For many years, component manufacturers in the machine-vision industry have leveraged consumer, computer, and broadcast technologies to lower the cost of their products. For example, frame-grabber vendors have used broadcast-compatible standards and devices, and smart-camera vendors have used computer-network standards such as Ethernet, USB, and FireWire in their designs. While many of these cameras incorporate consumer lenses, those developed for machine-vision applications require optics that are more sophisticated.
In the course of developing electronic-focus (EF) lenses for their consumer cameras, for example, engineers at Canon (Tokyo, Japan) developed an interface standard that allows Canon camera bodies such as the Canon 16.7‑megapixel EOS 1Ds Mark II to electronically control functions such as autofocus and aperture. This electronic-mount system has none of the abrasion, play, slow response, and diminished precision caused by lever operation. In addition, the lens’ built-in microcomputer can even warn of malfunctions through the camera’s LCD readout. Numerous types of Canon lenses support the EF standard, and they can be purchased independently from consumer camera stores.
Canon is unwilling to license its protocols to third-party manufacturers and so a number of lens, lens-controller, and camera manufacturers have reverse engineered the standard and incorporated it into their own products. But there is a drawback to reverse engineering. If a company figures out how their products can work flawlessly with Canon products, Canon can alter its future products in such a way that older third-party items no longer function correctly.
Despite these potential problems, using a computerized lens with electronic aperture and autofocus is very appealing to integrators of machine-vision systems and their suppliers. Birger Engineering (Boston, MA) and Imaginant (Pittsford, NY) have both “adopted” the Canon standard in lens controllers and digital cameras for machine vision. Birger Engineering’s EF232 adapter lets system integrators control Canon EF-mount lenses without requiring the use of a Canon EOS camera body. Imaginant’s adaptation of the Canon standard allows control of camera burst capture rate, trigger, and strobe rate, and enables the focus and the aperture of the lens to be adjusted automatically over a Gigabit Ethernet interface.
Standard imagination
As solid-state linescan and area-array imagers grow in format size, however, aligning lenses with camera bodies becomes a challenge. At this year’s International Robots & Vision Show (Rosemont, IL; Sept. 27-29), Edmund Industrial Optics (Barrington, NJ) proposed developing a standard to alleviate this problem. Samuel Sadoulet, director of product development at Edmund, outlined the problems faced by machine-vision system integrators.
“Applications such as flat-panel inspection,” he said, “are dictating the need to deploy cameras with increased resolution. At the same time, the high-throughput of these systems is demanding faster optics and increased signal-to-noise ratios of the cameras themselves. With these demands, the system integrator is presented with a mechanical hurdle when mounting very large format CCD and CMOS linescan and area-array cameras to fast lenses.”
Achieving true alignment can be virtually impossible with ordinary mounts because of the sheer size and often-difficult placement of the CCDs found in large linescan cameras. “Whether such a lens mount should be used,” said Sadoulet, “is directly related to the number of pixels in the imager and the aperture of the lens. Sadoulet proposed a standard mount that would accommodate 2k to 12k × 1-based cameras and remove the burden of aligning optics and imagers.
Such a standard would use a tilt mechanism centered about the imager’s center pixel to accommodate pitch and yaw. With this tilt mechanism, system integrators could take full advantage of the performance of sensor and optics. Better still, because depth of focus would no longer be a concern, increased light throughput of the imaging system would result.
Settling on mechanical or electrical standards such as these-whether borrowed from the consumer world or developed by machine-vision vendors-would provide long-term benefits to the entire machine-vision community, from camera manufacturers to system integrators.
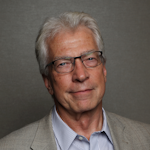
Conard Holton
Conard Holton has 25 years of science and technology editing and writing experience. He was formerly a staff member and consultant for government agencies such as the New York State Energy Research and Development Authority and the International Atomic Energy Agency, and engineering companies such as Bechtel. He joined Laser Focus World in 1997 as senior editor, becoming editor in chief of WDM Solutions, which he founded in 1999. In 2003 he joined Vision Systems Design as editor in chief, while continuing as contributing editor at Laser Focus World. Conard became editor in chief of Laser Focus World in August 2011, a role in which he served through August 2018. He then served as Editor at Large for Laser Focus World and Co-Chair of the Lasers & Photonics Marketplace Seminar from August 2018 through January 2022. He received his B.A. from the University of Pennsylvania, with additional studies at the Colorado School of Mines and Medill School of Journalism at Northwestern University.