose the lens is to be used at a single wavelength, say 1.064 µm. Here the effect is less severe but may be of concern for critical systems. The IR doublet shown in Figure 1 was only marginally better than the visible version with 0.18 vs. 0.25 wave of spherical aberration on axis. With about a dozen mouse clicks and five key strokes, however, the IR lens design was reoptimized for the single wavelength, yielding a design error of 0.02 wave.
Among the numerous trade-offs to consider in deciding between custom and stock optics, the first is probably your own design time. Many of the lens designers I talked with in preparing this article stated that it always takes longer to design using catalog optics because they start out allowing the design to vary freely, then they replace the optimized components with the nearest catalog components they can find. Chances are, choosing and reanalyzing the catalog optics will take even more time than the initial design. Of course, the more complex the optical system is, the more this will come into play.
Fast computers and design software
With modern lens-design software and current computer speed, optimizing a lens system for best performance is relatively easy. The first lens-design programs for desktop computers came out in the early 1980s. These traced light rays through a lens system at four surfaces per second. On my 450-MHz computer using Zemax (Focus Software; Tucson, AZ), the speed is 1.5 million surfaces per second. This means that the optimization of simple systems (that is, the tweaking of radii to minimize aberrations) takes only a few seconds of computer time. For example, when a customer called me recently about a simple collimating lens, I was able to compare for him a stock BK-7 singlet, a stock doublet, a custom high-index singlet, and a custom doublet in about five minutes. I was able to make a performance comparison while talking on the phone, and the design cost to the customer was zero.
Computer speed has also made test-plate fitting very economical. This is the process in which an optimized design is reoptimized to match the existing tooling of a given company, reducing tooling cost. This was actually the subject of my master's thesis in 1983, in which I concluded that a well-chosen set of 400 radii was sufficient for nearly all designs. At that time, the process of test-plate fitting could account for a high percentage of the cost of simply making new test plates. Today, major lens-design programs such as CODE V (Optical Research Associates; Pasadena, CA) and Zemax include extensive libraries of manufacturer's test-plate lists, as well as powerful test-plate-fitting routines that do this job automatically.
Some designers pointed out that a custom design can reduce long-term manufacturing cost by reducing the total number of lens elements needed. As a quick exercise, I looked at using two catalog doublets to form a 2:1 finite conjugate imaging lens. This is a common technique in which the doublets are placed back to back (see Fig. 1). The doublets selected were 240- and 120-mm focal lengths, 30-mm diameter. Because each doublet is essentially used at infinite conjugates, as they were designed, the pair is well corrected, as shown in the ray fan plot.
From this starting point, I changed one doublet for a singlet and ended up with the design shown in Figure 2, consisting of a plano-convex BK-7 singlet and a doublet, the performance being as good as the two-doublet design. Note that for the prototype, a close stock singlet can be found, so only the custom doublet would be needed. In production quantities, where custom lenses will be made anyway, the singlet will cost about one-third of what the second doublet would have cost, cutting the total cost of the optics by a one-third. Further analysis showed that performance from a stock singlet used with a stock doublet would be poor because the system would be under-corrected for chromatic aberration.
Computers have also aided custom optics through CNC manufacturing by reducing the cost and lead time of short-run production. CNC manufacturing reduces tooling cost by eliminating the need for specific grinding laps for each lens radius (see "Lead-time lessons").
Cost factors to consider
Consider the cost of your own time. It takes time to find the right stock lenses and fit them into your system. The burdened labor rate of an engineer can be quite high.Take the overall system cost into account. Doubling the cost of the optics for a 20% improvement in performance sounds high, but if the optics comprise 10% of the total system cost, then system cost is really up only 10%, and the added expense sounds like a bargain. For example, consider cylindrical lenses available from various manufacturers for concentrating the output of fiberoptic lightline illuminators. These stock optics consist of acrylic rod lenses, which are relatively inexpensive and low performance. I have been working with a company that needed a higher-quality system to yield greater light concentration. This led to designing two systems of different focal distance. Figure 2 compares these two systems with the stock (acrylic rod) lens. The cost of the custom optics is about twice as high as the cost of the acrylic lens, but the light concentration is at least double. Compared to the overall system cost, it is a bargain.
If your system will go into any type of production quantity, you will probably reach a point where custom optics are cheaper. For cylindrical optics, this may be just a few pieces. For spherical lenses, it may be in the range of 50 to 200 pieces. An engineer gave me an example of a savings of 50% when his company switched from purchasing a catalog lens in quantities of 500 to having it custom made by a domestic supplier. Any money saved on the prototype using catalog lenses had long since been lost. You need to keep in mind that the economy of catalog optics comes from allowing the buyer to purchase a few pieces from a much larger production run, which more than offsets the cataloging cost. If you are buying the whole production run, there is no savings.
Amortizing costs
You will also want to consider the cost of the prototype amortized over the life of a product. One engineer put it, "We are in for the long haul; with us it is 'pay now or pay later.' If they start with catalog optics, they end up needing to redesign for production, which costs more money." Another person pointed out that one must be careful even with a "quick proof of concept" prototype. Unless the design and quality of the optics are sufficiently good, you prove nothing, or may even be led down the wrong path entirely.
Then there is your ability to control tolerances. For OEM applications, parameters such as focal length often need to be held to a tight tolerance to minimize adjustments during assembly. Stock components typically carry loose tolerances for easy manufacture. Also, don't assume every catalog lens is in stock. Catalog houses carry a very large and diverse inventory but they can't always have an unlimited supply of everything.
And finally, when you are calculating the real costs of choosing custom rather than catalog optics, be sure you know your optics supplier, whether a catalog or custom house. Consider the service you get when you need questions answered. Ultimately, both catalog and custom optics are vitally important. Catalog optics can potentially cut cost and lead times over custom optics. However, the designer should be careful to take all cost and performance factors into account.
Lead-time lessons
What should the optics user expect in regards to lead time? My shop is probably typical for custom suppliers, and for typical lens elements, say between 1/4-in. and 4-in. diameter, moderately tight tolerances, available glass types, and without exotic coating requirements, I would classify lead times for short-run production as follows:
- 9 weeks or more: we are grateful for the long comfortable lead time, which minimizes production cost.
- 7-8 weeks: normal lead time.
- 5-6 weeks: normal rush lead time, which we can generally do.
- 3-4 weeks: rush lead time, which, depending on our workload, may require an expediting premium.
- 1-2 weeks: extreme rush, which, depending on parts to be made and shop workload, will require an expediting premium. This would be a good time to use off-the-shelf optics if at all possible.
About the Author
Cody Kreischer
President (former), Kreischer Optics
Cody Kreischer formerly served as president of Kreischer Optics Ltd., 906 N. Draper Rd., McHenry, IL.