3D photonic crystal has electrically pumped gain; makes invisibility cloaking more feasible
Champaign, IL--University of Illinois researchers have created 3D photonic crystals that contain electrically pumped gain elements as part of their structure. Devices made of such photonic crystals could make up for absorptive loss by adding gain, making the structure "lossless" and enabling large-scale volumes that are capable of negative refraction and cloaking.1 To demo their creation, the researchers fabricated an electrically driven 3D photonic crystal LED.
To create a 3-D photonic crystal that is both electronically and optically active, the researchers started with a template of closely packed spheres. They then deposited gallium arsenide (GaAs) through the template, filling in the gaps between the spheres. The GaAs grows as a single crystal from the bottom up via epitaxy. Once the template is full, the spheres are removed, leaving a complex, porous 3-D structure of single-crystal semiconductor. Then they coat the entire structure with a very thin layer of a semiconductor with a wider bandgap to improve performance and prevent surface recombination.
The epitaxial approach eliminates many of the defects introduced by top-down fabrication methods, a popular pathway for creating 3-D photonic structures. Another advantage is the ease of creating layered heterostructures. For example, a quantum-well layer could be introduced into the photonic crystal by partially filling the template with GaAs and then briefly switching the vapor stream to another material.
“The key discovery here was that we grew single-crystal semiconductor through this complex template,” says Paul Braun, a professor of materials science and engineering and of chemistry who led the research effort. (Braun is also affiliated with the Beckman Institute for Advanced Science and Technology and with the Frederick Seitz Materials Research Laboratory at Illinois.) Braun’s group is working to optimize the structure for specific applications.
REFERENCE:
1. Erik C. Nelson et al., Nature Materials (2011), Published online 24 July 2011; doi:10.1038/nmat3071.
Subscribe now to Laser Focus World magazine; it’s free!
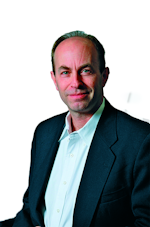
John Wallace | Senior Technical Editor (1998-2022)
John Wallace was with Laser Focus World for nearly 25 years, retiring in late June 2022. He obtained a bachelor's degree in mechanical engineering and physics at Rutgers University and a master's in optical engineering at the University of Rochester. Before becoming an editor, John worked as an engineer at RCA, Exxon, Eastman Kodak, and GCA Corporation.