Wärtsilä (Helsinki, Finland) is introducing augmented reality (AR) and smart glasses in stern tube seals & bearings services, creating a whole new dimension in repair and maintenance operations. The company says digitalization and the rapid development of new technologies is fundamentally transforming the marine industry. New innovations increase efficiency and flexibility; however, these innovations are no longer confined to products and systems, but will also revolutionize marine maintenance services.
RELATED ARTICLE: Engineering the ultimate augmented reality display: Paths toward a digital window into the world
Augmented reality technology can be used for a multitude of different tasks. With the help of AR, a field service engineer, a member of a ship's crew, or shipyard personnel can have immediate access to the global expertise of Wärtsilä Seals & Bearings—regardless of where and when help is needed. The use of AR technology simplifies troubleshooting and speeds up the service and repair of stern tube equipment. It also makes tasks like inspections, alignment measurements, on-site machining, shaft straightening, and newbuilding commissioning much simpler—and faster—than before, with enormous time and cost-saving possibilities.
"Augmented reality can be used to solve complex problems that would otherwise require considerable time to resolve. Smart glasses—equipped with WiFi, Bluetooth, camera and microphone—enable real-time communication with a remotely located Wärtsilä expert who can see and hear exactly what happens on board, in dry dock or in a workshop, no matter how far the customer's installation is," says Thomas Pauly, product manager, Wärtsilä Seals & Bearings Future Technologies.
The person on site can send and receive visual images, listen to the specialist’s advice, and receive written instructions right in front of their eyes on see-through-displays. The expert in Wärtsilä's Expertise Centre can guide the person on site through the actions needed to solve the problem. "It's like having a Wärtsilä service engineer by your side 24/7, with the bonus that this ‘virtual’ service engineer has real-time access to the vast wealth of information and expertise that Wärtsilä has accumulated over the years," Pauly continues.
Currently, Wärtsilä is carrying out pilots with selected customers to establish smart procedures for using AR in a broad range of Seals & Bearings tasks, such as working on installations in remote parts of the world where access is restricted, or onboard ships when there is no GSM signal. With the smart glasses, the person on site can take videos and pictures of a situation and save them on the glasses' internal memory. These files can then be sent to Wärtsilä's Expertise Centre via a satellite connection or via a GSM when there is signal again.
SOURCE: Wärtsilä; https://www.wartsila.com/media/news/31-07-2018-augmented-reality-creates-a-new-dimension-in-marine-maintenance-services
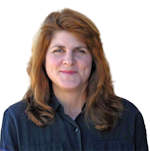
Gail Overton | Senior Editor (2004-2020)
Gail has more than 30 years of engineering, marketing, product management, and editorial experience in the photonics and optical communications industry. Before joining the staff at Laser Focus World in 2004, she held many product management and product marketing roles in the fiber-optics industry, most notably at Hughes (El Segundo, CA), GTE Labs (Waltham, MA), Corning (Corning, NY), Photon Kinetics (Beaverton, OR), and Newport Corporation (Irvine, CA). During her marketing career, Gail published articles in WDM Solutions and Sensors magazine and traveled internationally to conduct product and sales training. Gail received her BS degree in physics, with an emphasis in optics, from San Diego State University in San Diego, CA in May 1986.